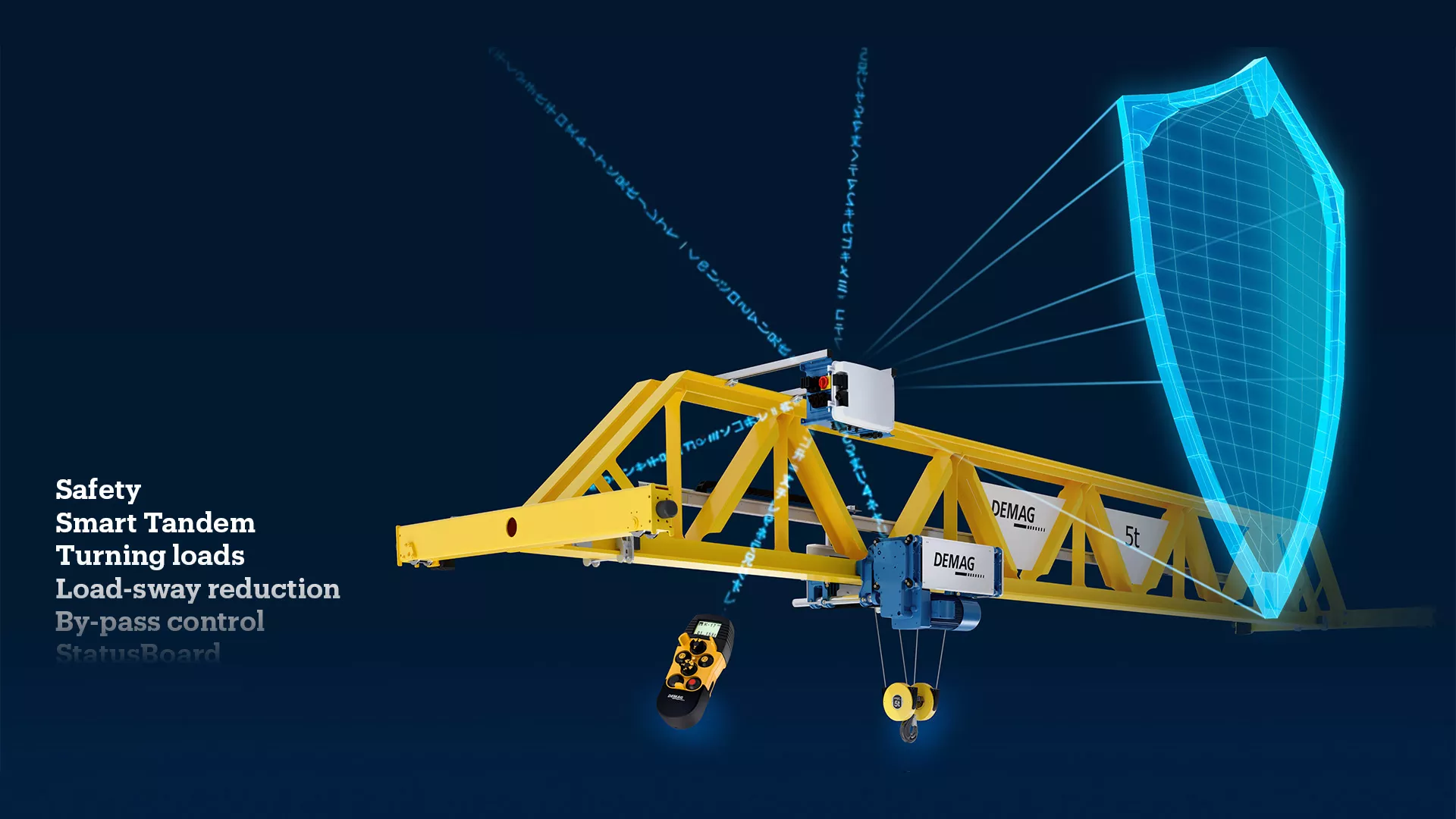
Safe, by Demag
Demag SafeControl
Safety during crane operation
The combination of crane control and wireless control concept creates the link between an operator and a crane and thus makes optimum load handling a tangible experience. Absolutely safe operation of a crane or a system of several cranes must always be guaranteed – safety for the crane operator as well as for the transported goods and surrounding infrastructure.
The smart Demag SafeControl system enables independent and continuous monitoring of a crane on the basis of a largely redundant control concept to bring the system to a standstill independently if any irregularities occur. Furthermore, dangerous conditions can be identified and prevented in advance. The crane operator can concentrate fully on his/her work at all times thanks to the safety control system. A crane can be conveniently and intuitively controlled by radio, which is also very efficient. The safety control system combined with radio control can ensure gentle handling and precise positioning of loads. This meets our high demands for safe and reliable crane control.
.
The SafeControl system can reveal its full potential wherever a crane needs to meet complex operating and control requirements. The safety control system provides the technical basis for implementing tandem crane control, smart-tandem crane control, the turning of loads and load-sway reduction as well as for other complex requirements, such as a crane by-pass control. Demag SafeControl enables safety-related control functions up to Performance Level d in accordance with EN ISO 13849 or SIL 2 in accordance with EN 61508.
Benefits of Demag SafeControl
- Crane operation additionally protected by continuous, independent monitoring of basic crane functions
- High productivity thanks to optimized load handling
- User-friendly control for complex applications
- Technical basis for a safety-related control system for almost all load handling needs
- Safety-related control functions up to Performance Level d according to EN ISO 13849, or SIL 2 according to EN 61508
- Two-channel hardware enables independent safety cut-off and corresponds to Category 3 (CAT 3) according to EN 13849-1
- TÜV certified
Safe, good to know
Technical background
SafeControl provides the basis for a large variety of safety-related applications and is suitable for a wide range of crane and lifting equipment applications. This applies to requirements for the pure lifting and lowering of loads, in addition to complex and safety-sensitive tasks, such as tandem control or turning of loads.
SafeControl is a modular control system consisting of decentrally arranged control modules as well as various additional hardware modules (I/O extension module, radio receiver, large load display and others). Communication between these control modules is wireless or wired via a CAN bus.
The firmware covers a wide range of control functions, including various assistance features. The control functions can be activated via a parameter-programming interface. The modular SafeControl control system enables safety-related control functions up to Performance Level d according to EN ISO 13849 or SIL 2 according to EN 61508. The control system hardware operates completely on two channels so that control functions can be executed in category 3. This is certified by TÜV.
Performance level – safety can be defined
The performance level is defined in the EN 13849 standard as a “discrete level used to specify the ability of safety-related parts of control systems to perform a safety function under foreseeable conditions.”
The performance level can thus provide a basis for assessing the reliability of a safety function. The performance level is divided into five levels, from level a (low performance level) to level e (highest performance level).
The higher the performance level, the safer and more reliable the given function. Before a component is used, it must be checked to ensure it can be used for the intended application and the assessed risk. The rule is that the performance level of the component must always be at least as high as the risk value at the relevant point.
A risk assessment is carried out according to the EN 13849 standard and assesses the possible extent of damage, the frequency and duration of stay and the possibility of avoiding the hazard.
Perfect interaction between all components
Tandem operation enables lifting and transport operations which cannot be performed with individual cranes or hoists: lifting long and bulky loads and lifting loads whose weight exceeds the maximum load capacity of the individual crane. Perfect interaction between the long and cross-travel motions, safety control system and radio control make it easier for the crane operator to concentrate fully on handling the load.
Smart tandem control of two cranes or hoists is one of the most complex operating methods for crane systems. Perfect interaction between all components is of crucial importance. Moving two cranes and up to four trolleys simultaneously requires a safe and powerful control concept.
The Demag control concept for cranes with smart tandem enables smooth and precise load handling – particularly for complex crane applications. By setting different hook heights on both trolleys, a bulky load can be turned simultaneously, safely, quickly and conveniently and can be transported to the desired position.
Demag DRC radio control systems make it easier for the operator to handle loads thanks to intuitive and ergonomic features. The control elements are arranged in such a way that the crane operator can always keep an eye on the load handling process. Assistance systems can be switched on and off with ease using selector switches or control elements. The SafeControl assistance systems are also easier to monitor via the LC display integrated in the control unit.
The Demag control concept enables the crane operator to select between single and smart tandem operating modes quickly and easily. Switching between these operating modes is done in such a way that potentially hazardous conditions for individuals and the surrounding infrastructure can be identified and avoided.
Benefits of (smart) tandem operation
- Safe and reliable handling of heavy and bulky loads
- Safe and reliable switch-over between operating modes
- Efficient load handling
- Precise position control thanks to Demag tandem control concept
- User-friendly radio controls
Operating modes
Tandem mode
Control of two cranes with a common control system
Tandem mode allows two cranes to be used independently of each other as individual units. It is also possible to use individual hoists, which gives the crane operator the flexibility that is needed at all times during daily work. Changing between operating modes is quick and easy with the selector switch on the radio control.
To change from single operating mode to tandem mode, one of the two crane control systems must be logged off and is then inactive. The remaining control system can control both cranes with all trolleys. In tandem mode, both cranes can be controlled together or independently with one radio control system. In single operating mode only one crane can be controlled (crane selector switch: A or B), in tandem mode both cranes can be controlled in parallel (crane selector switch: A+B)
Single mode
Each crane or hoist can be controlled by its own control system
In single operating mode, each crane or hoist can be controlled by its own radio control system as long as there are no safety-relevant special functions which can result in mutual interference by the cranes.
Smart-tandem mode
Two cranes with up to four trolleys
In smart tandem mode, two cranes with up to four trolleys can be used to transport particularly bulky and heavy loads.
Safely exceeding limits
The process of turning loads requires perfect interaction between the long and cross-travel motions as well as the lifting motion. This safety-sensitive operation enables the crane operator to turn a load weighing up to 50 tonnes by up to 180°. When a load is turned on the crane, all components must interact smoothly and the process must be constantly monitored.
When a load is turned, the maximum load on each rope hoist, the collective load on both rope hoists and the relevant rope angles must be taken into account. During the turning process, therefore, both the inclined pull and the lifting or lowering motion of one or both hoists need to be corrected.
The smart SafeControl system allows for the shift in load between the two hoists as well as the inclined angle of pull for correction purposes. With the Demag DMR modular rope hoist, it is possible to achieve a rope angle of up to 15° – or more in some cases. In addition, uncontrolled slipping of one of the two trolleys must be avoided. For safe control and monitoring of the load turning process, SafeControl uses its ability to monitor several motions simultaneously as a coordinated movement. For example, rope angle sensors are included in the monitoring of the turning process. Inclined pull of the hoists can thus be avoided with the load turning function.
Demag SafeControl independently safeguards the load-turning process at all times. The control system provides safety-oriented monitoring of all motion sequences and stops operation or gives a warning if any irregularities occur, thus avoiding dangerous operating situations. If the defined maximum rope angle stored in the control system is reached or exceeded, only those functions that lead to a reduction of the rope angle are possible. Errors by the crane operator when turning the load can be avoided with SafeControl.
Benefits when turning loads
- Loads weighing up to 50 t can be turned
- Loads can be turned by up to 180°
- Safe and reliable monitoring of the turning process by rope angle sensors
- Safe and reliable cut-off of lifting and travel motions if the maximum permissible rope angles are exceeded
- Requirements for safe control systems according to standard EN ISO 13849-1 are fulfilled
- Crane operating errors can be avoided
- Increased productivity when turning loads
Continuous monitoring. At all times.
Variant 1: Warning signal when the permissible rope angle is exceeded
An acoustic and/or visual warning is given as soon as the maximum deflection angle is reached. In this case, the crane operator himself is responsible for ensuring that no personal injuries or damage to the transported goods or the crane installation are caused during the turning operation.
Variant 2: Monitoring by safety control system
The safe load turning function can be achieved by combining the Demag smart SafeControl system with a two-channel, non-contact sensor system for precise measurement of the rope angles. The control system monitors all motion sequences and automatically stops the lifting and travel motions if any irregularities occur. If the previously defined maximum inclined angle of pull saved in the control system is reached or exceeded, only those functions that lead to a reduction of this angle are possible.
By monitoring with Demag SafeControl, a high safety category of Performance Level d (for lifting and lowering the load) or Performance Level c (during travel) in accordance with EN 13849-1 (category 3) can be achieved. Category 3 means that if a single error occurs when a signal is transmitted or evaluated, it is reliably identified by the control system and can never lead to a critical or unsafe situation.
In this way, the crane operator is ideally protected and can concentrate fully on the task. Safety and productivity can be increased when turning loads using the Demag smart SafeControl system.
Assistance system independently reduces sway
Demag load-sway reduction supports crane operators when handling loads. Loads can start to sway at any time when the crane or trolley is moving. The swaying motion can cause danger to life and limb and a risk of damage to the machinery. In addition, cycle times can take longer until the load has stopped swaying. On the basis of the Demag smart SafeControl system, load sway motions can be detected by measurement of the rope angle and compensated by dedicated correction of the travel motions. This also enables sensitive loads to be positioned more quickly and, above all, more safely and reliably.
The integrated sensor system precisely measures deflection of the load and can prevent an already lifted load from swaying by identifying the movement in good time. Above all, unexpected malfunctions or irregularities can be avoided and load handling made safer by combining SafeControl and rope angle measurement. Load-sway reduction supports inexperienced crane operators in particular, thus reducing the risk of collisions and increasing crane operating safety.
|
|
Benefits of load-sway reduction
- Support for load handling through independent corrective action by the crane
- Faster and more precise positioning of the load
- Collisions with other machines and equipment can be avoided
- Improved safety – especially for less experienced crane operators
- Assistance function, the advantages of which are immediately felt by every operator without the need for additional explanation
Range-specific adjustments of long and cross travel
The use of a crane cannot always be planned from the outset and the use case can change after it is installed. Over time, requirements on production lines change and with them the functional range of a crane. The smart SafeControl system makes it possible to bypass sections where the crane or trolley should not travel. What is known as bypass control can block this area for the crane or trolley, avoid the risk of collisions and protect against damage.
Load reduction on the crane can be necessary for certain parts of the building. If the building structure is already subjected to strong loads, these areas can be electronically protected to block operation with full loads; if required, travel in these areas can be permitted with a defined reduced load.
If there are several cranes on one crane runway or several trolleys on one crane, a crane or trolley anti-collision system can protect against collisions and damage. Sensors constantly measure position and distance. The acquired data is monitored by the SafeControl system at all times and if there is any deviation from the pre-set parameters, the safety control system can immediately and autonomously ensure that the installation is in a safe condition.
Benefits of a crane/trolley anti-collision system
- Protection against collision and damage
- Continuous monitoring of the installation(s) by sensors
- Safety cut-off of the installation by Demag SafeControl
Benefits of load reduction
- Optimum adaptation of your crane to the requirements of the working environment
- Protected areas can be defined at a later date without the need for any conversion work
- The building structure can be protected by means of defined maximum loads
- Continuous monitoring of the installation(s) by sensors
- Safety cut-off of the installation by Demag SafeControl
Benefits of bypass control
- Optimum adaptation of your crane to the requirements of the working environment
- Blocked zones can also be defined at a later date – without the need for any further conversion work
- Protection against collision and damage
- Safety cut-off of the installation by Demag SafeControl
Information on your crane at a glance
Demag SafeControl provides safety during crane operation. Sensors and smart interfaces enable data to be collected that reflect the condition of the crane. With the aid of Demag radio control systems, Demag SafeControl and Demag StatusBoard, these data can be displayed to the crane operator and owner.
StatusBoard can visualise how much load is actually transported on the hook of the crane. Current status reports, activated assistance and efficiency improvement functions as well as service data can be read quickly and easily from the StatusBoard by the crane operator and anyone else who can see the board.
Benefits of StatusBoard
- Display of the load weight on individual cranes or total loads
- Display of operating statuses, for example:
- Selected crane and/or trolley
- Activated assistance and efficiency improvement functions
- Error messages
- Information messages
- Service data