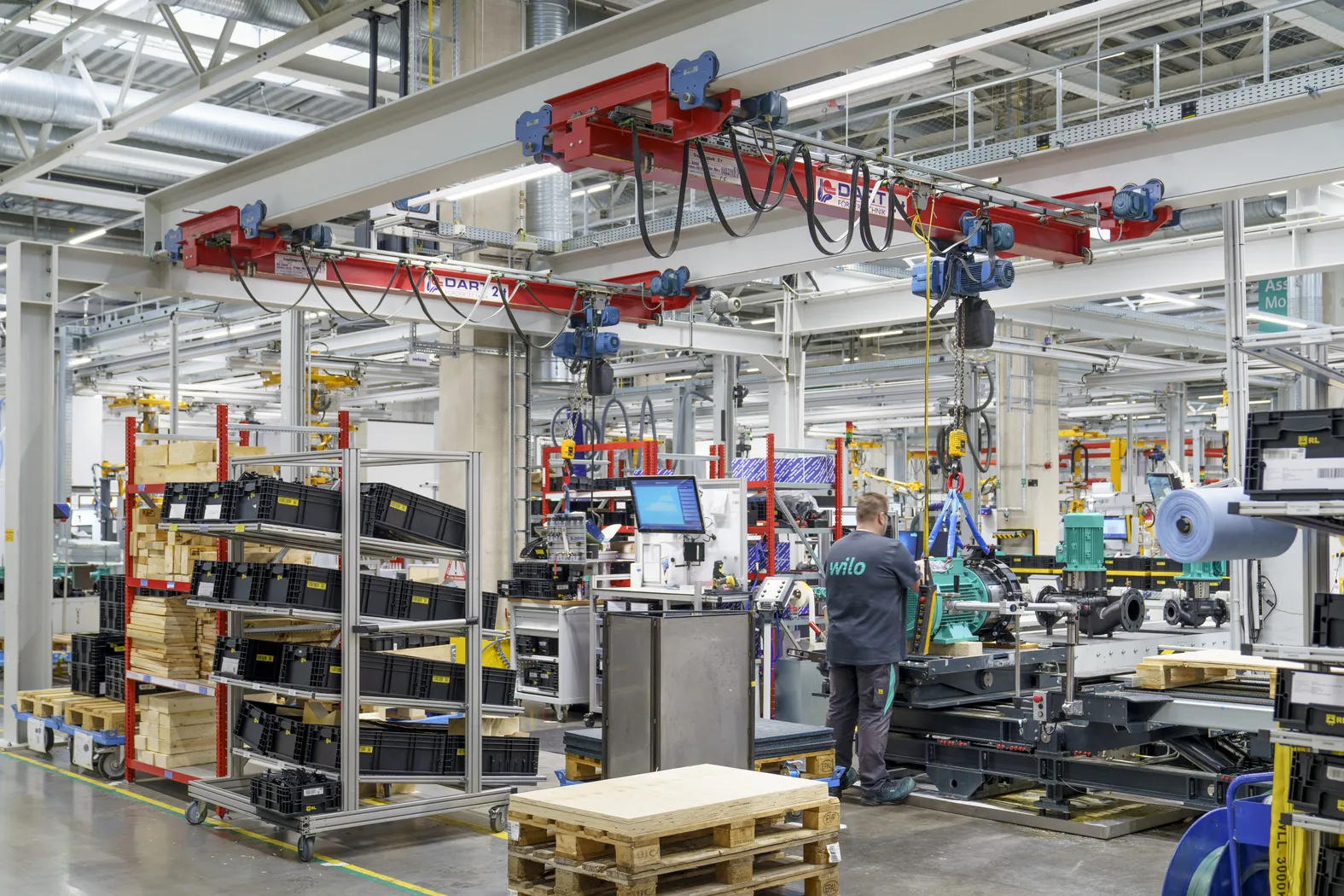
Smart crane concept for Smart Factory of the Year
Handling in Wilo’s Smart Factory 2024
Demag partner DART Fördertechnik supports material handling in Wilopark.
In the new, smart factory at the Wilo Group headquarters in Dortmund, all processes are digitally mapped and controlled. The actual material flow is also perfectly organised. Careful detailed planning means that every workstation allows both ergonomic and productive load handling. Wilo and DART Fördertechnik GmbH jointly planned the crane concept – and have been using the Demag KBK modular crane construction kit ever since.
A remodelling here, an extension there: this is how most successful industrial companies grow their production. Not so at Wilo in Dortmund. The long-established premium manufacturer of pumps and pump systems for building tech-nology, water management and industry has completely redesigned and rebuilt its headquarters, the Wilopark – including the production facility.
Excellence: the Wilo Smart Factory
What you can see from the skywalk of the completely newly built Wilo produc-tion facility is the physical material flow with (among other things) the Demag KBK system and driverless transport systems. You can also see, if you take a closer look, a very broad portfolio of products, systems and solutions that the fac-tory employees produce here.
This can only be achieved with extremely efficient, fully digitised production. State-of-the-art planning tools “orchestrate” and control the entire process. Com-pared to the old production facility, key figures such as inventories in production and throughput times have been reduced. This means that pumps can be produced in Dortmund in a highly economical and order-related manner, i.e. extremely flex-ibly – in the long term and in future also ordered by the customer via an online configurator.
This concept also convinced the judges of the most prestigious production compe-tition in the German-speaking region: they recently named Wilo’s Smart Factory “Factory of the Year 2024”.
Objective: Relieve the strain on employees
The planning of the new production workshops was based on the exact ideas of how production should operate in the future. The planners also consulted experts. The result: a fully digitalized factory that works with high efficiency and high speed. The relevant key figures such as throughput times, inventories in the supply chain and much more have been drastically reduced, even though Wilo was already producing and assembling using state-of-the-art methods.
As Wilo's portfolio is extremely broad and the average batch size in the glanded pump sector is 1.8 pumps per order, full automation is not a viable strategy in this area. Instead, employees’ intelligence and expertise are required. Their physical strength, on the other hand, is not the focus. Wilo sets very high standards in terms of ergonomics and health and safety. This is why all (assembly) work-stations where loads weighing more than 8 kg are lifted – and there are many – are equipped with lifting aids that are customised to the respective tasks.
Individual selection of workstation cranes and handling units
Wilo has DART Fördertechnik as a partner for this task (see text box), with whom the company has been working for many years. The Demag KBK light crane system has been available for more than 60 years. As a certified partner of Demag, DART is often called upon to equip workstations and is ideally suited to equip the Wilo project with its numerous options. Not just Demag KBK, but also the hoists, drives, control units and load handling attachments can all be customised or extended to suit the task in hand. This is a huge advantage for a factory that strives to constantly improve and create optimal conditions for its employees.
Steel structure concept creates flexibility
One basic idea that Wilo and DART came up with at the start of the project was to dispense with a wall or ceiling suspension for the handling systems on the individual assembly islands and lines. Instead, the runways for the suspension cranes are mounted on a gantry system.
DART Managing Director Axel Ditz: "With this Wilo is much more flexible. The travel paths and working areas can be easily changed and, above all, expanded if necessary." Another reason for this design: an impressive skywalk leads over the production area – an experience for every visitor and often a welcome shortcut for employees. However, the skywalk limits the working height and is not compatible with a hall crane at all. The planners had to do a lot of precision work here.
Diversity instead of unity
A walk through production (or across the skywalk) shows how versatile the intralogistics and the Demag KBK system at the Wilo factory are. Axel Ditz: “We have customised every crane at every workstation precisely to the transported goods and the respective work steps.” And that didn't just happen in theory: the employees were involved in the decision-making process.
Demag KBK suspension cranes are used for flat transport. They are used by employees to move pump components from the conveyor belt or from an automated transport system (AGV) to the processing machine and from there to further conveyor technology. Depending on the application, different Demag chain hoist series (DC-Com, DC-Pro) are used, as well as assistance systems in which the worker can easily guide the load to the destination with hand movements (DCMS-Pro Manulift, DCBS-Pro with “Balancer” function). These handling units are used at special workstations where the pump components are also tested. Particularly precise handling is required. One-handed operation promotes intuitive load handling for employees at their workstations.
Slewing jib cranes for ergonomic “picking”, hall crane for injection moulding tools
At other workstations, Demag KBK slewing jib cranes enable ergonomic picking work – once again with individually selected lifting equipment: basic chain hoist, DCMS-Pro Manulift or DCBS-Pro with balancer. Stephan Böing, project manager at Wilo: "The Demag KBK system offers many options, including support for operators when lifting and moving loads. We have used many of these options to be able to respond precisely to the requirements of our colleagues."
In one area, the planners deviated from the concept of the steel structure as a load-bearing structure and chose a “classic” hall crane with a Demag rope hoist – for good reason. Stephan Böing: "We also installed our own injection moulding in the new factory. As the tools for these machines weigh several tonnes, the only option here was a hall crane that can lift up to 3.2 tonnes. In assembly and other production areas, loads of up to 250 kg are sufficient, which can be easily dealt with by steel structures."
The final steps in the process chain show that the Demag KBK system really has been installed throughout the entire production process. A turntable installed by DART facilitates the handling of the fully assembled pumps and pump systems on the packaging lines – under a Demag KBK system with suspension cranes.
A concept that has proven itself
The Smart Factory has been in operation for some time now. In one area, the gantry structures of the Demag KBK system have already been adapted to changing requirements – with little effort. Stephan Böing: "We have been working on practical solutions with DART for years and we put a lot of thought into planning the new production facility together. Now you can say that we have achieved exactly what we imagined: a flexible workstation crane concept that can adapt to changing requirements. Since then, the Demag KBK system has proven itself at a wide variety of assembly, testing and packaging stations. And the colleagues are very satisfied."
Not an everyday project
For DART Fördertechnik GmbH, which has been a Demag partner since 1992, planning workstation cranes for Wilo’s Smart Factory was and is not an every-day project. Managing Director Axel Ditz explains the special features.
Demag: Mr Ditz, your company also plans and builds large cranes with high load capacities for demanding applications. Wilo has a lot of small workstation cranes. Why was this project a highlight for DART?
Axel Ditz: DART has been around for 33 years and we have indeed had bigger projects. But how often do you have the opportunity to really accompany such a comprehensive and detailed project from start to finish and make a contribution when the vision of a new factory is being realised? We hadn't done that before, and it was very special. We were very happy to contribute our expertise.
Demag: How did you come to work together in the first place?
Ditz: We have been working for Wilo for many years, in crane service and on new projects. Those responsible informed us that they would like to work with us on this project. We were very pleased with that.
Demag: Was using the Demag crane construction kit set from the start?
Ditz: We have been a certified Demag partner since 1992 and have designed and implemented many Demag KBK solutions. There is simply no alternative for such an application that is even remotely equivalent. The diversity is unique, which is why we were able to find tailor-made, ergonomic and always industry-appropriate solutions for every workstation, including at test stations and with semi-automated handling.
Demag: What have you learned from this project that you can recommend to other users of cranes and handling technology?
Ditz: Generally speaking, you should plan carefully and with attention to detail. After all, such a solution should last for many years. Wilo has implemented this principle in an exemplary manner. Future flexibility should also be taken into ac-count, as should the expertise of the employees. After all, they handle the lifting equipment on a daily basis, and their practical knowledge is helpful.
Demag: How did the collaboration work out over the course of the long project?
Ditz: Truly exemplary. We worked together confidently and very efficiently to find the optimal solution for every workstation and task.
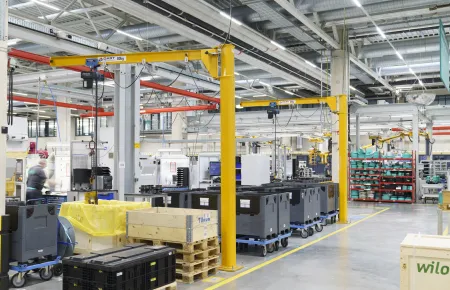
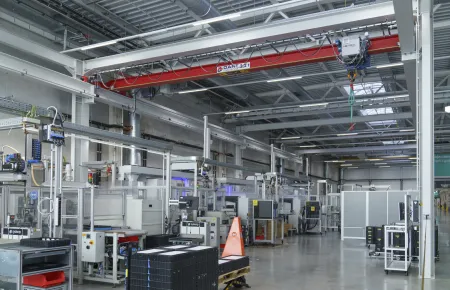
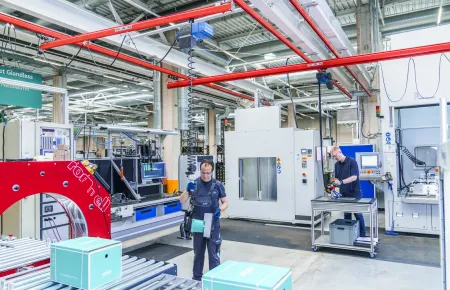
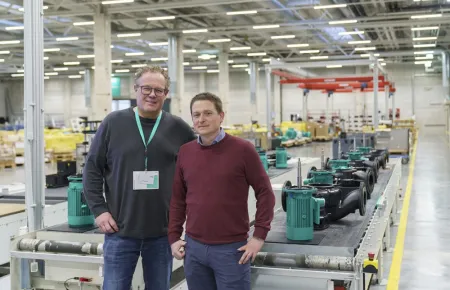