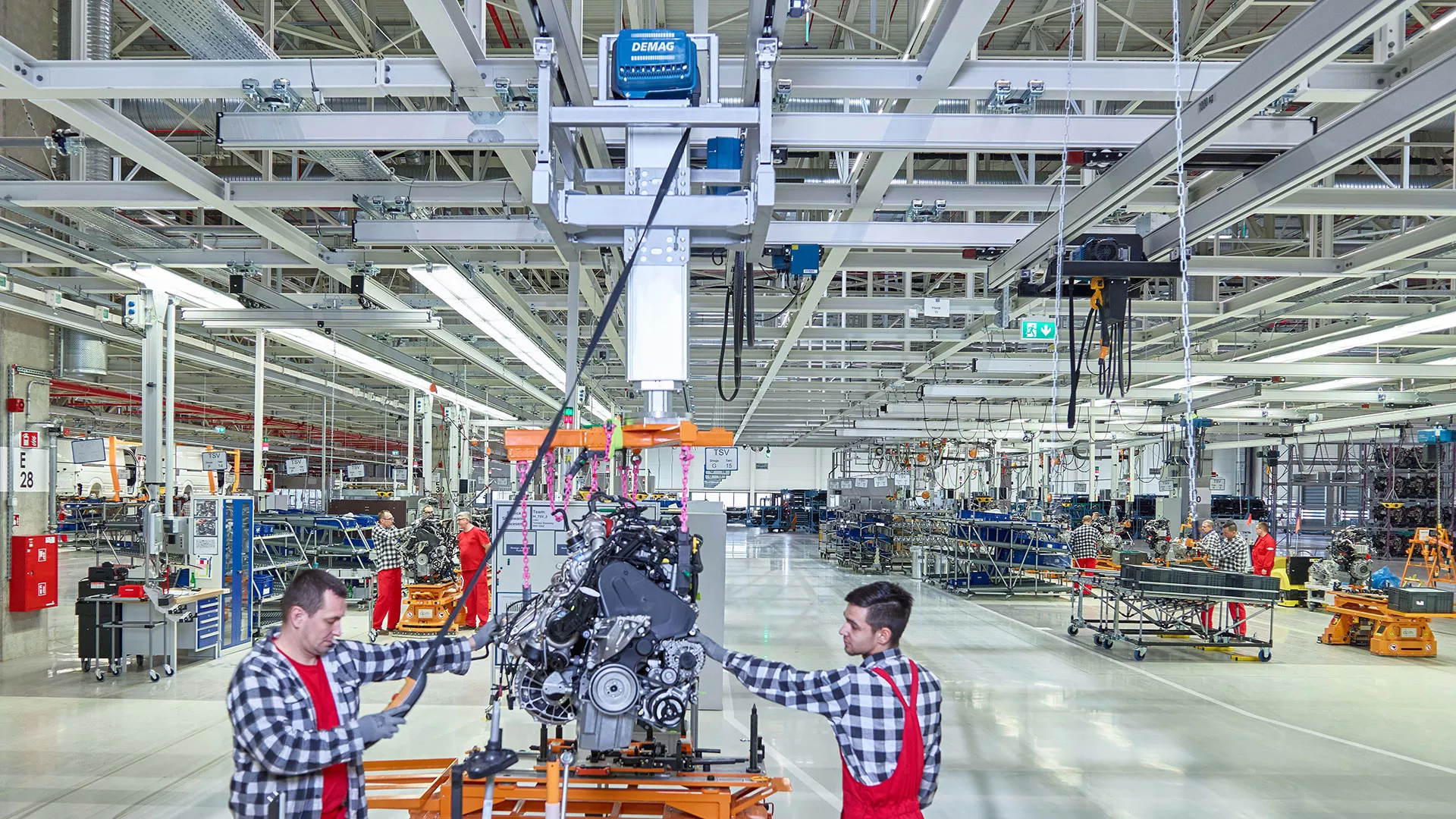
KBK Aluline en la planta de VW
Ergonomía en la producción de vehículos comerciales
KBK Aluline en la planta de VW en Września/Polonia
Más de seis kilómetros de raíles en cuatro tamaños de perfil, con 127 puentes grúa y una gran variedad de polipastos, manipuladores y unidades de atornillado integrados: este es, de forma resumida, el alcance del sistema KBK Aluline planificado e instalado por un equipo de proyecto internacional de Demag en la nueva planta de VW en Września, Polonia. El sistema de funcionamiento extremadamente fluido mejora la ergonomía de la manipulación de las piezas y satisface un importante requisito previo para una excelente productividad en todo el proceso de montaje del vehículo.
Para un diseñador de fábrica es la tarea ideal: un importante fabricante internacional de automóviles está construyendo una planta completamente nueva en un terreno donde todos los procesos e instalaciones se pueden diseñar desde cero, sin ninguna restricción impuesta por edificios ya existentes, dimensiones de pilares, etc.
Volkswagen AG puso en marcha una planta de estas características en Września (Polonia) a finales de 2016 para producir la última generación del VW Crafter. Más de 3.000 trabajadores fabrican allí el vehículo, así como —en el parque de proveedores integrado— muchas de sus piezas. La planta, construida en un terreno de 220 hectáreas, es la 121.ª fábrica del Grupo Volkswagen. Está diseñada para una capacidad anual de 100.000 vehículos comerciales ligeros y cuenta con amplias naves para la construcción de carrocerías y el montaje de vehículos, así como con un moderno taller de pintura.
Componentes más pesados que en la producción de turismos
Con vehículos como el Crafter, todo es un poco más grande y pesado que en la producción de turismos. Por eso, la manipulación de las piezas tiene un papel mucho más importante. Como el volumen de producción de vehículos comerciales suele ser menor que el de modelos de turismos de gran volumen, pero al mismo tiempo hay más variedad, muchos pasos de la producción no pueden automatizarse por completo. Debido al peso de los componentes, se necesitan medios auxiliares como manipuladores, grúas para puestos de trabajo y otros equipos de manipulación en numerosas estaciones. Esto se aplica a todo el proceso de montaje final, que se divide en siete etapas de producción y premontaje. Además, componentes de diferentes variantes se secuencian, se preparan y se ponen a disposición en varios «supermercados». En total, el montaje del VW Crafter se realiza en 155 ciclos. Continuamente, los componentes se retiran de los portacargas, se levantan o se preparan para la entrega, por lo que se requieren medios adecuados para la elevación y el transporte con el fin de lograr la mejor ergonmía posible para el personal en los distintos puestos de trabajo.
Uso generalizado: Demag KBK Aluline
Los responsables de proyecto de Volkswagen se decantaron ya en una fase temprana del proyecto por el KBK Aluline de Demag como sistema universal y utilizarlo en toda la línea de montaje. Por muchas razones. Las «instalaciones modulares» de grúas han demostrado su eficiencia en la industria del automóvil en todo el mundo desde hace más de cinco décadas. El sistema modular de grúas de aluminio Demag se caracteriza por su excelente suavidad de marcha y una baja resistencia a la rodadura. Esto, en combinación con un peso propio optimizado, permite obtener ventajas ergonómicas que benefician directamente a todos los empleados en su trabajo diario. El diseño claro y moderno del sistema de carriles también se adapta perfectamente al agradable concepto de puesto de trabajo de la nueva planta de VW. Además de los aspectos ergonómicos, los responsables de proyecto prestaron gran atención a los temas de seguridad y facilidad de servicio. KBK Aluline de Demag cumple plenamente ambos requisitos gracias a sus muchos años de experiencia internacional. Además, el sistema modular de fácil montaje ofrece la flexibilidad de poder ser ampliado o convertido fácilmente, permitiendo así cambios en los procesos y el flujo de materiales en cualquier momento.
Desde el punto de vista de Volkswagen, esta flexibilidad era un punto especialmente importante ya que, según el principio «Uno para todos», debía utilizarse un único sistema de carriles para todas las tareas, lugares de trabajo y zonas de montaje. En consecuencia: en los carriles se deben instalar un gran número de manipuladores, polipastos y unidades de atornillado que puedan moverse en el eje X y, en algunos casos, también en el eje Y.
Seis kilómetros de carriles, 127 puentes grúa
El resultado de la planificación puede apreciarse ahora «en vivo», ya que la fábrica ha iniciado la producción, y en cualquier lugar donde se mire pueden verse los carriles en plata mate del sistema KBK Aluline. Los técnicos de Demag instalaron más de 6.000 metros de perfiles y vías de rodadura para grúas. Montaron un total de 127 puentes grúa para grúas suspendidas de una y dos vigas, así como diversos polipastos, manipuladores (con columnas de elevación, brazos articulados y equilibradores) y herramientas. Volkswagen también apuesta por los productos Demag para los polipastos y ha optado por los polipastos de cadena de la serie DC, que —dependiendo de la aplicación— tienen capacidades de carga de entre 125 y 315 kg y están disponibles en diseños de 2 etapas o sin escalonamiento. La interacción de los polipastos Demag y los sistemas de carriles Demag ya ha demostrado su eficacia en otras plantas de Volkswagen. Por esta razón, esta combinación también se utiliza en Września.
Algunos ejemplos ilustran las posibles aplicaciones del sistema KBK Aluline en la producción de Crafter. La carrocería del vehículo se desplaza a través de la cadena de producción a una velocidad continua en un sistema de transporte. En una estación, la cabina y las puertas correderas se desmontan para ser premontadas en el premontaje de puertas. La batería de 30 kg también se monta aquí. El operador utiliza un manipulador de un solo lado con un rango de recorrido de 0 a 4.500 mm. Para retirar las puertas grandes, que pesan hasta 85 kg, también se utilizan manipuladores que van suspendidos en dos carriles. En esta estación se instalaron un total de 238 metros de carriles.
Diferentes requisitos - un solo sistema
En la línea de premontaje de accionamientos, los carriles suelen tener la tarea de proporcionar al trabajador las herramientas necesarias, como los atornilladores neumáticos. En el montaje de asientos y compartimento para la carga, hay que manipular componentes pesados o de gran tamaño, mientras que en el montaje del chasis, a menudo hay que colocar con precisión componentes pesados pero compactos, como suspensiones de ballesta y amortiguadores.
Por lo tanto, cada paso de trabajo plantea diferentes exigencias en cuanto a la manipulación; con el sistema KBK Aluline, se pueden cumplir sin excepción. Esto también se aplica a los diferentes niveles de altura y al tipo de suspensión: para proporcionar movilidad horizontal a los sistemas de grúa clásicos con polipastos de cadena, se utiliza una suspensión articulada pendular. Las resistentes suspensiones ergo que pueden soportar fuerzas de torsión y de arranque se utilizan para aplicaciones con equipos de manipulación y atornilladores telescópicos.
Independientemente del tipo de aplicación, los carriles del sistema KBK Aluline se caracterizan siempre por una relación óptima entre la capacidad de carga y el peso propio. Cuatro tamaños del perfil crean el requisito previo para una selección eficaz. Rodillos de plástico especiales garantizan un funcionamiento extremadamente ligero y silencioso. Esto conduce a una menor fuerza motriz y con ello, más ergonomía y menos esfuerzo para el trabajador. La línea de contacto integrada opcional permite prescindir de fuentes de alimentación externas o de los molestos cables de arrastre. El brillante diseño del sistema, en combinación con los sistemas de iluminación configurados por Volkswagen para cumplir con las especificaciones más exigentes, permite que cada puesto de trabajo esté idealmente iluminado.
Una buena planificación es la mitad del trabajo
No hace falta decir que una corporación internacional planifica una fábrica de coches con la máxima precisión. En este caso, sin embargo, también es importante mencionar la flexibilidad que ha permitido obtener ciertas ventajas: Durante la construcción, a menudo surgieron ideas para optimizar los planos existentes, que se aplicaron conjuntamente y mejoraron aún más la ergonomía y la productividad en los distintos puestos de trabajo.
En este caso, la estrecha coordinación bilingüe en la obra dio sus frutos, al igual que la experiencia del equipo de gestión de proyectos de Demag, que contaba con experiencia internacional en la ejecución y coordinación de proyectos de esta envergadura. Tim Rother, Gestión de productos Demag Handling: «La cooperación con los responsables de proyecto de Volkswagen, las personas involucradas en la construcción y otros proveedores se desarrolló sin problemas. Esta cooperación fue especialmente valiosa también en lo que respecta a la extraordinaria complejidad de este proyecto: no sólo por las numerosas estaciones de montaje, sino también por la inclusión de proveedores externos para los manipuladores y las unidades de atornillado». La experiencia de décadas que Demag ha adquirido en la industria del automóvil y en el equipamiento de líneas de montaje con el sistema KBK demostró su eficacia.
Galería de imágenes
Galería de imágenes
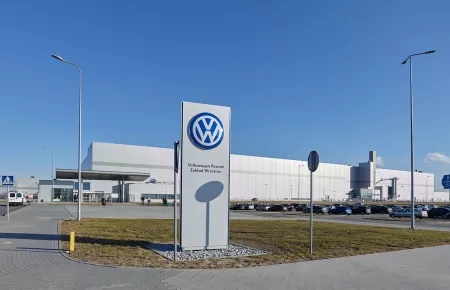
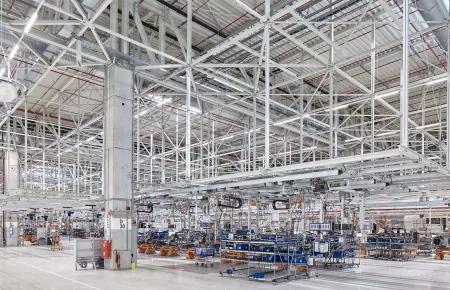
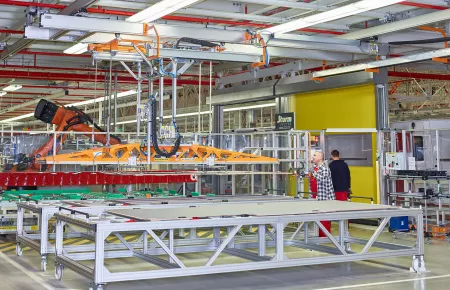
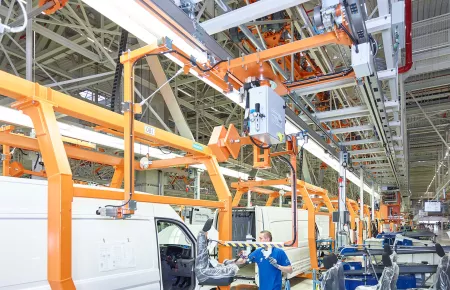