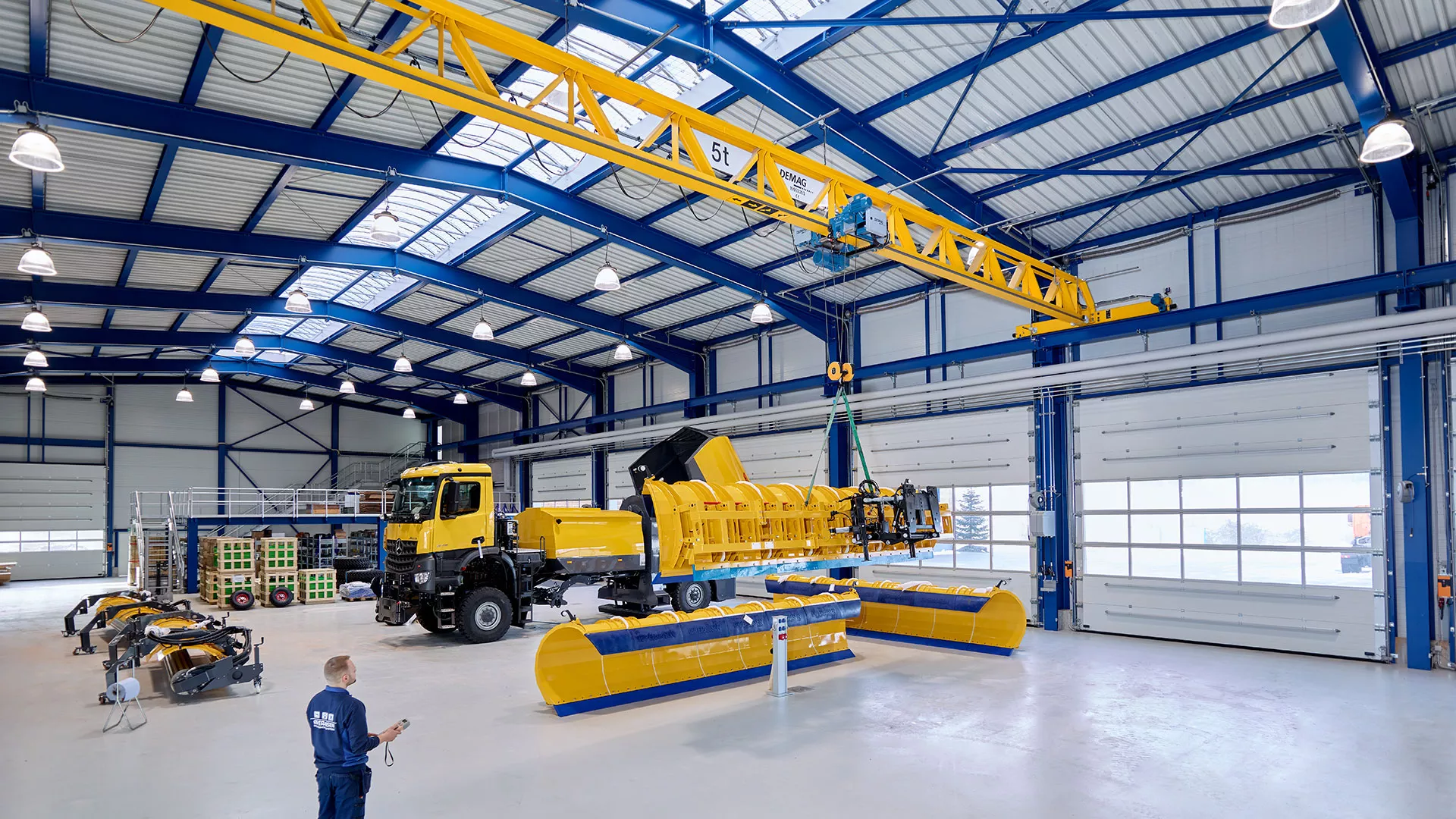
One customer. A variety of applications. Demag Cranes.
Load handling in production of snow removal equipment
Demag single-girder cranes for Øveraasen Deutschland GmbH
Customer
Øveraasen AS provides Norwegian Snow How with snow removal systems for road and rail. The family-owned company offers self-propelled snow blowers for snow removal at airports as well as snow ploughs and blowers for mounting on trucks or trains. The sale of used equipment and after sales support round off the product range. Øveraasen can look back on a company history of more than 110 years and is now represented with locations and partners worldwide.
Requirement
The German subsidiary Øveraasen Deutschland GmbH is responsible for sales and after-sales support for Central Europe. In addition, truck chassis for snow removal systems are produced and converted at the newly built plant in Grafenhausen, Germany. The overhead handling between the individual production and assembly areas, as well as the dimensions and weights of the components, require the use of cranes.
The trucks are converted and produced in the assembly bay. There, the exact positioning of the components on the truck chassis is to be made noticeably easier for the employees through the use of two cranes. The operator should be able to view precise installation of the components from different angles. During construction of the new bays, special attention was also paid to providing uniform illumination of the workplaces, which should not be impaired by the crane design.
For handling smaller components and spare parts, three additional cranes are needed at different production sites. The load weights of the goods in the metal workshop, the hydraulics workshop and the welding shop are lower, but exact positioning when feeding the machines is just as important as in the assembly bay. In addition to precise adaptation to the flat building structure and safe use of the installations, cost efficiency has to be considered for the three cranes.
Solution
EVKE and DMR
In the assembly bay, two Demag EVKE cranes help with assembly of components and truck chassis. The V-type girder is characterised by torsional rigidity and the ability to allow light to pass through. This promotes safe working in a well-lit production environment. The improved oscillation characteristics can reduce dangerous load sway. This is of great importance, for example, when the chassis and engine are combined.
The smart SafeControl system monitors and ensures safe operation of the crane. A two-stage cut-off limit switch arrangement prevents the crane as well as the travelling hoist from colliding with the end stops. When the first limit switch is reached, the long or cross-travel motion switches to slow speed. Once the second limit switch is reached, the long or cross-travel drives are switched off, gently braking the travel motion. Load sway, which can cause injuries and damage to snow ploughs or blowers, is thus – in addition – prevented electronically.
Both cranes are equipped with a Demag DMR modular rope hoist and, with their load capacity of up to 5 t, can even transport entire truck chassis without any problems. The rope hoists feature the Demag DualDrive two-wheel drive and therefore have higher traction, which means that the load is subjected to even fewer oscillations. The components are thus transported safely, quickly and smoothly.
Thanks to the Demag DRC-10 radio control system, crane operators can move around the load at a safe distance. This enables them to select the desired position at the required angle at any time and to position the large-volume snow ploughs on the truck precisely and efficiently.
Short interview with Mr Simon Eckert, Øveraasen Deutschland GmbH
Demag: Mr Eckert, why did you prefer the Demag solution?
Simon Eckert: Basically, the overall package from Demag was right. The proposed cranes met our requirements for safe and efficient materials handling. During the discussion with the sales engineer, we were shown useful safety options, which our employees have come to appreciate very much in their daily work.
Demag: What are the advantages of using Demag products?
Simon Eckert: Let’s take the example of converting a truck to a snow clearing machine. In this case, components of the truck need to be removed and refitted or completely different components must be used. In the past, two employees were needed for some of the construction steps to fit the sometimes quite large components safely. Thanks to the mobility around the truck provided by the radio control and the precise and exact control of the crane, this can now be performed by one employee. Meanwhile, their colleague can already be deployed elsewhere.
Demag: What feedback have the employees given you so far?
Simon Eckert: Their feedback has been exclusively positive. The cranes fully meet our daily requirements. The combination of radio control, safety functions and the travel characteristics of the cranes considerably improve our assembly and repair processes.
EPKE and DC-Com
In addition to the two V-type cranes, three Demag EPKE profile-section girder cranes support production. One of the EPKE cranes, with a span of 4.37 m and a low headroom dimension, is precisely adapted to the conditions on site. The trolleys all have a compact design with minimum approach dimensions. This means that every centimetre of the limited space can be optimally utilised.
Load handling is made easier for operators by smoother crane travel – thanks to optional horizontal guide rollers. In combination with the Demag DC-Com chain hoist, Øveraasen opted for an economical overall package for everyday needs.
The DSE-10C controller is equipped with a height-adjustable control cable and can be positioned along the crane girder. The ergonomic design allows the employee to operate the relevant crane with ease.
Special features
The smart SafeControl system offers maximum safety in crane operation. The long-travel limit switches and safety control system support the crane operator electronically, helping to avoid any accidental damage in the crane’s operating environment.
The DRC-10 radio transmitter facilitates ergonomic control within a larger radius of the crane, making daily tasks easier for the crane operator.
The DC-Com chain hoist is uncompromisingly good. The DC unit provides low-sway load handling thanks to smooth cross-travel starting and braking motions. The slipping clutch has automatic cut-off, thanks to the speed-monitoring function. Generous specification of the gearbox and the fact that the gearbox and clutch are maintenance-free for up to 10 years, and the brake for up to 5 years, result in a long service life for the chain hoist.
Your contact
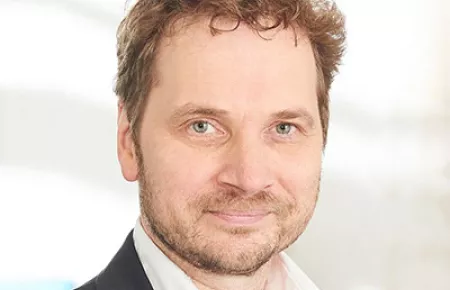
Christoph Kreutzenbeck
Ruhrstrasse 28
58300 Wetter
Germany
Image gallery
Image gallery
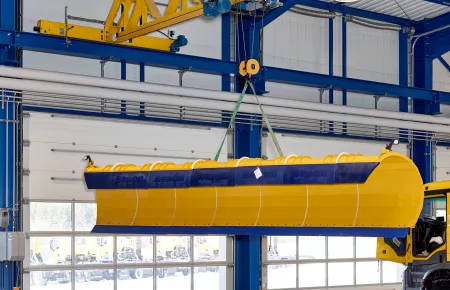
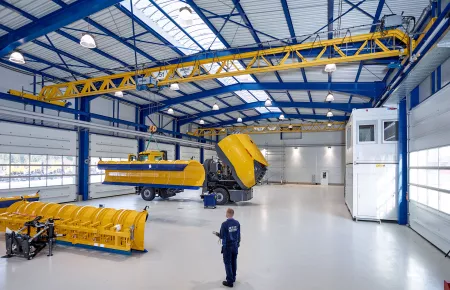
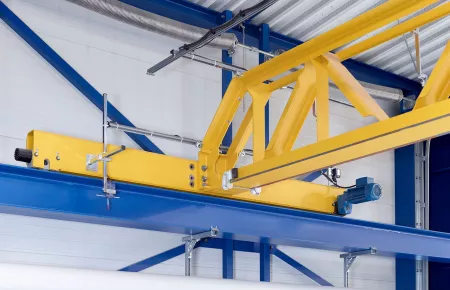
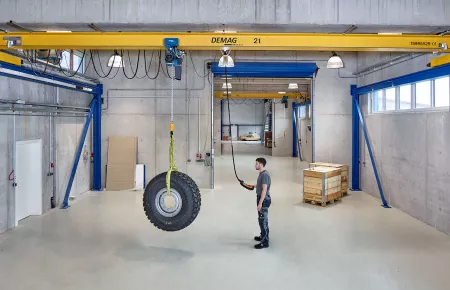