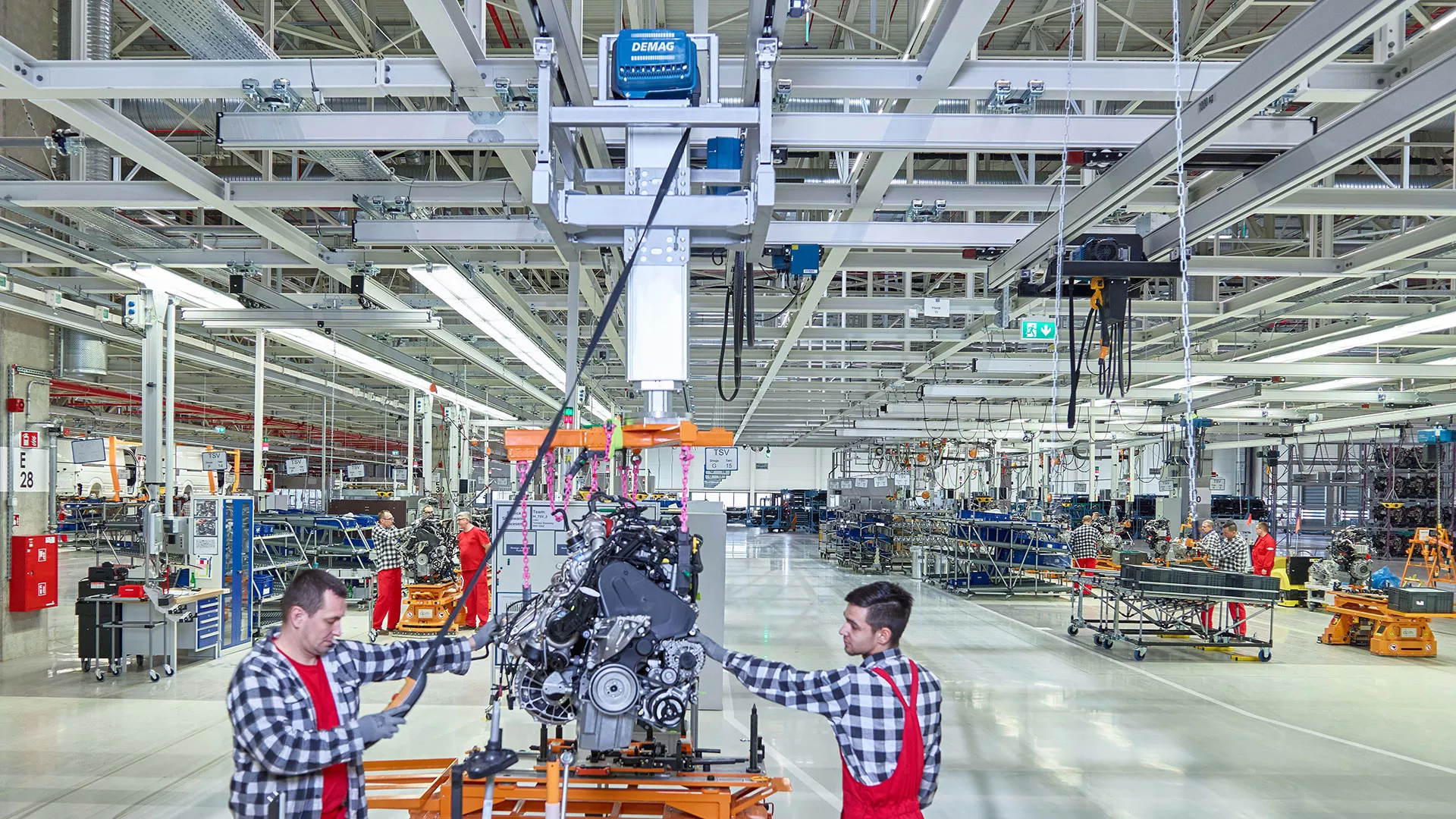
KBK Aluline na fábrica da VW
Ergonomia na produção de veículos utilitários
KBK Aluline na fábrica da VW em Września, na Polônia
Ergonomia na produção de veículos utilitários
Mais de seis quilômetros de trilhos em quatro tamanhos de perfil, com integra-ção de 127 pontes rolantes e das mais diversas talhas, manipuladores e unida-des parafusadeiras: Bem resumidamente, esse é o escopo do sistema KBK Alu-line projetado e instalado por uma equipe internacional da Demag na nova fá-brica da VW em Września, na Polônia. O sistema é extremamente leve e melhora a ergonomia no manuseio de peças, criando condições favoráveis para uma ótima produtividade em toda a linha de montagem do veículo.
Este é um trabalho ideal para um planejador de uma fábrica: uma grande indústria automotiva internacional constrói uma fábrica totalmente nova em um terreno limpo com um belo gramado. Nela, todos os processos e instala-ções podem ser concebidos do zero, sem quaisquer restrições impostas por edificações ou fundações preexistentes.
Uma fábrica assim foi aberta pela Volkswagen AG no fim de 2016 na cidade polonesa de Września, para a produção da última geração do seu utilitário Crafter. Ali, mais de 3 mil profissionais fabricam o veículo, além de inúmeras peças de terceiros no parque industrial integrado de fornecedores. A fábrica, construída em um terreno de 220 hectares, é a 121ª planta produtiva do grupo Volkswagen. A capacidade anual instalada é de 100 mil veículos utilitá-rios leves. A fábrica dispõe de amplas oficinas para a montagem do chassi e do veículo, bem como uma linha de pintura de última geração.
Peças mais pesadas do que na produção de carros de passeio
Quando se trata de veículos utilitários como o Crafter, tudo é maior e mais pesado do que na produção de carros de passeio. Por isso, a manipulação de peças desempenha um papel muito maior. Uma vez que no caso de veí-culos utilitários as quantidades produzidas são menores, mas proporcional-mente mais variadas se comparadas com a produção de carros de passeio, muitas das etapas produtivas não podem ser totalmente automatizadas. De-vido ao peso das peças, em muitas estações de trabalho se faz necessário o uso de manipuladores, pontes rolantes e outros equipamentos de manuseio. Isso se aplica a todo o processo de montagem final, que é subdividido em sete estações, de produção e pré-montagem. Peças para uma série de vari-antes também são sequenciadas, coletadas e disponibilizadas em vários "supermercados”. A montagem do Crafter, da VW, é realizada em um total de 155 ciclos. As peças são continuamente coletadas das transportadoras de carga, levantadas ou instaladas em pedidos, o que requer equipamentos cor-respondentes de elevação e transporte para fornecer a melhor ergonomia possível para os operadores em seus locais de trabalho individuais.
Utilização abrangente: Demag KBK Aluline
Já nas primeiras etapas os responsáveis da Volkswagen optaram pelo KBK Aluline da Demag como sistema universal a ser usado em toda a montagem. Eles tinham bons motivos para esta decisão. O sistema modular de pontes rolantes tem proporcionado o melhor desempenho em toda a indústria auto-motiva por mais de cinco décadas em todo o mundo. O sistema modular de ponte rolante em alumínio da marca Demag tem co-mo diferenciais as características de leveza, de movimento e mínima resis-tência à rolagem. Combinadas à otimização do peso próprio, tais proprieda-des trazem vantagens ergonômicas que beneficiam diretamente todos os operadores em sua rotina diária.
A aparência clara e moderna do sistema de trilhos também combina com o design amigável do local de trabalho da nova fábrica da VW.
Além dos aspectos ergonômicos, os responsáveis priorizaram a segurança e a facilidade de manutenção. O KBK Aluline atende plenamente a ambas as exigências, graças aos muitos anos de experiência internacional da Demag. Além disso, o sistema modular facilmente montado e versátil pode ser ampli-ado ou modificado de modo simples, possibilitando alterações no processo e no fluxo de materiais a qualquer momento.
Para a Volkswagen, essa flexibilidade particularmente foi muito importante, pois de acordo com o princípio "One fits all" um único sistema de trilhos de-veria ser usado em todas as tarefas, estações de trabalho e áreas da mon-tagem. Isto também significa que: nos trilhos são instalados manipuladores, talhas e unidades parafusadeiras muito distintos, com translação no eixo X mas também, em partes, no eixo Y.
Seis quilômetros de trilhos, 127 pontes rolantes
Já é possível conhecer pessoalmente o resultado desse trabalho, pois a fá-brica deu início à produção. Para onde você olhar, poderá ver os trilhos pra-teados foscos do sistema KBK Aluline. Os técnicos da Demag instalaram mais de 6 mil metros de trilhos perfilados para as pontes rolantes e caminhos de rolamento. No total, foram instaladas 127 pontes rolantes suspensas mo-noviga e biviga, e uma grande variedade de talhas, manipuladores (com co-lunas de elevação, braços articulados e balancins) e ferramentas. Em rela-ção às talhas, a Volkswagen também demonstrou confiança nos produtos da Demag, optando por talhas de corrente da linha DC com capacidades de carga entre 125 e 315 kg, usadas em 2 velocidades ou com controle variável de velocidade, dependendo da aplicação. A interação das talhas Demag com os sistemas de trilhos Demag já provou ser uma boa solução em outras fá-bricas da Volkswagen, por isso, essa combinação foi implementada também em Września.
Alguns exemplos mostram as possibilidades de aplicação de sistemas KBK Aluline na produção do Crafter. As carrocerias dos veículos são levadas por um sistema de transporte em velocidade contínua através da produção. Em uma estação, as portas deslizantes e a cabine são retiradas para serem pré-montadas na pré-montagem de portas. As baterias de 30 kg também são instaladas aqui. Para fazer isso, o operador usa um manipulador unilateral com uma área de translação de 0 a 4.500 mm. Manipuladores que estão suspensos em dois trilhos também são usados para remover as portas gran-des, que pesam até 85 kg. Foram instalados um total de 238 metros de tri-lhos nessa estação.
Necessidades variadas - um sistema único
Na pré-montagem do conjunto de acionamento os trilhos servem para dispo-nibilizar as ferramentas necessárias ao operador, por exemplo a parafusadei-ra pneumática. Componentes pesados ou grandes precisam ser manusea-dos na montagem do banco e na linha de montagem do painel de base do compartimento de carga; embora as peças sejam muitas vezes pesadas, porém compactas, como feixes de molas e amortecedores, devem ser posi-cionadas com precisão na linha de montagem do veículo.
Cada etapa do processo traz exigências diferentes em termos de manipula-ção – todas podem ser atendidas, sem exceção, com o sistema KBK Aluline. Isto também se aplica a diferentes níveis de altura e tipos de suspensão: quando se requer mobilidade horizontal de instalações convencionais de pon-tes rolantes com talhas de corrente, são utilizadas suspensões que tenham dobradiças articuladas. Suspensões ergorobustas que suportam torque e cargas negativas são usadas para aplicações com equipamentos de manu-seio e parafusadeiras telescópicas.
Qualquer que seja a aplicação, os trilhos do sistema KBK Aluline sempre se destacam pela otimização de capacidade de carga para o seu peso próprio. Quatro tamanhos de perfil, permitem a escolha da solução certa para a apli-cação específica. Os rodízios especiais, de material sintético, oferecem uma translação extremamente leve e silenciosa. Isto também garante que pouca força seja aplicada para movimentação – para uma ergonomia ideal e menor esforço físico para o operador. O barramento elétrico integrado opcional dis-pensa o uso de alimentação elétrica externa ou de cabos de arraste indese-jados. O design claro do sistema, associado à tecnologia de iluminação pre-cisa, projetada pela Volkswagen, possibilita a visibilidade ideal em cada local de trabalho.
Um bom planejamento optimiza o resultado
É evidente que uma corporação internacional planeja uma nova fábrica de automóveis com máxima precisão. Nesse caso é preciso mencionar a flexibi-lidade que resultou em vantagens significativas: muitas vezes, durante a fase de construção, surgiam ideias de otimização para o planejamento existente que eram implementadas, permitindo assim melhorar ainda mais a ergono-mia e a produtividade dos locais individuais de trabalho.
A estreita colaboração com comunicação bilíngue no canteiro de obras foi muito vantajosa, além claro da expertise da equipe de gerenciamento de pro-jetos da Demag com sua experiência internacional na realização de projetos desse porte. Tim Rother, Gerente de Produtos da Demag Handling, explica: "A colaboração com os responsáveis da Volkswagen, com as pessoas envol-vidas na construção e com outros fornecedores transcorreu em harmonia. Essa cooperação foi especialmente valiosa também considerando a comple-xidade extraordinária desse projeto, não apenas devido às muitas e variadas estações de trabalho como também devido à inclusão de fornecedores ex-ternos para os manipuladores e parafusadeiras." A experiência de décadas da Demag na indústria automotiva e na configuração de linhas de montagem com o sistema KBK novamente foi comprovada.
Galeria de imagens
Galeria de imagens
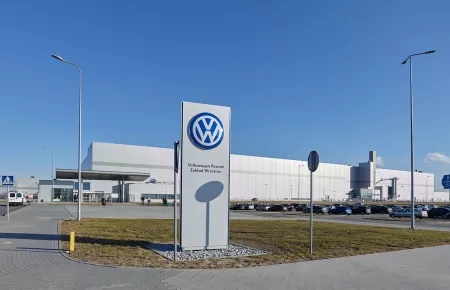
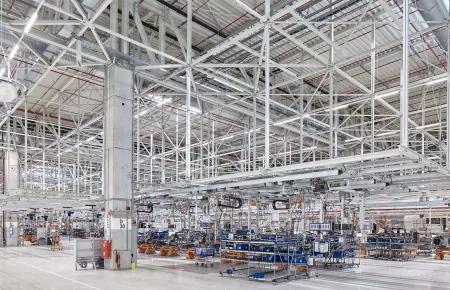
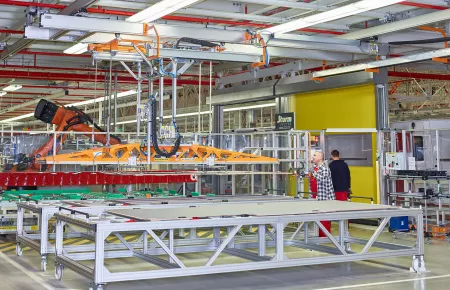
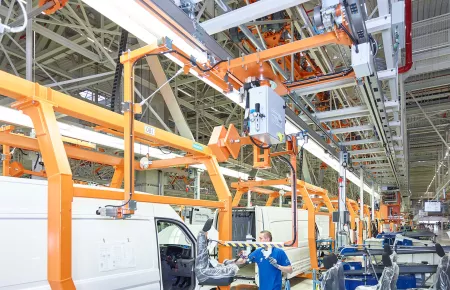