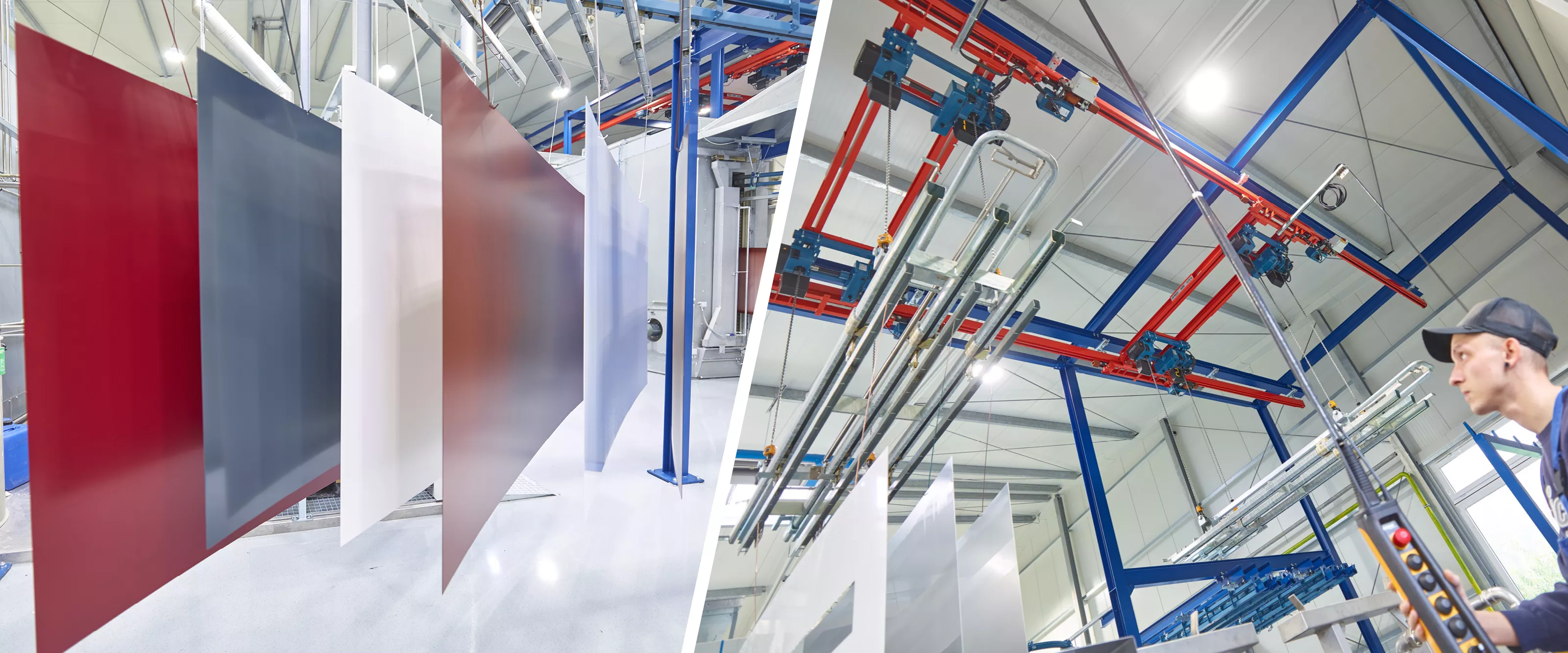
Modułowy system dźwignicowy KBK umożliwia elastyczne łączenie różnych procesów produkcyjnych
Demag Modułowy system dźwignicowy KBK
Przygotowanie ręczne – automatyczna produkcja
Przy budowie nowej instalacji do powlekania elementów aluminiowych producent elementów drzwiowych świadomie stawia na połączenie automatycznej linii transportowej z ręczną obróbką wstępną. Pomost pomiędzy tymi procesami tworzy system suwnic podwieszanych wyposażonych w równolegle sterowane podwójne wciągniki łańcuchowe.
Mecklenburger Bauelemente GmbH jest spółką-córką firmy Rodenberg Türsysteme AG, jednego z wiodących na rynku specjalistów od wypełnień drzwiowych wykonywanych na zamówienie. Zakład spółki-córki w Cramonshagen koło Schwerina jest jednym z czterech niemieckich zakładów produkcyjnych, najbardziej wysuniętym na północ. W kompleksie, który został otwarty w 1992 roku, produkowane są na zamówienie elementy do wypełnień drzwiowych, takie jak ościeżnice, półprodukty i panele z aluminium.
Ze względu na zwiększoną ilość zamówień, istniejąca instalacja do nakładania powłok od pewnego czasu pracowała z pełną wydajnością w trybie 24/6. Aby odciążyć tę instalację i stworzyć dalsze możliwości produkcyjne, operator zaplanował budowę drugiej hali nakładania powłok. W ciągu zaledwie dziewięciu miesięcy na terenie zakładu wybudowano nowy budynek i uruchomiono kompleksową instalację.
W hali o powierzchni 1.600 m² odbywają się wszystkie etapy procesu nakładania powłok, od przygotowania do wykończenia powierzchni. Cztery kabiny natryskowe do lakierowania proszkowego oraz piece do wypalania połączone są za pomocą automatycznie sterowanego systemu power-and-free, który został zaprojektowany i zainstalowany przez firmę Sapp Anlagenbau z Eslohe. Przed obszarem produkcyjnym znajduje się strefa przygotowania zamówień z dziesięcioma wannami zanurzeniowymi. Tutaj operator celowo wykorzystuje procesy manualne przez wdrożenie dalszych, zautomatyzowanych procedur.
Michael Kock, kierownik produkcji w Mecklenburger Bauelemente GmbH, wyjaśnia powody tej decyzji: „W naszym zakładzie wszystkie elementy są planowane i produkowane zgodnie ze specyfikacją klienta: od małej aplikacji o wielkości dziesięciu centymetrów kwadratowych po panele o wymiarach półtora na trzy metry. Chcemy wieszać materiał zgodnie z kolejnością przyjęć, a nie sortować go najpierw według wymiarów.”
Przy systemie czysto automatycznym trzeba by było za każdym razem wcześniej ustawiać czasy zanurzania materiałów i proces obróbki wstępnej byłby za każdym razem inny. „Dlatego zdecydowaliśmy się na manualną strefę wstępną i manualnie sterowaną technikę dźwigową do załadunku wanny. Zachęciły nas również doświadczenia z naszą istniejącą instalacją, która działa niezawodnie od 17 lat.”
Integracja w proces
Proces produkcyjny w Cramonshagen został zaprojektowany z myślą o wysokiej elastyczności. Części są dostarczane do hali nakładania powłok bezpośrednio z sąsiednich hal produkcyjnych według zamówienia, rejestrowane za pomocą kodu kreskowego i ręcznie wieszane na jednym z 60 wózków systemu power-and-free.
Kock informuje: „Przekazywane elementy - niezależnie od ich wielkości - są taktowane bezpośrednio w bieżącym procesie produkcyjnym w celu wykończenia powierzchni na podstawie zamówienia, obróbka odbywa się w krótkim czasie, a następnie ma miejsce zwrot do bieżącej produkcji w celu ostatecznego montażu.”
Do przenoszenia elementów zainstalowano podwójny tor szynowy z modułowym systemem dźwignic Demag KBK z wózkami wyposażonymi we wciągniki. Dzięki modułowej budowie systemu KBK można było dopasować instalację dokładnie do wymagań. Mocowanie do konstrukcji hali uzyskano za pomocą własnych zawieszeń systemowych KBK. Tor jezdny suwnicy o długości 35 m wykonany z profili KBK-II-R o rozstawie kół 3 m łączy wlot, wanny i stację przeładunkową z pozostałymi urządzeniami technologii przenośników. Dzięki wyposażeniu profili torowych w zintegrowany szynoprzewód zasilanie jest chronione w obrębie profilu, dzięki czemu okablowanie wzdłuż toru nie jest konieczne.
Trzy identyczne wózki o zoptymalizowanej wysokości, każdy wyposażony w dwa podwójne wciągniki łańcuchowe LDC-Pro-D, poruszają się po torze dwuszynowym. Udźwig na hak: 125 kg. Każdy podwójny wciągnik łańcuchowy posiada mechanicznie zsynchronizowane przebiegi łańcuchów, które umożliwiają precyzyjne przenoszenie ładunków z trawers. Takie rozwiązanie konstrukcyjne skutkuje dłuższą żywotnością łańcuchów, ponieważ nie są wymagane dodatkowe zespoły zmiany kierunków łańcuchów. Dwustopniowe wciągniki łańcuchowe podnoszą z dwoma prędkościami podnoszenia 4 i 16 m/min, dzięki czemu możliwe jest zarówno precyzyjne pozycjonowanie, jak i szybkie przenoszenie trawersów.
Możliwość precyzyjnego pozycjonowania
Ze względu na duże obciążenie podczas zmiany roboczej wciągniki łańcuchowe zostały zaprojektowane zgodnie z grupą FEM 4m. Dla zapewnienia długotrwałego zabezpieczenia wciągniki już w standardzie posiadają wysokiej jakości ochronę antykorozyjną w postaci powłoki proszkowej. Dokładne pozycjonowanie wózków na torze odbywa się za pomocą ciernych napędów jezdnych typu RF 125 z silnikiem E22-C z modułowego systemu, które mogą poruszać się z prędkością 7 lub 27 m/min. Przebieg procesu: Operator przesuwa pierwszy wózek z trawersem zamocowanym na czterech hakach (rysunek, strona 5) dokładnie do pozycji końcowej odcinka przenośnika i w ten sposób zamyka [1]przebieg odcinka. Teraz trzy wózki wyposażone w elementy aluminiowe można przenieść obok siebie na trawers.
Następnie pracownik podnosi trawers z toru, przesuwa wózek nad jedną z czterech kąpieli odtłuszczających i opuszcza w niej ładunek. Po rozpoczęciu zanurzania wózek jest gotowy do następnej operacji przenoszenia do jednej z dziesięciu pojedynczych kąpieli, w których następuje wytrawianie, płukanie i przygotowywanie produktów aluminiowych do aplikacji koloru. Po upływie indywidualnie określonego czasu przebywania w basenie zanurzeniowym, trawers zostaje ponownie wyprowadzony z wanny. Za pomocą przełącznika wyboru wciągniki mogą być przesuwane indywidualnie za pomocą dwóch prowadnic łańcucha, a trawers jest ustawiany w pozycji pochylonej.
„Ten proces ma ogromne znaczenie dla szybkiej obsługi”, mówi Kock. „Uzyskana pozycja pochylona wciągników przyspiesza odsączanie cieczy, zanim przejdzie ona do następnej kąpieli.”
Sterowanie dwoma podwójnymi wciągnikami łańcuchowymi odbywa się za pomocą podłączonej do kabla kasety sterowniczej DST 7, którą obsługuje się za pomocą wysięgnika w ergonomicznej pozycji z pomostu wzdłuż wanny. Za pomocą przełącznika wyboru można ustawić funkcje pracy pojedynczej lub w tandemie (rysunek strona 4). Funkcja tandemu zapewnia dokładne pozycjonowanie czterech prowadnic łańcucha przy wspólnej pracy wciągników.
W przypadku niezamierzonego zatrzymania wciągnika łańcuchowego - np. z powodu zadziałania wyłącznika krańcowego - natychmiast zatrzymuje się również drugi wciągnik. Po ostatniej kąpieli zanurzeniowej trzeci wózek podnosi trawers (rysunek, strona 7) i wprowadza go - analogicznie do stacji odbioru - na odcinek przenośnika. Stąd elementy trafiają do automatycznej sekwencji linii transportowej, by w końcu otrzymać żądaną przez klienta aplikację kolorystyczną (rysunek strona 2).
„Po uruchomieniu naszej instalacji planowaliśmy przepustowość od 40 do 60 wagonów na godzinę - w zależności od poszczególnych wielkości konstrukcyjnych”, przekonuje Kock. „Cel ten osiągnęliśmy już po krótkim czasie dzięki połączeniu procesów automatycznych i obsługi ręcznej. Urządzenie dźwigowe do obsługi elementów konstrukcyjnych w znacznym stopniu przyczynia się do naszej zdolności do realizacji celów, które postawiliśmy sobie w zakresie elastyczności i jakości.”
Galeria zdjęć
Galeria zdjęć
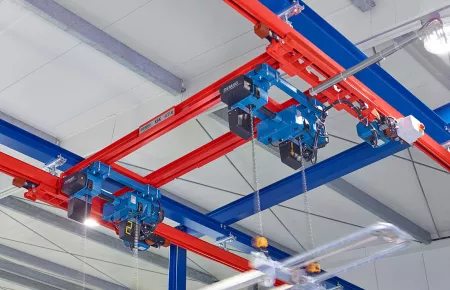
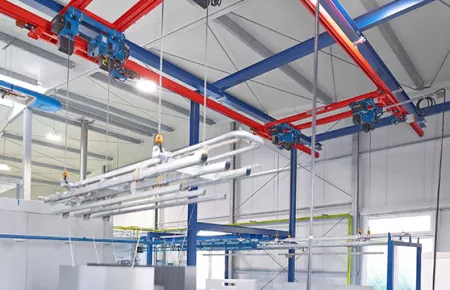
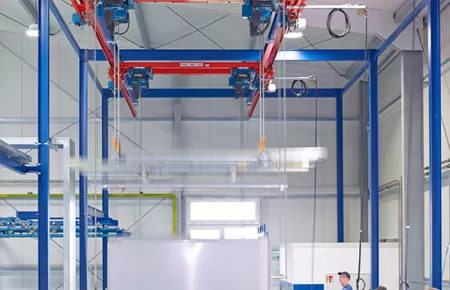
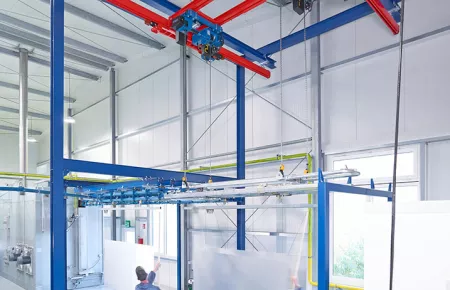