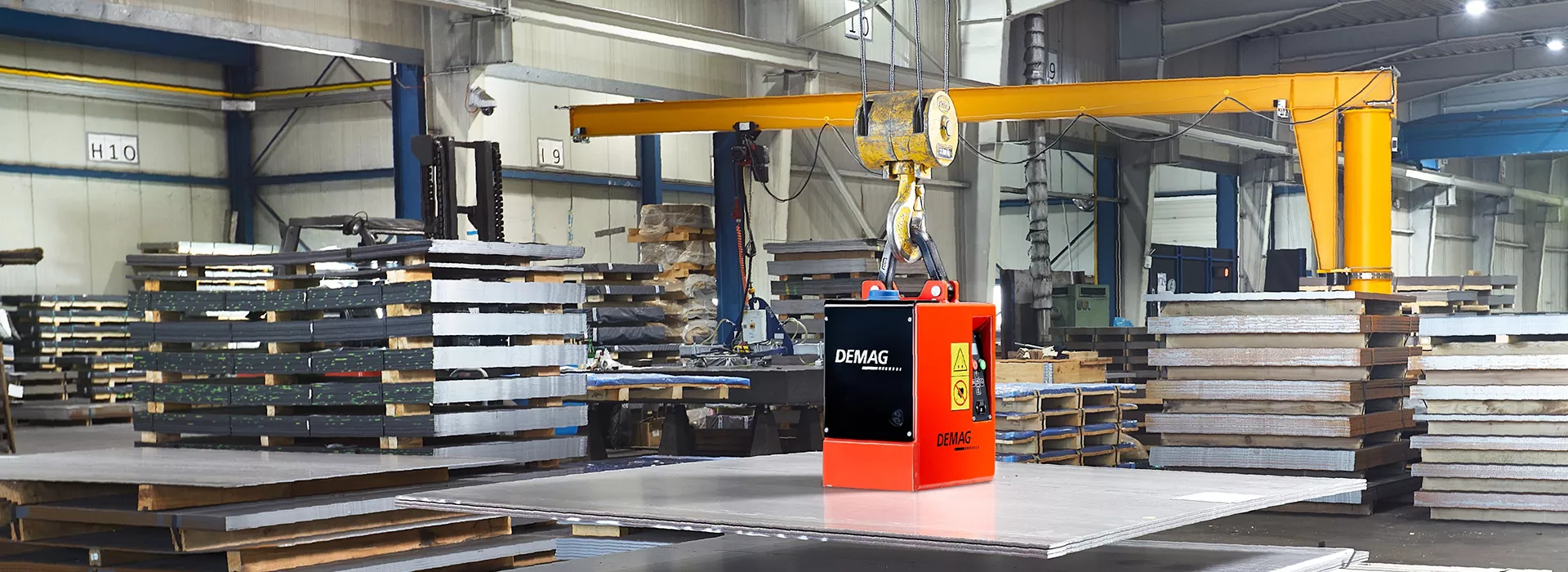
Load-lifting magnets at special steel company BESTAR
Handling steel to produce high quality tools, knives and saws
Lifting without attaching: handling sheet metal plates with the Demag DBM battery magnet
Company
Since the beginning of industrialisation, Remscheid has been a centre of the German tool industry. Many manufacturers of high-quality knives and saws have their home here, and BESTAR Stahlhandelsgesellschaft mbH has been providing them with special steels since 1978. In addition to hot-rolled wide and narrow strip, and cold-rolled strip, the product range also includes tool steel and HSS sheets, rust- and acid-resistant products as well as flat and round bars.
Originally BESTAR supplied the local saw and knife industry in the Bergisches Land region of Germany. Today, the company has branches in the USA (Atlanta) and China (Hong Kong) and supplies exacting manufacturers of industrial tools, saws and knives worldwide. As a specialised steel service centre, it also offers a wide range of steel grades.
Requirement
The majority of the steels are delivered as sheets of metal. BESTAR stores the cold and hot strip ready to resell. The material can be processed to a wide range of production depths to meet customer requirements. In both cases, the metal sheets need to be picked up and handled during storage and retrieval. With conventional lifting technology, this requires slings to be attached to all four corner points. The time required and the risk of an accident during operation must be taken into account in each case.
For this reason BESTAR was looking for an alternative solution that promised greater safety and better efficiency and productivity. It was clear that there was actually only one solution for this task – load-lifting magnets. However, the following questions needed to be answered: Is this solution as practical as expected? Does it meet with the approval of the operators? And which type of lifting magnet is the right one?
Solution
BESTAR managers decided to test the Demag DBM battery-powered load lifting magnets. With the DBM 2, magnetisable loads weighing up to 2 tonnes can be transported safely and efficiently. With a duty cycle of 50%, the battery magnets support the operator with up to eight hours of operation, i.e. for an entire shift. The charge level of the battery is always visible on the display on the magnet. The operator has the greatest possible freedom of operation because the DBM's separate DRC control unit works by radio control. This increases safety by allowing the operator to keep a safe distance away from the sheets and transport them from A to B with the best overview of the complete process.
It is particularly helpful for the employees at BESTAR to be able to detach the metal bundles from the magnet at different stations. This eliminates the need for multiple attaching and detaching operations and makes even more efficient use of working time.
Frank Schymura, Operations Manager at BESTAR, sums up the result: "There's no doubt about it, operators need to adapt and trust the magnet. If they do, they will benefit from a significantly easier and more ergonomic way of handling the sheets. And we save time and money in the process."
Special features
BESTAR's requirements are fully covered by the DSM's range of performance: The application – the handling of metal sheets – is typical for this type of load handling attachment. However, the DBM model series itself has some special features. This includes comprehensive and smart safety functions. For example, an automatic switch-on disabler prevents the load from being picked up if the battery voltage is too low: the load can only be picked up if the battery magnet and magnetised load are sufficiently connected to each other. An automatic power monitor constantly monitors the operating voltage and issues an acoustic warning if the voltage drops below the minimum operating value. The operator can therefore safely deposit the load and recharge the battery with a residual voltage for ten minutes of operation.
Another special feature of Demag DBM battery magnets is that by flicking the toggle switch on the radio control, the bottom sheet of a held stack of sheets can be released. This enables the time-saving positioning of individual sheets at different workstations in a single step. An additional feature is the demagnetisation function, which can be used to shake off chips and swarf, for example.
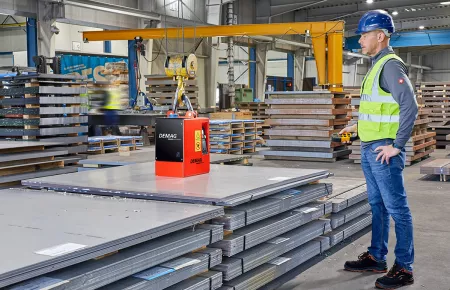
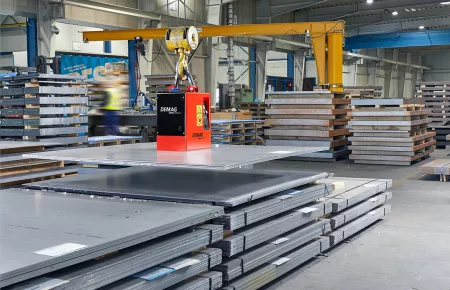
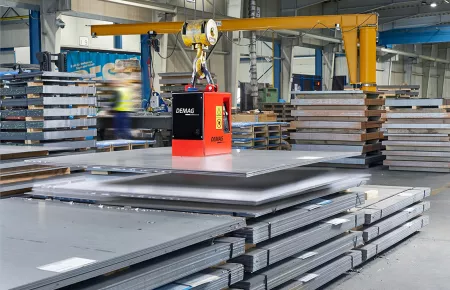
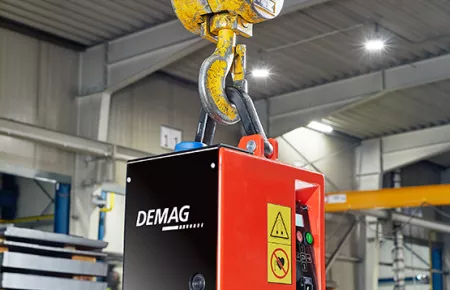