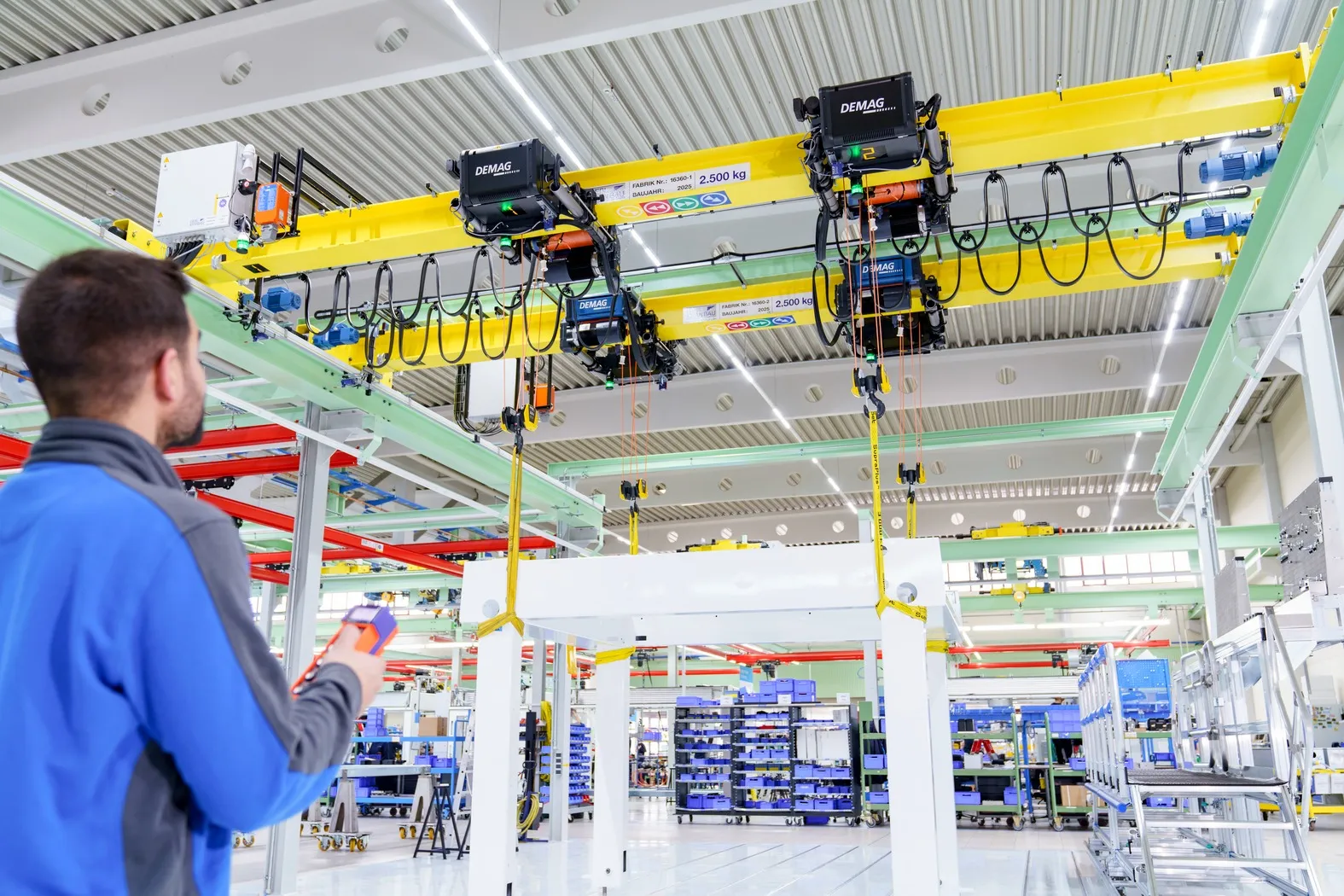
A completely clean handling solution
Handling during assembly of packaging machines
Innovative lifting technology for modern production at Gerhard Schubert GmbH in Crailsheim
Company
Highly efficient, automated and convenient to operate via an ergonomic human-machine interface: these are the characteristics of every packaging machine from Gerhard Schubert GmbH’s extensive product range. And from Schubert's point of view, it is only logical that the workplaces and stations in its own production are designed according to the same principles.
Requirement
That’s why Schubert turned to Liebl Kranbau when planning a new production area – and this was not the first time. The task was divided into two parts: handling of frames and racks of the machine modules and, in an adjacent assembly area, the handling of components that are installed in these modules.
Solution
DHR rope hoists: state-of-the-art crane technology for frame assembly
For handling frames and racks, Liebl’s crane experts designed a crane duo that uses the latest Demag lifting technology. Two cranes with a span of around 8 metres travel on a common 25-metre-long elevated crane runway and are each equipped with two Demag DHR rope hoists that can lift loads of up to 2.5 tonnes.
Schubert is thus one of the first users of this new rope hoist series, which is characterised by a compact design with low dead weight, among other things. The two-stage hoist motor enables fast lifting and lowering of the load as well as precise positioning. The CANBus communication standard (optional and selected by Schubert) allows independent monitoring of safety-relevant parameters. Christoph Liebl, Technical Manager of Liebl Kranbau: "This is an important option, because our customer places great importance on occupational safety throughout the entire operation." In addition, on the subject of ergonomics and user-friendliness, both Demag cranes can be conveniently operated by radio remote control.
Clean elements: synthetic rope material
Schubert is also one of the first users of Demag rope hoists with synthetic ropes, which are offered as an option for DHR rope hoists. The synthetic rope material is high-strength and at the same time about 85% lighter than a comparable steel rope. At the same time, there is much less wear on the rope drums and sheaves, and there is no need for lubrication. This increases the service life of the rope guiding components and reduces service requirements. These factors are - without a doubt - very beneficial. But it was something else that ultimately tipped Schubert's decision in favour of synthetic ropes: due to the reduced wear and abrasion and the lack of lubrication, this rope material is ideal for cranes that operate in an environment which demands high levels of cleanliness. And that’s exactly how Schubert operates. Christoph Liebl: "The machines work in clean, often hygiene-sensitive applications, when packaging food and pharmaceuticals. That’s why they are also installed in a clean environment – right from the start."
Putting safety first
The crane experts at Liebl chose the DHR wire rope hoists precisely because of these properties of synthetic ropes, the precise positioning and the extensive safety equipment – and because Schubert is always open to using innovations in crane and handling technology. Christoph Liebl: "We've been designing crane systems for Schubert for many years – always with the latest generation of hoists."
The two cranes are "kept at a distance" by means of photosensors; automatic cross-travel and long-travel limit switches at the ends of the track are standard for Schubert – the focus is safety.
Tandem and quadro-hoist
In normal operation, the operator controls one of the two crane bridges with one of the two hoists. If necessary, they can select tandem mode and then control both hoist units synchronously. But that’s not all. Christoph Liebl: "Alternatively, the operator can also transfer the second crane installation to a radio transmitter. They can then control all four hoist units together in quadro mode. This is often done because the large-volume, rectangular frame constructions that are created here can thus be handled in a balanced and therefore secure manner."
The overhead cranes are configured on the basis of Demag Crane Sets, which are supplied as assembly-friendly complete equipment with all (assembly) accessories. Liebl experts opted for Demag DRS-M wheel blocks with the right Demag geared motor to provide sufficient power for driving the cranes. The cross-travel and long-travel drives are infinitely variable thanks to Demag frequency inverters.
Workstation cranes: KBK with durable chain hoists
When equipping the assembly workstations for the adjacent assembly of units with handling systems, Schubert – together with Liebl – opted for a high-quality and proven Demag solution: the Demag KBK light crane system. The workstations are spanned by four KBK systems, each with two crane bridges. A total of eight Demag DC-II E-chain hoists with a load capacity of 500 kg each take care of vertical transport. The second generation of the DC chain hoist series, which has been tried and tested for decades, is a new addition to the Demag hoist portfolio. Its features include an extensive safety package with automatically engaging slipping clutch and 24 V contactor control. In addition, the classification of the groups of mechanisms has been increased compared to the predecessor model series, ensuring an extended service life with low service requirements. And the adjustable control cable fits Schubert’s aspiration to offer operators maximum ergonomics and operating comfort at the workplace. In addition, the standard equipment with seven-segment display offers high system transparency as status and error display. And thanks to the additional magnifying glass function, this is also clearly visible from a greater distance.
Schubert has chosen additional options for the KBK system, which also offer a plus in terms of safety and operating comfort. On the installed KBK systems, the energy is not transmitted via trailing cables but via internal conductor lines. This reduces the risk of collision with other trailing cables in the workstation.
Innovations that have proven themselves in practice
All in all, Liebl and Schubert have chosen innovative solutions that set standards in terms of user-friendliness and occupational safety. Cleanliness has also been prioritised. The new production area proves its worth every day and meets all of Schubert’s requirements. The employees are also completely satisfied.
Special features
Innovative lifting solutions for safe and forward-looking operation: The DHR rope hoist offers a high level of versatility and productivity. From simple lifting applications to high-performance rope hoists with smart assistance and convenience features, the DHR meets all demands for highly efficient load handling.
The synthetic synthetic rope is made of high-modulus polyethylene fibres and is approximately 85% lighter than the steel rope option. The rope can be used indoors and outdoors and in a temperature range of -10°C to +45°C. Due to its physical properties, there is no wear on the rope drum and sheaves, and lubrication is not required.
Liebl Kranbau: The solution experts from Swabia
Liebl Kranbau GmbH has an excellent reputation in the industry and stands for decades of experience and innovative system solutions. And, of course, for Swabian entrepreneurial spirit and unbridled ingenuity. Since the company was founded in 1997, it has been steadily expanding under the management of its founder Franz Liebl. In Ostfildern near Stuttgart, the family-owned company develops innovative and customer-oriented system solutions that the crane manufacturer installs and maintains at the customer’s premises after completion. As a Demag partner, Liebl uses the entire Demag range for crane, handling and drive technology.
No reservations about new crane technologies
In a brief interview, Christoph Liebl, Technical Manager at Liebl Kranbau, explains the special features of the project that the crane experts from Ostfildern have successfully completed with Schubert – with the latest crane technology.
Mr Liebl, what was special about this project?
Christoph Liebl: Schubert is a demanding customer who places high demands on ergonomics and occupational safety and is always open to innovation. Those responsible are also not afraid to use completely new products and technologies if this promises to be beneficial, above all in terms of safety and ergonomics. It’s always fun to work with such a customer and drive an innovative project forward. Schubert already uses six generations of cranes with Demag lifting technology, which we have had the privilege of designing.
And on the technical side?
Christoph Liebl: The “Quadro” control technology is particularly important here: operating two cranes with two hoist units each via a radio control system is something very special. The same applies to one of the first deployments of both the DHR hoists and the synthetic ropes. Both solutions proved to be the best from the start, Schubert made the right decision.
Why synthetic rope? And how does this new rope material prove itself?
Christoph Liebl: There are several reasons to use this synthetic rope material. Schubert focused on cleanliness: less wear, no lubrication. But the long service life of the ropes was also a factor in the decision. It was just right!
What benefits does your position as a partner in the Demag network bring you?
Christoph Liebl: We get comprehensive support and access to the latest technology. The very broad and technically high-quality range is another factor. We often design comprehensive and very specific overall solutions for crane and handling technology. With Demag, we can serve ourselves in the sense of 'one-stop shopping'.
Foto Galerie
Foto Galerie
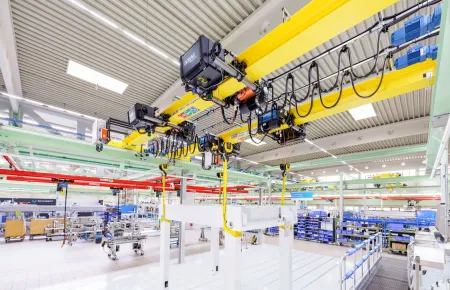
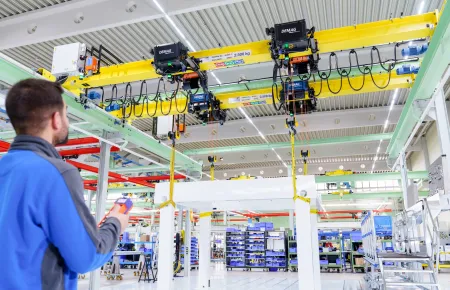
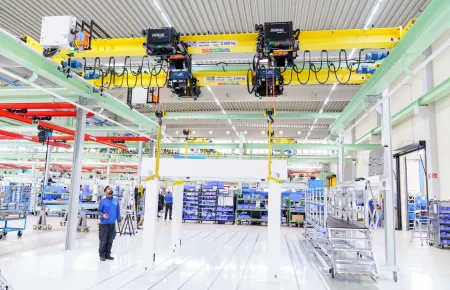
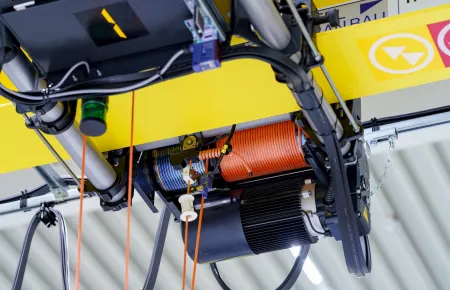