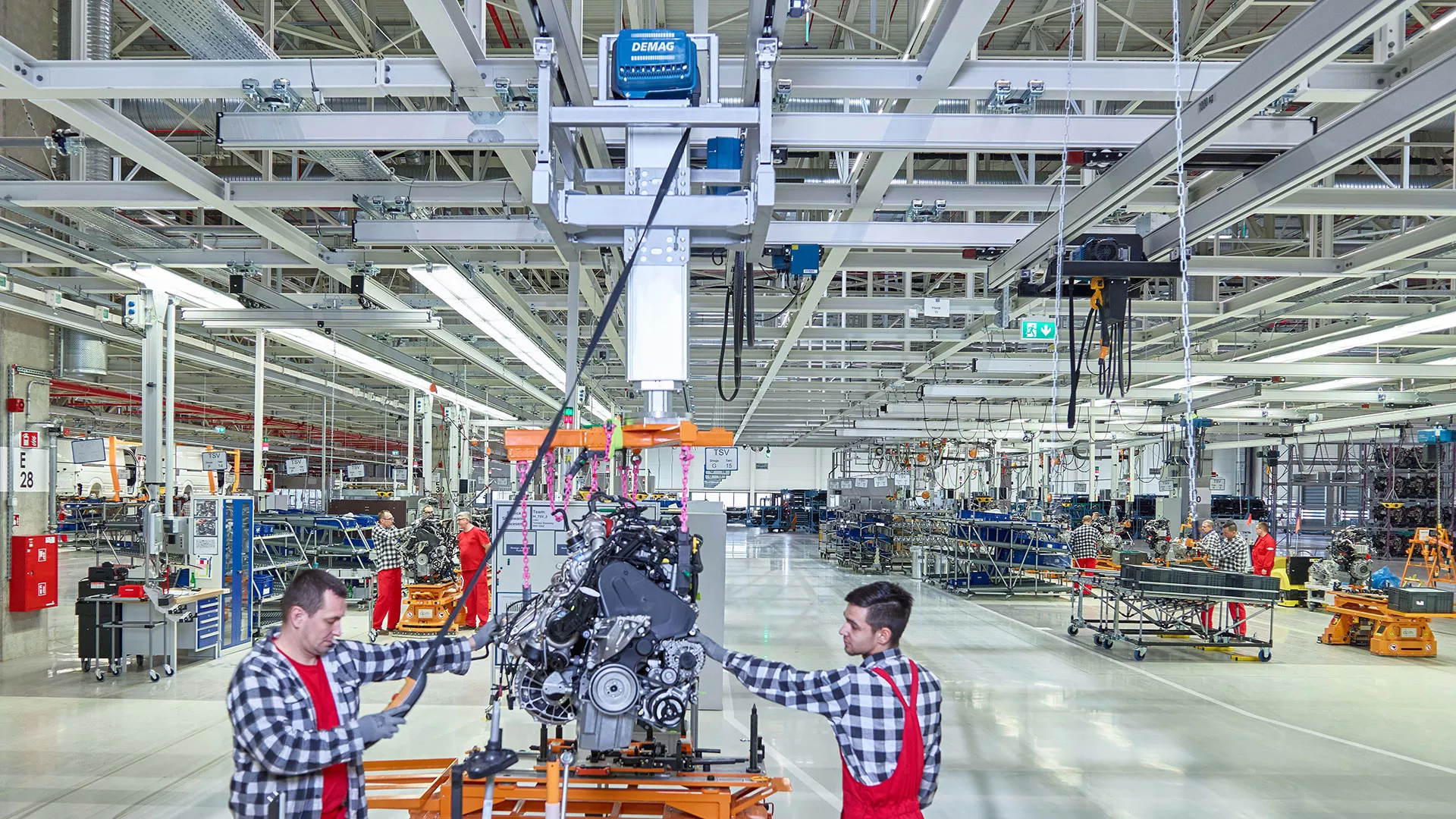
KBK Aluline nello stabilimento VW
Ergonomia nella produzione di veicoli commerciali
KBK Aluline nello stabilimento VW di Września / Polonia
Oltre sei chilometri di rotaie con profili di quattro dimensioni diverse, in cui sono integrati 127 ponti e vari mezzi di sollevamento, manipolatori e unità di avvitamento: questo è, in poche parole, il volume del sistema KBK Aluline progettato e installato da un team di progettisti internazionale Demag presso il nuovo stabilimento VW di Września / Polonia. Si stratta di un sistema estremamente lineare, che migliora l'ergonomia in fase di movimentazione dei pezzi, creando un presupposto importante per una produttività ottimale nell'intero processo di montaggio dei veicoli.
Per un progettista industriale, si tratta della missione ideale: una casa automobilistica leader a livello internazionale costruisce un impianto completamente nuovo e tutti i processi e le attrezzature possono essere progettati da zero - senza restrizioni imposte dalle dimensioni degli edifici o dei pilastri esistenti, ecc.
Volkswagen AG ha dato il via a un progetto di questo tipo alla fine del 2016, a Września, in Polonia, per la produzione dell'ultimo Crafter firmato VW. Proprio qui e nell'indotto integrato, ben 3000 dipendenti producono il veicolo e la componentistica. Questo stabilimento, costruito su una superficie di 220 ettari, è la centoventunesima fabbrica del gruppo Volkswagen. È dimensionato per una capacità annua di 100.000 veicoli commerciali leggeri e dispone di spaziosi capannoni per la costruzione delle scocche, per l'assemblaggio delle vetture, nonché di un moderno reparto di verniciatura.
Componenti più pesanti rispetto a quelli delle automobili
Nel caso dei veicoli come il Crafter, tutto è un po' più grande e pesante rispetto alla produzione delle automobili. Ecco perché la movimentazione dei componenti riveste un ruolo ancora più importante. I veicoli commerciali sono prodotti in quantità decisamente più piccole rispetto ai modelli automobilistici, ma le varianti sono in proporzione molte di più, cosicché molte fasi di produzione non possono essere completamente automatizzate. A causa del peso dei componenti, molte stazioni devono essere servite da manipolatori, gru alle postazioni di lavoro e altre attrezzature di movimentazione. Questa esigenza caratterizza l'intero processo dell'assemblaggio finale, che si suddivide in sette fasi di lavorazione e premontaggio. In molti “supermercati”, vengono inoltre sequenziati, commissionati e messi a disposizione i componenti di molteplici varianti. Complessivamente, il montaggio del Crafter VW si realizza in 155 tappe. I componenti vengono continuamente prelevati dalle piattaforme di carico o preparati per la spedizione, perciò sono necessari dispositivi ausiliari adatti al sollevamento e al trasporto, in modo da ottenere la migliore ergonomia possibile per il personale in ogni singola postazione di lavoro.
In uso in tutta l'area operativa: Demag KBK Aluline
I progettisti di Volkswagen avevano già scelto anticipatamente il KBK Aluline di Demag come sistema universale da impiegare nell'intero processo di montaggio. E i motivi di questa scelta erano e sono buoni. Il sistema modulare ha fornito prestazioni ottimali in tutto il settore automobilistico per oltre cinque decenni a livello planetario.
Il sistema modulare in alluminio del marchio Demag si distingue per le sue buone caratteristiche di scorrevolezza e per la resistenza minima al rotolamento. Queste proprietà unite a un peso proprio ottimizzato offrono vantaggi ergonomici a beneficio diretto dell'operatore durante il lavoro di tutti i giorni. L'estetica dai toni chiari e moderni del sistema di rotaie si adatta inoltre perfettamente a un'organizzazione confortevole delle postazioni di lavoro presso il nuovo stabilimento VW. Oltre agli aspetti ergonomici, i progettisti hanno prestato una particolare attenzione alle tematiche della sicurezza e della praticità in termini di assistenza. Il KBK Aluline di Demag, con la sua pluriennale esperienza internazionale, è in grado di soddisfare appieno queste esigenze. Inoltre il sistema modulare facile da montare permette una certa flessibilità nel caso in cui sia necessario semplicemente ampliare o riorganizzare il sistema, perciò è possibile modificare i processi e il flusso di materiali in qualsiasi momento.
Questa flessibilità era importantissima per Volkswagen, perché era necessario utilizzare un sistema di rotaie adatto a tutte le operazioni, postazioni di lavoro e aree di montaggio, come vuole il principio del “one fits all”. Ciò significa quindi che: sulle rotaie, si installano manipolatori, mezzi di sollevamento e unità di avvitamento completamente eterogenei per quanto concerne l'asse X e in parte anche l'asse y.
Sei chilometri di rotaie, 127 carriponte
Il risultato della progettazione si può peraltro apprezzare “live”, infatti lo stabilimento ha intrapreso la produzione... e ovunque si volga lo sguardo, si vedono le rotaie color argento satinato del sistema KBK Aluline. I tecnici Demag hanno installato oltre 6.000 metri di profilato per i carriponte e le vie di corsa. In tutto, hanno montato 127 ponti per carriponte sospesi mono e bitrave, oltre a tutta una serie di mezzi di sollevamento, manipolatori (con colonne telescopiche, bracci articolati e bilanciatori) e utensili. Anche per i mezzi di sollevamento, Volkswagen si affida ai prodotti Demag e ha deciso a favore della gamma DC di paranchi a catena, che hanno una portata nominale compresa tra 125 e 315 kg e sono utilizzati con 2 velocità o a velocità variabile, a seconda dell'applicazione. La sinergia fra i mezzi di sollevamento Demag e i sistemi di rotaie Demag ha già dato i suoi risultati in altri stabilimenti Volkswagen. Ecco perché questa combinazione è stata implementata anche a Września.
Alcuni esempi basteranno a spiegare le possibilità di utilizzo del sistema KBK Aluline nella produzione del Crafter. La scocca del veicolo si sposta su un sistema di convogliamento a velocità costante attraverso il reparto di produzione. In una delle stazioni si disassemblano le porte della cabina e i portelloni scorrevoli, per poi procedere al preassemblaggio in fase di premontaggio delle porte. Anche la batteria, che pesa ben 30 kg, viene montata qui. Per queste operazioni, l'operatore utilizza un manipolatore monolaterale con uno spazio di movimento da 0 a 4.500 mm. Anche per disassemblare le porte, che sono particolarmente grandi e pesano fino a 85 kg, si utilizzano gli appositi manipolatori, sospesi rispettivamente a due rotaie. In questa stazione, sono stati montati complessivamente 238 metri di rotaie.
Esigenze diverse: un unico sistema
Nel contesto del montaggio del gruppo di trasmissione, le rotaie hanno più che altro il compito di mettere a disposizione dell'operatore gli utensili necessari, come per esempio l'avvitatore pneumatico. Durante il montaggio dei sedili e della base del vano di carico, è necessario maneggiare componenti pesanti o ingombranti, mentre nel montaggio dell'autotelaio si deve sovente provvedere al posizionamento preciso di elementi pesanti, ma compatti, come le balestre e l'ammortizzatore.
In ogni fase di lavoro, il maneggiamento richiede svariate competenze, che KBK Aluline dimostra di avere senza eccezioni. Questo vale anche per i diversi livelli di altezza e per la tipologia della sospensione: se deve provvedere allo spostamento orizzontale degli impianti carropontistici classici con tanto di paranchi a catena, la sospensione utilizzata sarà di tipo oscillante-articolato. Le robuste sospensioni Ergo, che assorbono la coppia e i carichi negativi, entrano in gioco quando si tratta di utilizzare i manipolatori e i sistemi telescopici di avvitamento.
A prescindere dal tipo di utilizzo, le rotaie del sistema KBK Aluline presentano sempre un rapporto ottimale fra portata e peso proprio. I profili in quattro diverse dimensioni creano il presupposto per una scelta adatta all'utente. Le rotelle speciali in plastica permettono un movimento estremamente agevole e silenzioso. In questo modo, le forze necessarie per indurre lo spostamento sono minime e si ottiene una migliore ergonomia, gravando meno sull'operatore. Grazie alla linea di contatto opzionale integrata, si può fare a meno delle linee di alimentazione elettrica esterne o del cavo a festoni. Il colore chiaro, insieme alla tecnologia d'illuminazione precisa e commisurata da Volkswagen, permette inoltre di ottenere la giusta luce in ogni postazione di lavoro.
Chi ben progetta è a metà dell'opera
Va da sé che un gruppo internazionale progetti una fabbrica automobilistica con la massima precisione. In questo caso, si deve tuttavia accennare anche alla flessibilità che ha dato origine a certi vantaggi: spesso, in fase di costruzione, nascono idee per ottimizzare i progetti già esistenti e realizzati insieme, ma anche per migliorare ulteriormente l'ergonomia e la produttività delle singole postazioni di lavoro.
La stretta coordinazione bilingue sul posto, la competenza del team di gestione del progetto Demag e l'esperienza internazionale nella realizzazione di progetti di queste dimensioni hanno dato i loro frutti. Tim Rother, Product Management Demag Handling spiega: “La collaborazione con i progettisti di Volkswagen, le persone coinvolte nella costruzione e gli altri fornitori è andata benissimo. Questa cooperazione è stata sostanziale, anche considerando la straordinaria complessità di questo progetto: non solo per via delle numerose e disparate stazioni di montaggio, ma anche perché è stato necessario rivolgersi a fornitori esterni per i manipolatori e le unità di avvitamento.” In questo contesto, si è rivelata preziosa l'esperienza pluridecennale di Demag nel settore dell'industria automobilistica e dell'attrezzaggio delle linee di montaggio con il sistema KBK.
Esempi di applicazione
Esempi di applicazione
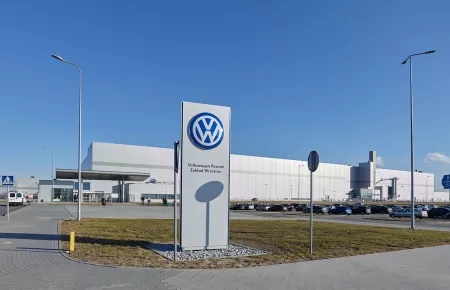
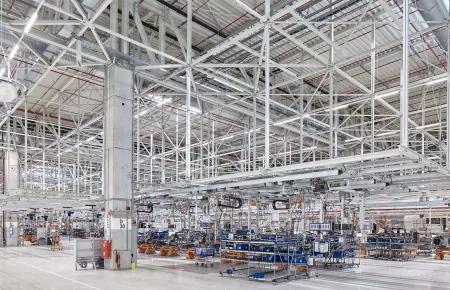
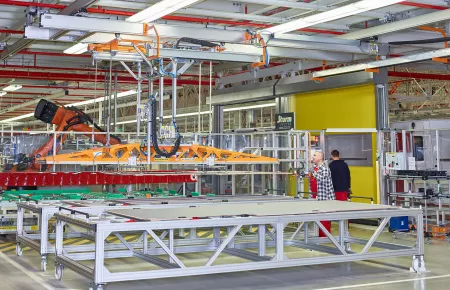
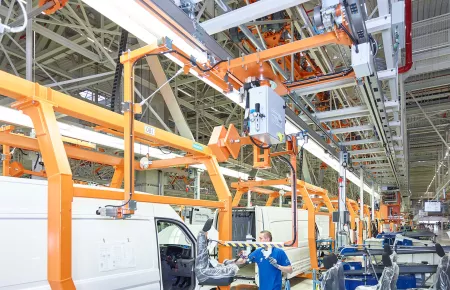