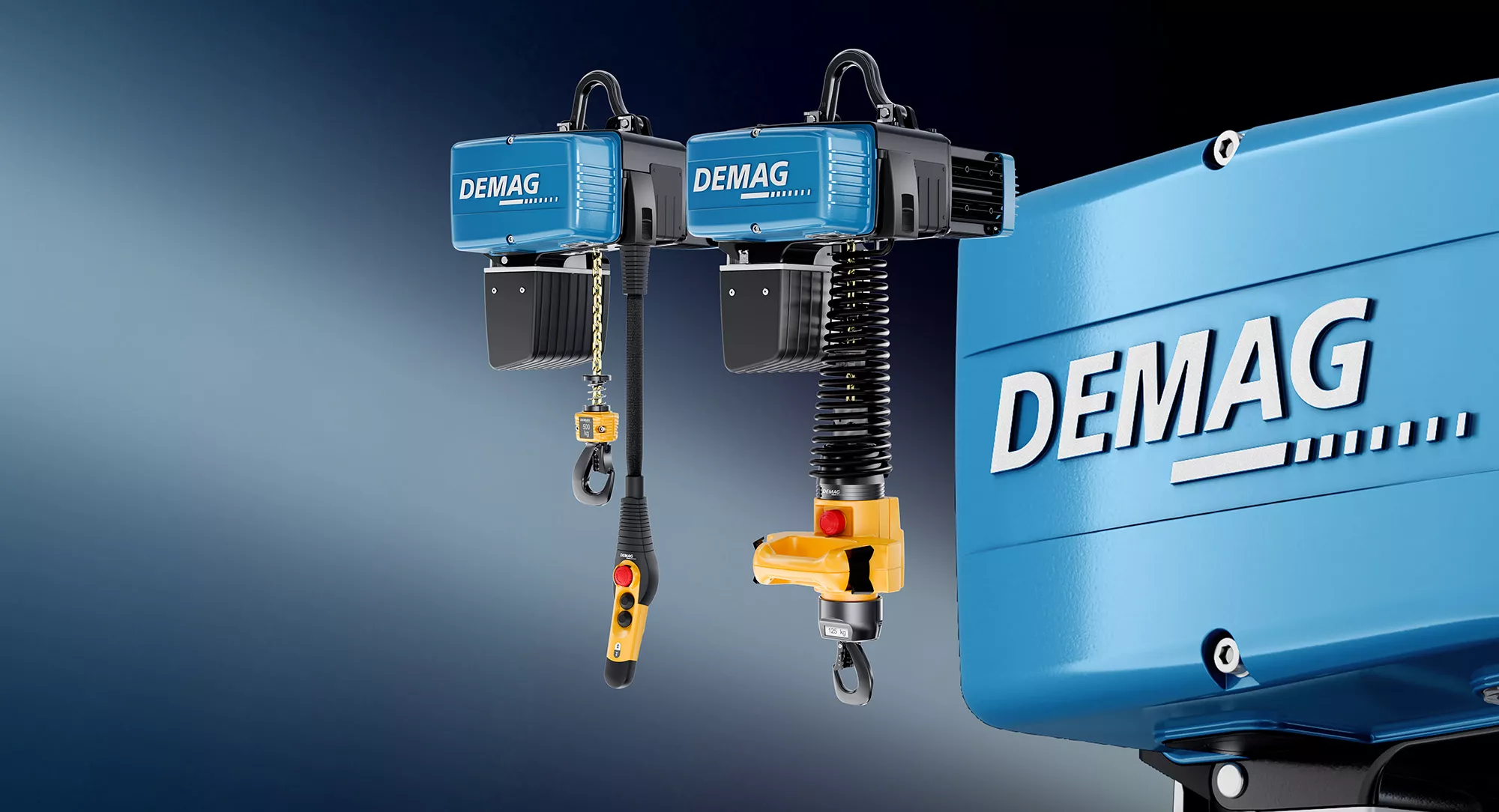
We deliver best performance
Powerful reliable light crane systems, crane components and drives are our core competence. As one of the world's leading manufacturers, we have been offering our customers a comprehensive portfolio of solutions for their material flow and logistics needs for more than 200 years – enabling them to achieve the highest levels of efficiency and performance.
Discover the world of Demag.
Become a Demag Official Country Partner!
We are known as a reliable partner in the world of industrial cranes and components for many decades: competence and experience are the foundation for a successful cooperation. If you are interested to work with us as a distributor in dedicated regions where we are not represented yet – we look forward to hearing from you.