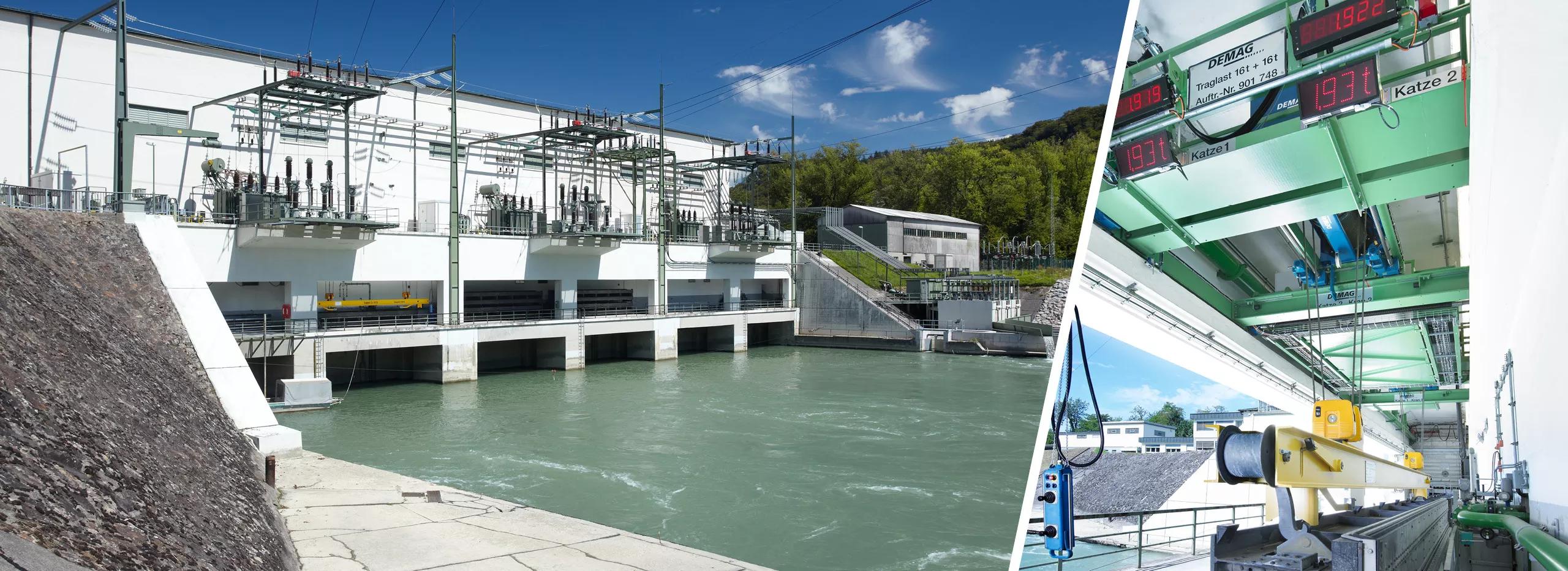
Natural energy generation
Demag modernises the hoist concept
Demag DH hoist unit positions dam beams
Company
The Albbruck-Dogern run-of-river power plant on the High Rhine is located right on the German-Swiss border. As a hydroelectric power plant, it uses the slope of the Rhine to generate environmentally friendly renewable energy. Along with a weir power plant built later, the operator Schluchseewerk AG generates an annual average of 650 million kilowatt hours of CO2-free electricity at this site, which is used to supply 180,000 households.
The water volumes required for power plant operation are supplied to the power plant channel via a weir channel. Three machine sets, each consisting of a generator and turbine, are installed in the power plant channel. To allow regular inspection work on the turbines, the turbines are sealed off from the water with the help of the dam beams and emptied. For this purpose, the 11-metre-long dam beams are lowered into the niches provided.
Requirement
Previously, this task had been performed by a double-girder overhead travelling crane which, after several decades, was long overdue extensive renovation. In the upgrade, Demag DH hoist units play a central role in raising and lowering the dam beams.
The requirements for the lifting concept were clearly defined:
- Complete replacement of the moving steel structural elements and the load bar
- Installation of two 16-tonne hoist trolleys, which can also operate in tandem
- Safety control by measuring the length of the hook path with large optical display
- Precise positioning thanks to frequency-controlled drives in three axes
- Drive concept with eight driven crane wheels and four trolley drives
- Secure year-round operation thanks to heated electric switchgear cabinets
- New installation of a power supply line with minimal space requirements for the cable accumulating section
- Adaptation and extension of existing pendant controllers
Solution
Proven hoist technology for precise handling
Positioning and removing the dam beams at depths of up to 22 metres requires high positioning accuracy. Two 20-tonne DH 2100 hoist units with a 4/2 reeving system prevent any hook travel. They are installed on two mechanically coupled trolleys that travel with a span of 3.54 metres on an 80-metre-long crane runway. By means of a selector switch on the pendant controller, the hoist units can be used individually or in tandem for loads weighing up to 32 tonnes. Both trolleys have a hook lead-off of 7,000 millimetres to secure the load bar for mounting the dam beams.
Further safety functions such as overload protection with summated load cut-off and a load spectrum recorder are integrated into the hoist units. An additional technical feature makes it easier for the crane operator to position a dam beam precisely: the length of the hook path is measured via rotary encoders on the hoist units and shown on large pivoting displays on the crane bridge. Starting from the reference point of the uppermost hook position, the personnel are thus shown the deposit position of a dam beam with centimetre precision, which can then be documented and precisely controlled for subsequent removal. Two additional large displays show the current weight held by the hoist units.
Special features
Additional safety with second brake
The operator Schluchseewerk AG also uses the hoist units to transport people in order to be able to carry out special inspection and maintenance work. The two DH hoist units were equipped with a second brake as a holding brake for this purpose. Their proper function can be checked via an additional button integrated into the ground control panel. A test function for the emergency limit switch and a tare button have also been integrated into the control unit.
All-wheel drive included
In addition to the high positioning accuracy in the long and cross-travel directions, year-round operation must also be ensured – even if the dam beams are only inserted and removed three times a year. Although the crane installation runs under a concrete roof protected against precipitation, the equipment is exposed to outdoor temperatures through the side opening along the length of the crane runway.
A total of eight travel unit combinations from the Demag modular drive system were selected for the drives used for the long-travel motions. These consist of DRS 250 wheel blocks with guide flanges on one side, which are driven individually by cylindrical motors. Wheel blocks with 160 mm travel wheel diameters are used for cross travel and are driven in pairs. Control for variable-speed travel and hoist operation is provided by Demag Dedrive Compact frequency inverters.
The trolleys are equipped with additional heaters for the switchgear cabinets. The region experiences cold winters, so the electronics are optimally protected against these weather conditions. The power supply system also took account of the effects of the weather and the confined space conditions: the track profile for guiding the trailing cable runs along the 80-metre-long crane runway and runs at a right angle at the end of the runway. With this space-saving solution, the cable accumulating section is located at the end position of the crane and the crane maintains the best possible approach dimensions. An ingenious lifting concept for generating natural electricity in southern Germany.
Your Contact
Image gallery
Image gallery
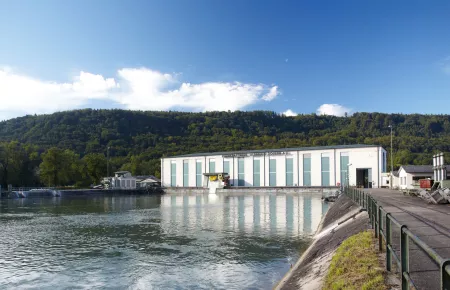
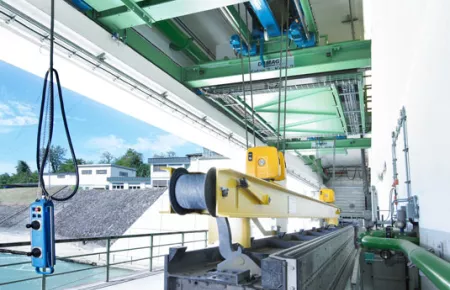
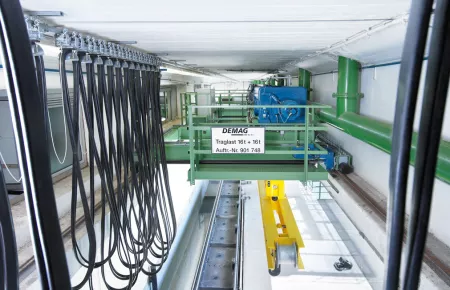
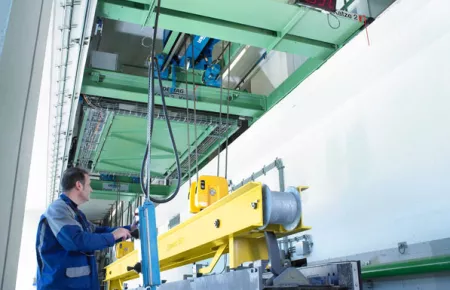