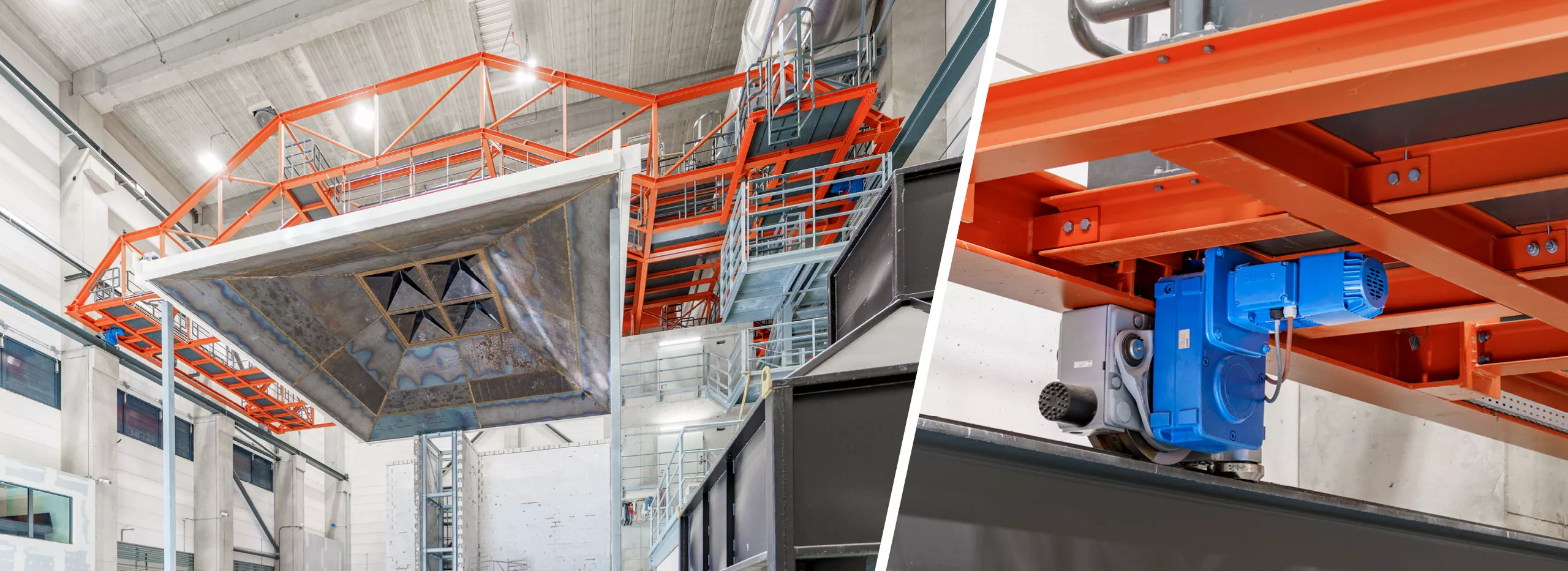
Stahlbau Wentz builds mobile extraction hood for fire tests
A special task for the Demag modular drive system
Flue gases “under the hood”
Company
Where other steel construction companies reach their limits, the specialists at Stahl-Projektbau Wentz GmbH come to the fore. Founded in Goslar in 2005, the company designs and builds pipeline bridges, support substructures and crane runway installations, among other things. The company's portfolio includes complete industrial buildings as well as test benches and process plants.
Wentz specialises in special steel constructions, including for research facilities. One example is individually designed radiation protection booths as enclosures for material testing systems and electron accelerators, among other things. Another very “exotic” example is the extraction system described here for an institute that carries out fire tests on building materials and components.
Requirement
How do building materials behave in the event of fire? And how can the fire risk of new and innovative building materials, e.g. from renewable raw materials, firstly be assessed and secondly minimised? A research facility in Braunschweig is investigating these questions and has set up a new experimental workshop for large-scale fire tests for this purpose.
The task of Stahlbau Wentz was to construct a movable 12 x 12 metre extractor hood in this workshop, which extracts all smoke gases generated by several open test benches and supplies them to a flue gas cleaning system. This places high demands on the materials handling components of the extractor hood, which must ensure reliable positioning of the extractor hood weighing several tonnes within a broad temperature range.
Solution
A crane runway was installed in the workshop on which a bridge made of a sectional steel structure travels. This positions the extractor hood above the relevant fire test. A raised bridge design was selected here to save on the overall height.
The entire unit consisting of bridge and steel extractor hood weighs 70 tonnes. It is precisely positioned on the craneway with a total of four Demag wheel blocks from the DRS 315 range. The wheel blocks are all equipped with flanges on both sides for reliable travel even in a broad temperature range of -20 to +70 degrees during the experiments. Two Demag ADE60TD ZBA80 offset geared brake motors transfer their power of 0.62 KW to the four wheel blocks. The offset gearbox design saves installation space. The drive concept is rounded off by a Demag Dedrive Compact frequency inverter, which moves the huge "extractor hood" continuously along the crane runway.
Special features
Demag DRS travel wheels with flanges on both sides ensure precise travel on one of the two crane runways. Both drives are controlled via a common Dedrive Compact frequency inverter. Synchronised control is thus guaranteed with minimal effort. Signals are evaluated by a Demag SCU safety control unit, which can achieve Performance Level 3 (EN ISO 13849) and SIL Level 2 (IEC 61508). As the travel unit is relatively high up, it is conveniently controlled by personnel from the working level via a Demag DRC-MJ radio control system. The Demag drive solution can be used up to an ambient temperature of 70 oC, which means that there is no risk of failure caused by overheating during the fire tests.
Three questions for Marcel Lissa, Sales Engineer responsible for the project with Wentz Stahlbau and the research facility at Braunschweig Technical University.
Demag: Mr Lissa, what were the initial requirements you received from the project partner?
Marcel Lissa: Wentz Stahlbau Managing Director, Felix Wentz, approached me with a project in which a 12-metre wide lattice framework structure with a correspondingly large extraction hood was to be moved. It was important for the Braunschweig Technical University site that the components could withstand the high temperatures, move the around 70-tonne extraction hood at a responsive travel speed, and also be controlled by radio control.The entire unit now travels around the building on 30-metre rails, with both the right and left positions being approached equally at 1–5 m/min. The Braunschweig Technical University research facility has defined these zones in the building design for its experiments, so that the extraction hood collects the flue gases at a total of three stopping points and directs them out of the building.
Demag: What product features are particularly noteworthy in the drive solution for the industrial platforms?
Marcel Lissa: The overall drive concept is particularly noteworthy. Our Demag modular drive system offers the option of creating a complete drive system consisting of a geared motor and wheel block as well as an application module consisting of a frequency inverter and Demag SCU safety control unit. Mechanical and electric components such as track buffers and a radio control system complete the set-up. The trolley components have all been designed for a temperature range of up to 70° C and move the hood precisely into position at the desired very low travel speed.Demag: Did this project involve any unusual requirements?
Marcel Lissa: The most unusual thing about this project was the environment! The combination of a 70-tonne steel hood and a high temperature range for experiments is another fantastic challenge for our components to prove their reliability. Operator safety was, of course, taken into account. The extraction hood is controlled from a console at a safe distance from the experiment. After carrying out the respective experiment, the operator can conveniently change the control system at the push of a button and use the radio control to move the extractor hood directly on the lattice framework or through the building.
Your Contact
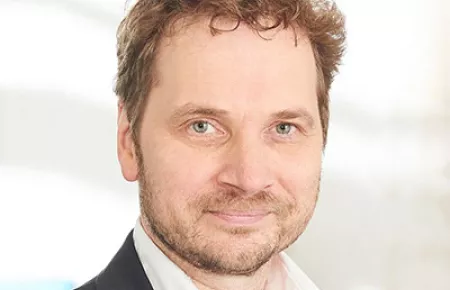
Christoph Kreutzenbeck
Ruhrstrasse 28
58300 Wetter
Germany