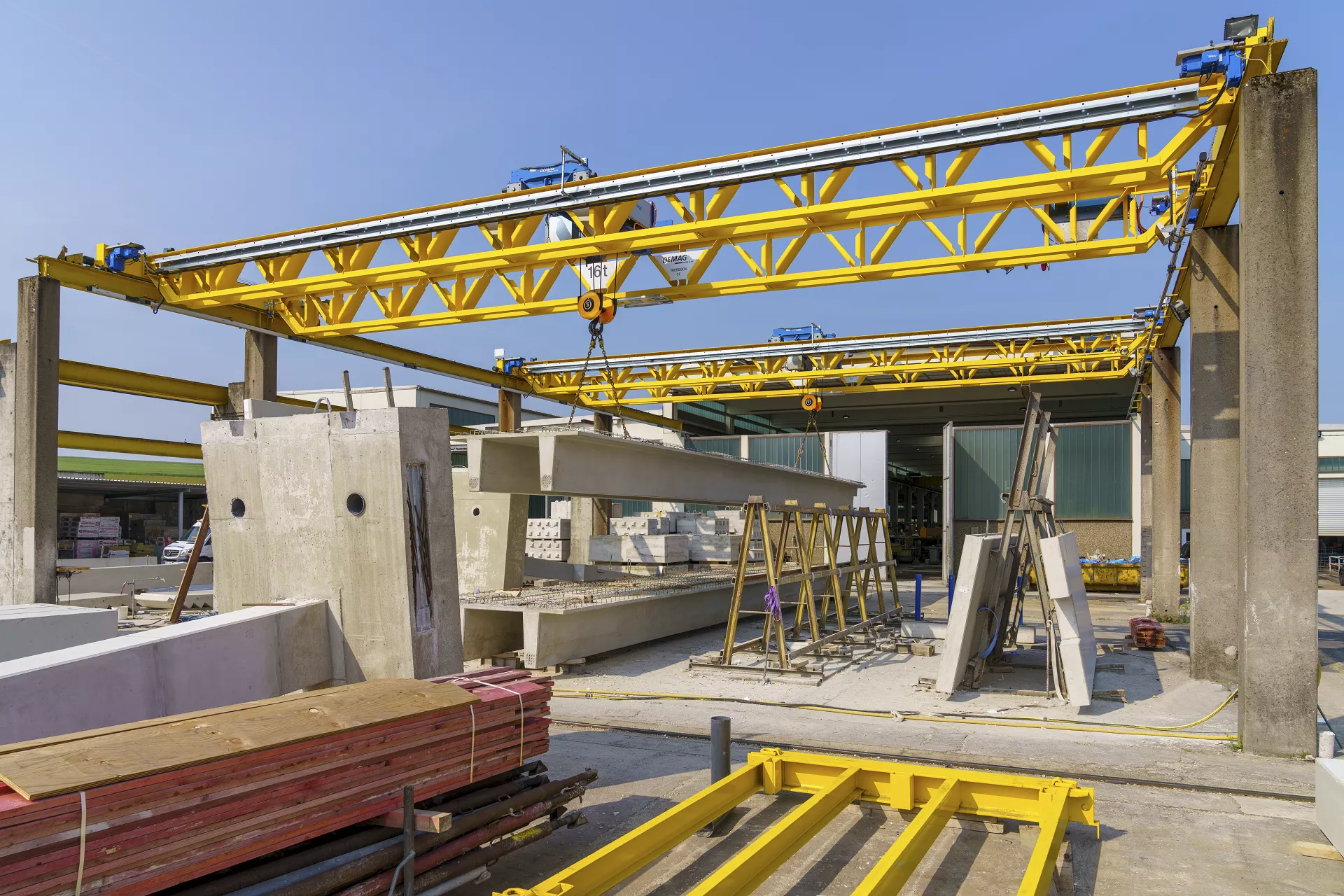
V-type crane in precast concrete production
High-profile lifting – also in smart tandem operation
Two Demag ZVKE with smart tandem for Faber & Schnepp Hoch- und Tiefbau GmbH & Co. KG
Bionic design with slim yet highly robust profile sections that are nevertheless light and elegant and allows light to pass through: Demag V-type cranes enjoy a high level of recognition in the construction industry.
In the precast concrete production facility operated by Faber & Schnepp, several V-type cranes from Demag help to ensure an efficient material flow – both in the factory and in the outdoor area. With a mini-joystick radio control, the crane operator can move the heavy and bulky precast parts using two cranes with smart tandem control.
However, when investing in a crane for day-to-day handling of precast concrete parts, factors other than the innovative and at the same time practical design also count. At Faber & Schnepp GmbH, there were quite pragmatic reasons that spoke in favour of a V-type crane (with further ones to follow).
Precast parts for efficient construction
Founded in 1932 and headquartered in Gießen, the company is one of the largest independent specialists in structural and civil engineering in the state of Hesse. As a full-service provider with qualified permanent staff, Faber & Schnepp is active in turnkey industrial and residential construction as well as in sewer and road con-struction.
Part of the group of companies is a precast concrete parts plant in Langgöns, which has been producing structural precast parts since 1967. Faber & Schnepp continuously invests in its production facilities, thereby ensuring high efficiency and producing high quality precast parts in individual shapes.
Efficient series production ensures short construction times and cost-effective structures.
It is not just a question of the mould lines but the material flow in the precast parts plant, too. After stripping the formwork, the large, often irregularly dimensioned components have to be transported to the storage location or prepared directly for transport to the construction site – efficiently, gently and safely.
Three cranes on one crane runway
In Faber & Schnepp’s precast parts production, Demag V-type cranes perform this task. Three of these cranes, each with a load capacity of 16 t, are located on a 134-m-long crane runway with a track gauge of 19 m, which covers both the interior of the production area and the open area in front of it. To transport the precast parts, which can be up to 25 m long, back and forth between the indoor and outdoor areas, the bay has an opening at the front that extends across its en-tire width. The crane profile sections are manufactured to fit this opening precise-ly.
The differences between the V-type girder and a conventional box-section girder design are recognisable at first glance. The V-shape of the girder consists of pro-file sections with tapered membrane joints. This innovative and patented design improves the oscillation characteristics by 30% (compared to a box-section girder). The deadweight of the crane and thus the load on the crane runway is reduced by an average of 17% – this enables an increased load capacity. In addition, the ser-vice life is doubled to up to 500,000 load changes. This new girder concept thus provides significantly improved efficiency for transporting loads and higher han-dling rates.
Safe, by Demag
Efficient crane operation is the main focus at Faber & Schnepp. A central factor here is the possibility of operating the cranes in smart tandem mode. This capabil-ity is required for a large proportion of newly produced precast concrete parts. In the case of the V-type crane, this is ensured by the smart SafeControl system developed by Demag. It provides safety-related monitoring of all crane travel and lifting motions. At the same time, it creates the basis for smart solutions for further safety functions, e.g. for automatic braking of the cranes at the end of the crane runway and for distancing the cranes from each other.
As far as the human-machine interface is concerned, smart tandem operating mode is implemented with DRC-MJ type mini-joystick radio control. At the touch of a button, the operator can choose between “single crane mode” and “smart tandem mode” and then safely move both cranes together with the long material.
Precise travel and positioning – even in harsh environments
The drives for long and cross travel as well as the lifting motions are all frequency controlled so that the user can control the cranes carefully and position the large-volume precast parts precisely.
Demag DMR modular rope hoists with their compact design and low approach dimensions are used for lifting. StatusBoard is a large-format LED dis-play which informs the staff in the plant about the weight of the load as well as the operating statuses of the crane.
As high as the demands on accuracy are here, the ambient conditions can be just as harsh. This is particularly the case at Faber & Schnepp, because the crane run-way leads to the outside area and every precast part produced leaves the bays on the crane hooks. The V-type cranes are set up for this: all components used are designed for a long service life and reliable operation. The cranes take the chal-lenging environment with abrasive materials in their stride, as they do any weather changes during outdoor operation. A canopy protects the travelling hoist from external influences. The compact but powerful Demag DFW travel units were developed for demanding crane applications. The Demag DRS wheel block system provides contact with the crane runway.
Adapted to site conditions
Demag has adapted the V-type cranes for Faber & Schnepp precisely to the indi-vidual conditions on site, and this applies not only to the paint finish in the cus-tomer’s corporate colour. The design of the crane girders has been optimised by lowering them so that their bottom edge is below the crane runway rail. Just one of many options for design optimisation at Demag. In addition, the compact de-sign allows short approach paths of the DMR travelling hoist to the crane girders.
Power is supplied to the travelling hoist via an energy chain. The ar-rangement of the power and signal cables on the crane bridge in the chain and guide channel prevents damage to the cables during travel. In this case, this ap-plies in particular when the cranes enter and exit the bay. There is not much space here, so freely moving cables would pose a risk.
Conclusion: The optimum solution – even under harsh operating conditions
The use of V-type cranes in the precast concrete plant shows that even under harsher operating conditions, e.g. in combined indoor/outdoor use, these cranes are a very good choice. They achieve a very high load-bearing capacity in relation to their deadweight and can be ideally adapted to individual requirements. The smart SafeControl system enables safe smart tandem operation with a single radio control – this is very important for Faber & Schnepp. And the design is also impressive in terms of functionality. Indoors the profile section design ensures that light can pass through, outside it reduces wind loads. The extremely satisfied customer Faber & Schnepp is thrilled with the new crane profile section design.
Your contact
Image gallery
Image gallery
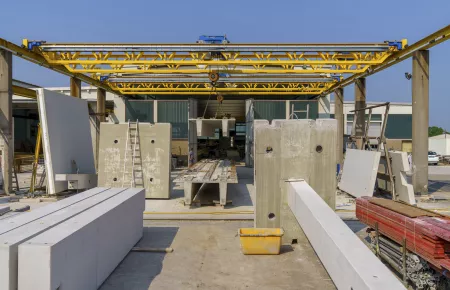
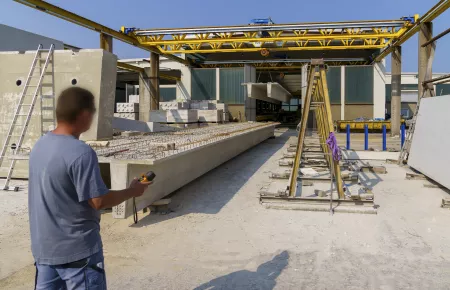
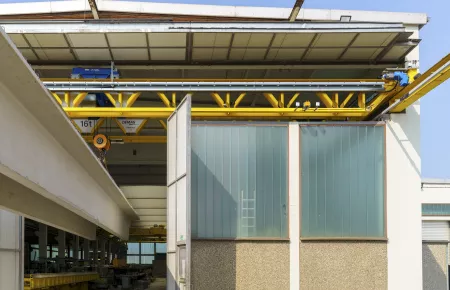
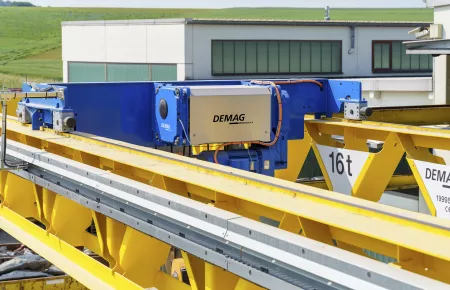