Demag WMS: bespoke material flow solutions to manage automated stores
It is not a matter of course for a crane manufacturer to develop and offer its own warehouse management system. In every case, it provides major benefits from the user’s point of view. The Demag Warehouse Management System (WMS) can be tailored to meet individual customer requirements – also using state-of-the-art simulation tools. The system encompasses the entire intralogistics process from the goods-receiving, intermediate and shipping stores as well as in the production process, including yard management, i.e. the organisation of truck traffic on the customer’s premises.
In many areas of industry, such as in the paper and steel sectors, process cranes usually perform the task of carefully storing and retrieving rolls and coils. Thanks to the overhead logistics, the available space can be fully utilised as no travel paths are needed at ground level. In addition, cranes can achieve high handling rates and they can be integrated direct into the overall material flow of a manufacturing facility.
This level of integration already places demanding requirements on the hardware side of the material handling equipment. No less demanding are the requirements to be met by the information-processing level, which ranges from control of the crane installations and the entire warehouse management system to the interface to the customer’s ERP system. This requires a fully integrated flow of information, which needs to be adapted to meet the individual demands of the specific project.
It all begins with consulting and analysis
Due to the complexity of this task, warehouse management systems (WMS) offered on the market for standard applications are often only a second-best solution, as they cannot fully satisfy specific requirements. For this reason, some 30 years ago Demag already developed its own system, the Demag Warehouse Management System (WMS), which differs fundamentally from other conventional warehouse management systems. One central difference is that every WMS is individually tailored to match the relevant application. That is why each WMS project starts with consulting, which in turn starts with a comprehensive analysis of the storage and material flow processes by the Demag industry sector experts.
Considering alternatives – with simulation tools
The analysis forms the basis of a concept study in which various storage and material flow solutions are developed and reviewed. This is (also) done with state-of-the-art simulation tools that enable a virtual trial of the developed concepts. The entire logistics process including any manual storage operations can be simulated. This approach has been proven to be more economical and more efficient than a planning process without simulation, although it requires a little more time and investment at the planning stage. However, the owner of the store can save costs over the entire life cycle of the installation. In addition, he has the certainty that the investment in the storage material handling equipment is utilised in the best possible way in daily operation.
Yard management simulation included
Besides the process chain between production and the store, simulation of the logistics processes also includes the loading and unloading operations at the ramps as well as the forklift and truck traffic on the owner’s premises. Experience shows that this holistic review of the material flow enables much greater potential improvements to be identified than an isolated view of the storage and retrieval processes. On this basis, for example, the owner can significantly cut the time that trucks spend on the premises and ensure faster turnaround times.
Individual software package as an end-to-end solution
The software package tailored to control the customer’s specific storage and material handling systems is only developed following this comprehensive preparation. At the shopfloor level, the Demag WMS has interfaces to the control system for the process cranes and other material handling equipment; at the higher level, it usually has an interface to the owner’s ERP system. This results in end-to-end information system, which enables the entire material flow throughout the company and in the store to be controlled for optimum results and to meet actual demand.
Example: paper manufacturer’s shipping store
An example of a recent application underlines the benefits of a tailor-made WMS compared to a standardised solution. A paper factory has doubled its annual production capacity to some 500,000 tons by investing in a new paper machine. The new machine produces some 1,500 kilometers of corrugated base paper every day. The quantities of rolls that have to be stored and retrieved every day are correspondingly high.
For this reason, the company had a new shipping store built with a capacity of 12,270 tons. As in the already existing store, two Demag process cranes provide for the fully automated handling of the paper rolls in this store. In an area measuring 66 x 30 metres, the rolls, which have a maximum diameter of 1,500 mm and a maximum weight of 4.2 tons, are automatically transported to the storage locations assigned to them by the higher-level Demag WMS. They are stacked up to a height of 15 metres in the store.
System handling performance was rated at 54 rolls per hour for single storage and retrieval operations by simulation in advance, i.e. during the consulting phase. 58 rolls can be achieved with combined storage and retrieval cycles. The Demag WMS enables the travel paths of both cranes to overlap – that accelerates the material flow.
Simulating and optimising entire on-site traffic flow
The in-house material flow on the finished-goods side becomes much more complex with the second store, as there are now two stores for different product groups. This led to the question of how to organise the material flow and the truck movements on the yard in the best possible way.
This was also determined by using the simulation tool. Specifically, this means that the Demag experts generated a scale simulation model for the entire outbound logistics of the paper factory. First of all, the control strategies for the storage, retrieval and re-organisation processes in the two automatic stores were optimised. In a second step, the entire traffic flow on the premises was simulated – with all trucks and forklifts – on the basis of real demand scenarios. Among other things, this revealed that it is more efficient for the trucks to approach two loading points one after the other, rather than providing a central ramp for both shipping stores. The results of the simulation were put into practice with a Yard Management System. As soon as the truck driver has logged in and the truck has been weighed, this system guides him through the factory and assigns him a position and time slot in the goods-out area.
As a result, average truck waiting times have been significantly reduced from 45 to 17 minutes and the maximum number of trucks in the waiting zone has been cut to eight from previously 18. Following installation, these figures were verified in a performance test and match the figures previously calculated via simulation. The paper factory logistics team are also highly satisfied because they were able to improve the level of service at their location.
Expertise goes beyond cranes
This example of a recent application also demonstrates the efficiency and practical application of the simulation tools employed for this project, as well as Demag’s ability to improve the entire intralogistics processes in addition to the cranes and storage system. The supplier has industry-specific expertise that is used to offer customers solutions that are tailored to meet their specific needs from planning through to commissioning. At the same time, it demonstrates the benefits that result from a leading international crane manufacturer, who develops, continuously maintains and adds new functions and modules to his own warehouse management system.
Automatically generated: configurable modules/storage strategies
With its comprehensive range of storage strategies that can be defined and configured, the Demag WMS forms the optimum basis for bespoke solutions. Storage operations can be automatically generated and performed according to the selected strategies. Examples for paper roll storage and retrieval strategies.
- Order-related stacking
- Stacking by types
- Roll sizes
- Safety criteria
- Keeping inventory fresh (first in/first out)
- Storage area selection/priority zones
- Priority-based retrieval lists (before inventory is reorganised)
Store reorganisation
- Consolidation of small orders
- Separation of stacks into single product types
- Consolidation of stacks by types
Visualisation of the processes belongs, of course, to the WMS scope of delivery. For example, this includes information on the contents of the store, visualisation of the crane movements, roll movements, roll characteristics and loading lists. In this way, the customer has continuous inventory control and damage to the paper rolls and the associated loss of paper can be avoided.
The Demag WMS is used in many projects all over the world. The majority of installed systems can be found in the paper industry, with more than 70 stores already supplied. Automated crane-served stores are also operated with the Demag WMS in the bulk-handling and recycling industries. These range from stores in a cement factory and refuse incineration facilities to power plants that utilise renewable resources, as well as stores used for the processing and storage of wooden panels. The same also applies for storage in the steel-processing sector: (process) crane owners can benefit from a bespoke warehouse management system in applications ranging from production stores for sheet and plate metal to shipping stores for steel and aluminium coils.
Your Contact
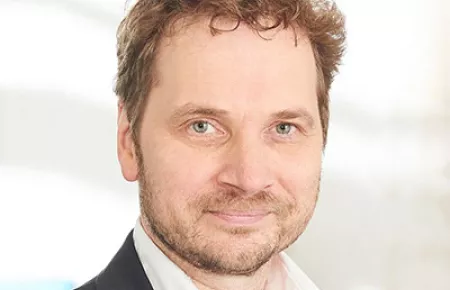
Christoph Kreutzenbeck
Ruhrstrasse 28
58300 Wetter
Germany