Demag to supply three process cranes for “green” power generation at E.ON biomass power plant in Hürth
- Two grab cranes continuously feeding wood as fuel
- Further grab crane to remove ash
- Remote control via Demag Remote Operating Station (ROS)
- Entering service in October 2021
Demag will supply three process cranes equipped with grabs for an ambitious project to serve a major combined heat and power plant. The order has been placed by Green Steam Hürth GmbH, a subsidiary of E.ON, which will build a biomass power plant with an output of 20 MW of electricity and 87 MW of heat energy at the site of the UPM paper plant in Hürth near Cologne, Germany. This project sees the first use of Demag Remote Operating Stations, which enable the remote control of crane systems.
The power plant, where E.ON is investing some EUR 110 million and is due to go online in mid 2022, will provide heat for the Hürth paper factory and, at the same time, feed renewable energy into the grid. UPM produces more than 300,000 tonnes of high-quality newspaper made from recycled paper at the factory every year.
The location has been well selected, because the paper production operation needs a lot of heat (in the form of steam) and combined heat and power generation is particularly efficient. In this case, it is also particularly sustainable, since the power plant is fuelled by wood residues, which E.ON procures in the region. According to E.ON, this will provide an efficient and reliable supply of virtually CO2-neutral energy to an industrial operation that requires a lot of energy.
Demag will deliver two process cranes for the automated continuous supply of wood to fire the boiler in the power plant. Some 45 tons of wood need to be fed around the clock every hour. The two double-girder cranes, which have a load capacity of 14 tonnes and a span of 20.6 meters, will travel on a crane runway measuring almost 100 meters in length. All of the crane travel drives feature variable speeds; energy recovery when braking and lowering loads enhances the energy efficiency of the cranes. Hydraulic multi-jaw grabs with a capacity of 12 m³ will be used as load handling attachments.
Cranes continuously feeding fuel
The crane systems will largely operate in automatic mode. The Demag Warehouse Management System (WMS) software will ensure, for example, that the bunkers are cleared, that the boiler is continuously fed with the required quantities of wood and that both cranes complete their coordinated tasks.
Not only the fuel, but also the ash as a residual material is handled by a Demag crane. The Demag engineers have specified a smaller double-girder process crane with a 5.4-tonne load capacity and a hydraulic grab for this task. The three crane systems will operate under challenging conditions with high humidity (up to 100%) and high dust levels. They are ideally suited to meet these requirements, as Demag has already designed and delivered many cranes for refuse recycling installations and biomass power plants all over the world.
Demag ROS: crane control system with multiple views of the operating location
Since it is very difficult to view the entire very long fuel bunker from a conventional crane cab, the project engineers at E.ON decided in favour of a special Demag option. If the cranes need to be operated under classic manual control, this can be done via a Remote Operation Station (ROS), which also serves as a monitoring station when the cranes are running in automatic mode.
ROS is a remote control station that includes all operating functions of a process crane with a crane operator seat – except that the operator does not view the crane and its operating environment direct, but via a widescreen monitor that shows images from several cameras in real time. The screen layout can be configured to meet process requirements, with information relevant to the process being automatically displayed.
In theory, a station like this can be located very far from the crane. At the Hürth biomass power plant, it is installed in the control centre, so the operator can benefit from improved working conditions. Thanks to the many installed cameras, he has an even better view of the process than from a crane cab. This is because the cameras can also “look” where the normal field of vision would be restricted.
Press contact
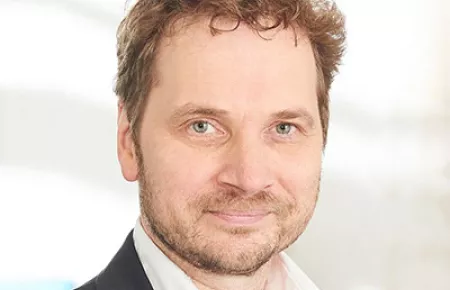
Christoph Kreutzenbeck
Ruhrstraße 28
58286 Wetter
Deutschland