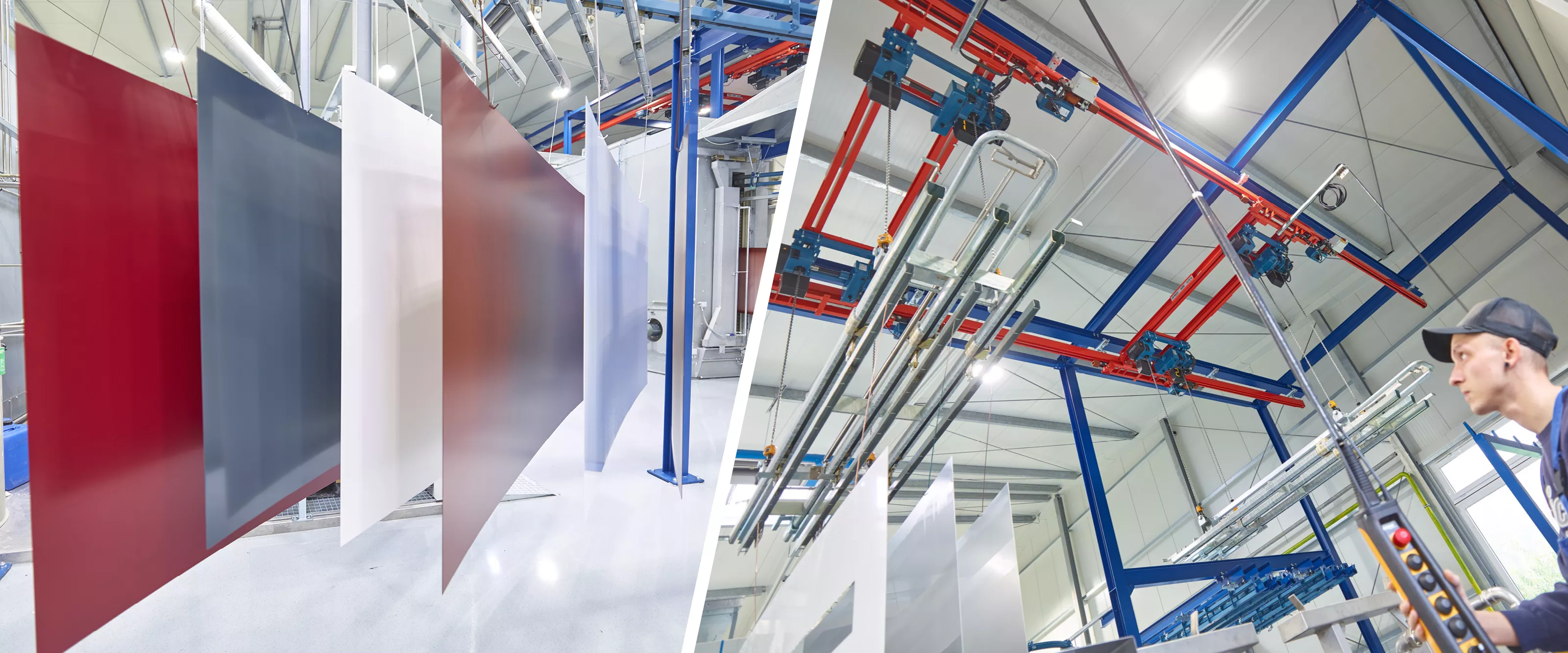
Sistema de içamento modular KBK permite uma interligação flexível de diversos processos de produção
Demag Sistema de içamento modular KBK
Preparação manual – produção automática
Ao conceber um novo sistema de revestimento para peças de alumínio, um fabricante de elementos de portas optou por escolher uma combinação de linha de transporte automática e tratamento prévio manual. Uma ponte rolante suspensa, com talhas de corrente duplas que podem ser controladas em paralelo, une estes dois processos.
A Mecklenburger Bauelemente GmbH é uma subsidiária pertencente à Rodenberg Türsysteme AG, uma das especialistas líderes de mercado de painéis de portas personalizados para residências. A fábrica desta subsidiária fica na cidade alemã de Cramonshagen bei Schwerin, sendo a que fica mais ao norte das quatro unidades. Neste complexo, inaugurado em 1992, são produzidos elementos sob medida para painéis de portas, como molduras, produtos semiacabados e painéis em alumínio.
O crescente número de encomendas exigiu que o sistema de revestimento existente passasse a funcionar com ocupação total durante 24 h por dia, 6 dias por semana. Para otimizar a ocupação deste sistema e maximizar sua capacidade, a empresa utilizadora planejou construir um segundo barracão de revestimento. Uma nova e complexa instalação foi construída e comissionada na unidade em apenas nove meses.
No barracão de 1.600 m² são realizados todos os processos de revestimento, do preparo até o tratamento de superfícies. Quatro cabines de pulverização para aplicação de pintura a pó são interligadas aos fornos de secagem por uma instalação Power-and-free, que foi planejada e instalada pela empresa Sapp Anlagenbau, de Eslohe, na Alemanha. Uma área própria para a preparação para a aplicação, com dez pontos de imersão, antecede a área de produção. Ali, a empresa adota processos manuais propositalmente, para preparar os demais procedimentos automatizados.
Michael Kock, gerente de produção da Mecklenburger Bauelemente GmbH, explica o motivo para tal decisão: "Em nossa fábrica são planejados e produzidos todos os componentes de acordo com as instruções do cliente, desde pequenas aplicações de dez centímetros quadrados até placas inteiras de 4,5 metros quadrados. Queremos acolher o material do jeito que está, sem ter que fazer uma separação prévia por tamanho."
Em uma instalação totalmente automatizada, a cada mudança seria necessário fazer o ajuste dos tempos de imersão dos componentes, e toda vez o processo de preparação seria diferente. "Foi por isso que optamos por uma área de preparação manual, com tecnologia de içamento de operação manual para o transporte entre as imersões. Nossa experiência com o sistema confiável que já usamos há 17 anos também contribuiu para a nossa decisão."
Integração aos processos
O processo de produção em Cramonshagen, na Alemanha, é orientado para uma alta flexibilidade. Dependendo do pedido os componentes são trazidos diretamente dos barracões de produção vizinhos até as instalações de alimentação, onde são lidos os respectivos códigos de barras, e então inseridos manualmente em um dos 60 vagões da instalação Power-and-free.
Kock completa: "Seja qual for o tamanho, os elementos que chegam entram diretamente no processo de produção corrente, por ordem de encomenda e já cadenciados, para o tratamento de superfícies, onde são rapidamente processados e encaminhados à produção corrente rumo à montagem final."
Para a movimentação dos componentes foi instalada uma via dupla do sistema de içamento modular KBK da Demag com carro de elevação da Demag Cranes & Components. Graças à construção modular do sistema KBK foi possível adequar a instalação perfeitamente às exigências. A fixação na estrutura do barracão foi feita com as suspensões próprias para o sistema KBK. Um caminho de rolamento de 35 m de comprimento composto por dois perfis KBK-II-R, com largura de três metros, abrange as estações de acolhimento, imersão e transferência para a linha de transporte. Os perfis da via incorporam uma linha condutora integrada, que faz a alimentação elétrica por dentro dos perfis de forma protegida, dispensando o cabeamento ao longo da via.
Três carros do mesmo modelo, com altura otimizada, equipados com talhas de corrente duplas do tipo LDC-Pro-D percorrem essa via dupla. Capacidade de carga por gancho: 125 kg. Cada talha de corrente dupla dispõe de uma saída de corrente mecanicamente sincronizada, que possibilita a movimentação de carga precisa para travessas. A solução construtiva permite maior vida útil para as correntes, pois dispensa inversões de corrente adicionais. As talhas de corrente trabalham em duas fases com duas velocidades de elevação, de 4 e 16 m/min, sendo capazes de oferecer um posicionamento de precisão e de mover travessas rapidamente.
Posicionamento com precisão
Devido à alta demanda dentro de um mesmo turno de trabalho, as talhas de corrente são projetadas segundo o grupo FEM 4m. O equipamento de elevação dispõe de proteção anticorrosiva a pó de alta qualidade e durável por padrão. O acionamento de translação por roda de fricção do tipo RF 125 com motor E22-C do sistema modular executa o posicionamento de precisão dos carros na via de rolamento, que pode ocorrer, opcionalmente, com 7 ou 27 m/min. O procedimento: um operador move o primeiro carro com uma travessa suspensa nos quatro ganchos (imagem da página 5) com precisão até a posição final da linha, encerrando [1]assim o percurso. Três carros com elementos de alumínio são transferidos paralelamente na travessa.
Por fim, o colaborador suspende a travessa da via, move o carro por cima de uma das quatro imersões desengordurantes e abaixa a carga nela.
Com o início do procedimento de imersão, o carro está pronto para o próximo procedimento de movimentação para uma das próximas dez imersões, em que os produtos de alumínio a serem revestidos são tratados, lavados e preparados para a subsequente aplicação da p[1]intura.
Decorrido o tempo individualmente prescrito no respectivo tanque, a travessa se eleva saindo da imersão.
Um seletor permite mover as talhas individualmente com duas saídas de corrente, levando a travessa a uma posição diagonal.
"Esse procedimento é muito importante para uma movimentação rápida", afirma Kock. "A posição diagonal agiliza o escoamento do líquido durante a transferência até a próxima imersão."
O comando de ambas as talhas de corrente duplas é feito pela botoeira com cabo DST 7, operada a partir de um braço em posição ergonômica ao longo do trajeto das imersões. Através de um seletor é possível ajustar as funções de operação simples ou em tandem (imagem da página 4). O funcionamento em tandem assegura o posicionamento de precisão na operação conjunta das quatro saídas de corrente das talhas.
Caso ocorra uma parada involuntária de uma talha de corrente, causada, por exemplo, pela ativação de uma chave de fim de curso, a segunda talha também é interrompida imediatamente. Depois da última imersão, o terceiro carro recebe a travessa (imagem da página 7) e a deposita na linha de transporte, de forma similar à estação de acolhimento. Dali, os componentes seguem no modo automático da linha de transporte para receber a pintura desejada pelo cliente (imagem da página 2).
"Depois do ramp-up de nossa instalação planejamos uma produtividade de 40 a 60 vagões por hora, dependendo dos diferentes tamanhos", continua Kock. "Atingimos essa meta em pouco tempo, através do mix de processos de transporte automáticos e manuais. O sistema de içamento para a movimentação dos componentes tem uma contribuição determinante para o atingimento de nossas metas em relação à flexibilidade e à qualidade."
Galeria de imagens
Galeria de imagens
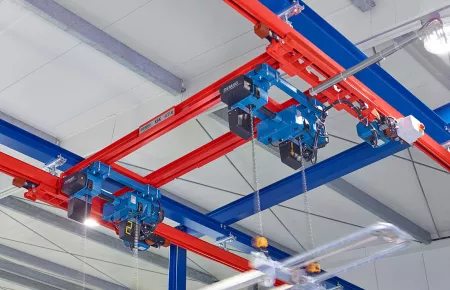
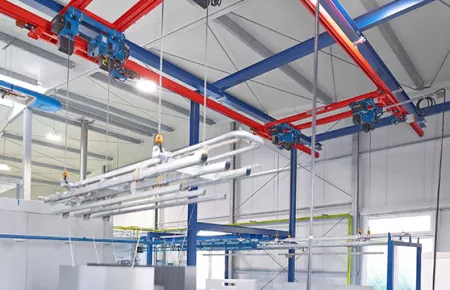
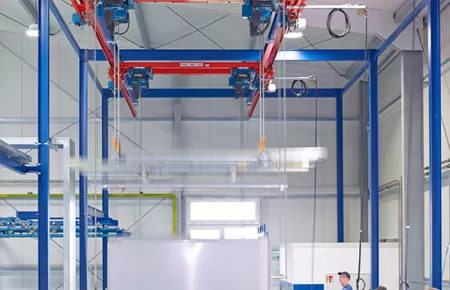
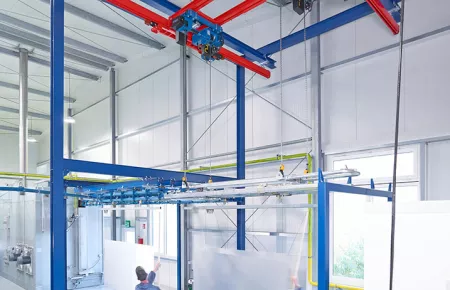