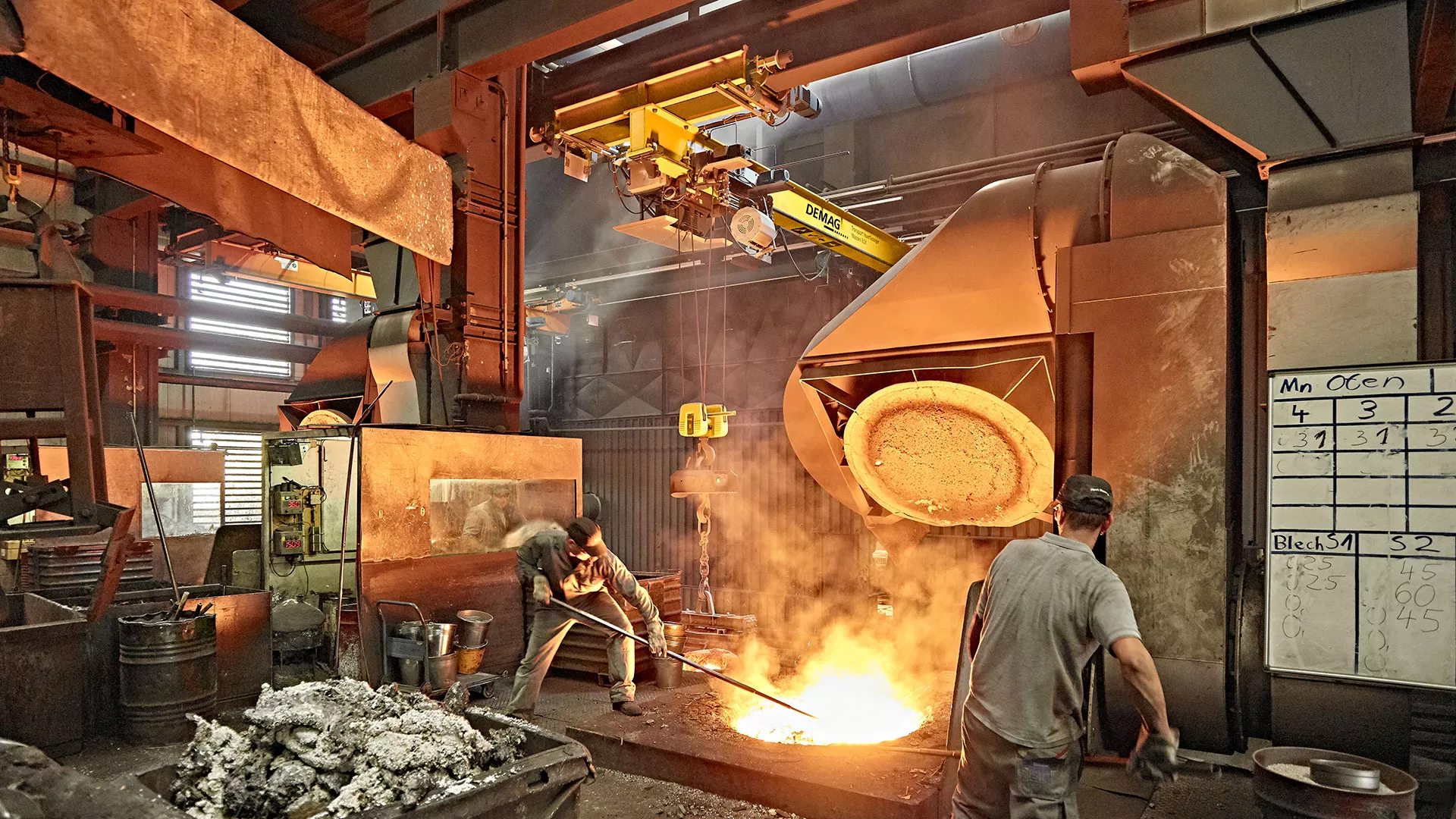
Hot, hotter, heat resistant
Safely handing molten masses
Two Demag foundry cranes for the SLR foundry
- Cranes for transporting goods with temperatures of 1500 °C
- Highest availability requirements under harsh conditions
- Demanding conversion, assembly in a narrow window of opportunity
SLR Giesserei St.Leon-Rot GmbH uses two Demag foundry cranes to transport molten cast iron. The cranes are based on the proven universal crane range but have been adapted to the extreme requirements of foundry duty thanks to numerous design features.
“Transporting molten materials”: This is the task, as specified by relevant standards, performed by the two Demag cranes that recently entered service at SLR Giesserei St.Leon-Rot GmbH.
The cranes, each with a rated capacity of 8 t, transport ladles of molten cast iron at a temperature of around 1500 °C, which they transfer from the melting furnaces to the casting cars that take the material to the mould line. There, the high-quality spheroidal-graphite cast iron is filled into the moulds. This is how a casting blank is created after a controlled hardening process.
Cranes such as these need to satisfy special requirements, which are laid down in standard EN 14492-2, among others, to ensure that the ladle cranes work safely and reliably under the extreme ambient conditions – which include abrasive dust as well as heat.
Replacement of two existing Demag foundry cranes
Demag experts can draw on decades of experience when designing such process-relevant cranes. The planners and operating engineers at SLR are well aware of this, as Demag had supplied two foundry cranes to St. Leon-Rot in 2002. Despite heavy use, these cranes had by no means reached the end of their life cycle after 16 years. However, growing demand for SLR’s casting expertise required the use of ladles for handling up to 3 t of molten material. The existing cranes would then have exceeded their load capacity limit of 5 t.
On the basis of this specification, Demag proposed to replace the 50.5-metre-long crane run-way and install two EKDE suspension cranes rated for foundry duty with a load capacity of 10 t (8 t unloaded). One of the advantages of this solution is that, on the one hand, cranes with tried and tested crane components are used, but on the other hand, all the requirements for the special ambient conditions can be met.
A crucial interface in the material flow
At SLR – and also in other foundries – such cranes work at the crucial material flow interface between melting furnaces and casting trolleys.
Matthias Meisberger, Head of Technical Planning at SLR: “If the cranes fail, the foundry will come to a standstill. And that doesn’t just apply in the event of a lengthy period of downtime. We have a maximum period of 15 minutes to transport the material from the melting furnace to the mould line. If the spheroidal-graphite cast iron has not been cast by then, the treatment effect wears off and it turns into conventional grey iron, which is of no use to us.”
This is because SLR is a specialist in sophisticated components made of spheroidal-graphite cast iron – an iron casting material whose properties match that of steel and with which SLR produces, for example, high-strength travel unit components for construction and agricultural machinery of leading manufacturers.
Designed for safety and redundancy
For this reason, the two new cranes installed at SLR are designed for maximum availability. The drive is protected by heat shields and the crane bridge enclosure is installed exactly in the centre of the bridge because the heat is higher at the girder ends. The crane bridge itself is exceptionally rigid to avoid deflection and extreme oscillation.
All four trolleys of the travel unit are driven and equipped with a manual brake release function, which enables the crane also to operate with only two working drives. An automatic centrifugal emergency brake serves as a catching device in the (unlikely) event that the drive unit in the hoist fails.
The two cranes – which are equipped with collision protection – are each controlled by a Demag D3 radio control system. This ensures that the operator can maintain a safe distance from the load. The DMR rope hoist has a bottom block with a hook as a load handling attachment and, like the entire crane, is designed for an ambient temperature of up to 55 °C. An integrated weighing device (also suitable for high temperatures) shows the operators the weight of the filled ladles, which can weigh up to 8 t in total. Other options are aimed at ensuring high availability of the cranes in the not only hot, but also dusty environment – for example, self-adjusting brushes that continuously sweep the abrasive dust off the crane runways.
Conversion and assembly within a short time
Only a relatively short period of two weeks was available to dismantle the old installation and install the crane runways and crane during the factory break. The SLR and Demag fitters worked closely together here because the power supply also had to be renewed and structural changes made. After the end of the holiday, the foundry staff were able to work with the new cranes, which have since proven their worth under the demanding conditions.
Mathias Meisberger: “Finishing touches are being made gradually. It is important that the cranes run smoothly from the start, and they do.”
The finishing touches also include modification of the tilting mechanism on the ladles. The hand wheels for manual operation can still be seen in the picture. SLR has now, however, switched the casting ladles to electric motorised tilting at the touch of a button as planned – for good reason.
Mathias Meisberger: “The smaller crucibles were still easy to operate manually. With the new, larger crucibles, however, the operators would have to use the hand wheel to tilt 3 t of molten material, more than 80 times per shift. The electric tilting mechanism makes the work much easier and also improves safety.”
Your contact
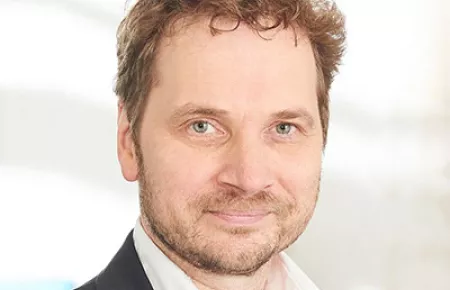
Christoph Kreutzenbeck
Ruhrstrasse 28
58300 Wetter
Germany
Image gallery
Image gallery
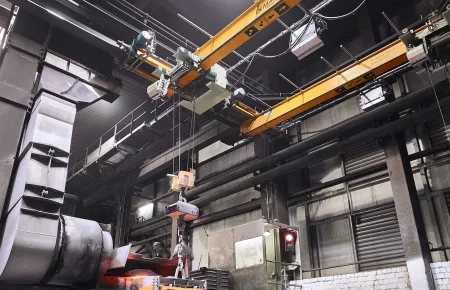
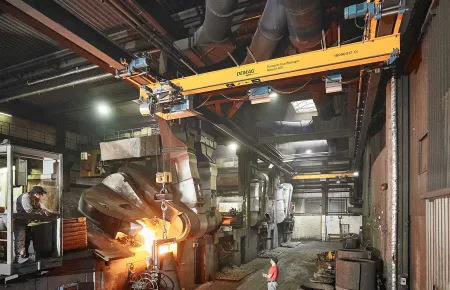
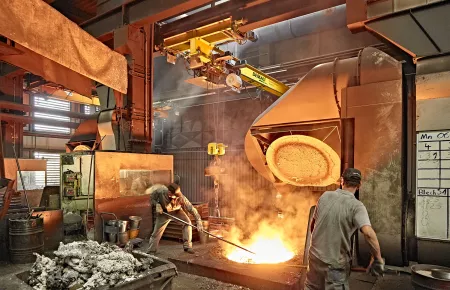
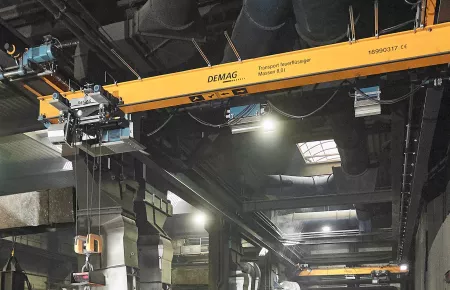