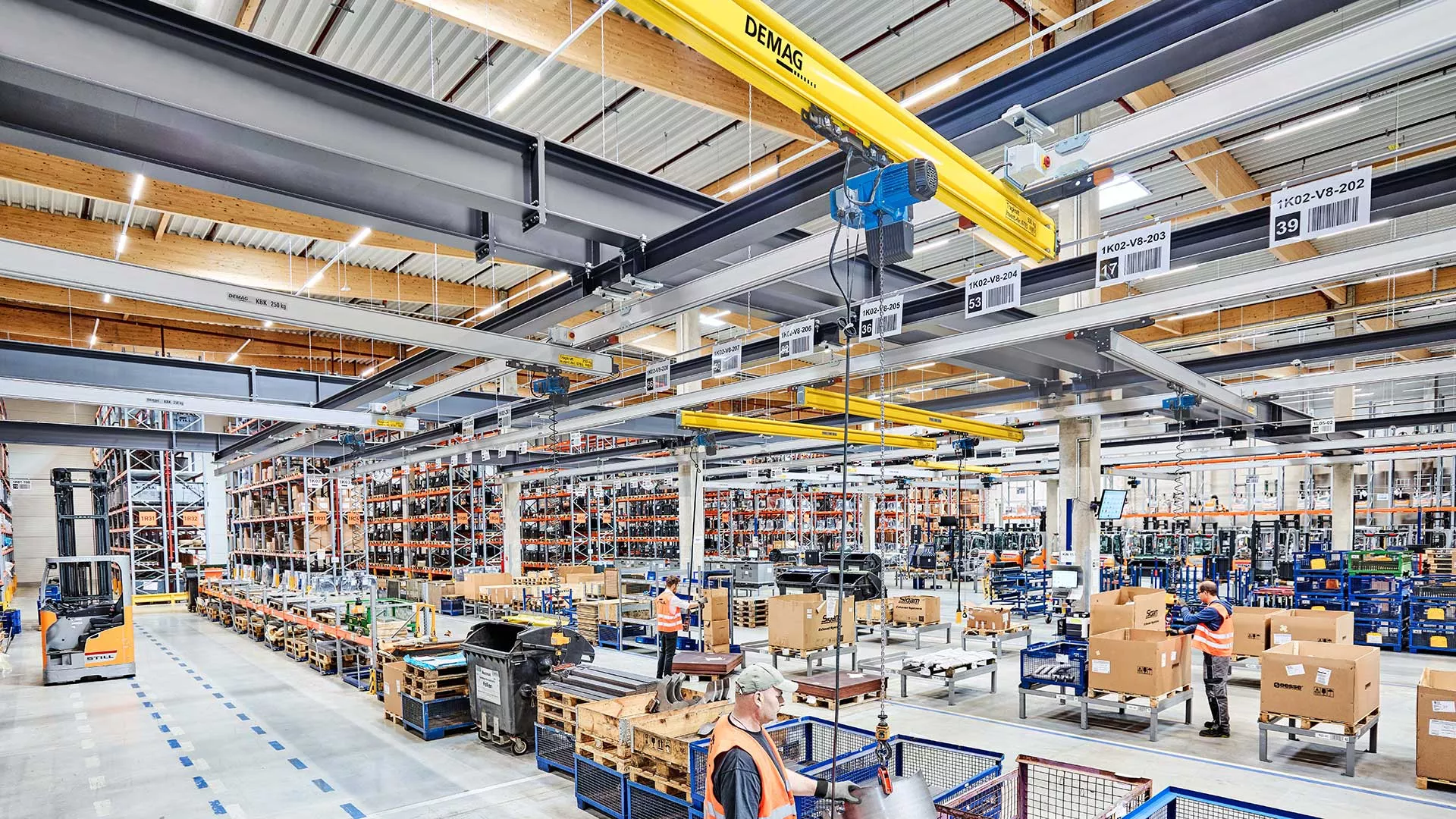
Sistema di carroponte leggero presso il centro logistico di Still
Preparazione agile degli ordini per la produzione dei carrelli elevatori
Sistema di carroponte leggero presso il centro logistico di Still
In occasione della progettazione del nuovo centro logistico ad Amburgo, nel quartiere di Billbrook, gli esperti di intralogistica di Still GmbH hanno messo sul piatto della bilancia tutta la loro competenza. Il risultato è un progetto pluripremiato su larga scala e un concetto eccezionalmente flessibile per la movimentazione e il prelievo di elementi ingombranti necessari per la costruzione di carrelli elevatori di alta qualità. Le postazioni di lavoro sono dotate del sistema di carroponte leggero Demag KBK.
Arancione e argento sono i colori di Still GmbH, e i mezzi di movimentazione a terra in queste tonalità rientrano in ogni categoria nel segmento premium: dal muletto a mano al carrello elettronico o diesel con 8 tonnellate di portata. Inoltre, Still ha saputo crearsi negli anni passati una posizione di leadership nell'ambito delle soluzioni intelligenti per l'intralogistica. Oltre ai mezzi di movimentazione a terra, la ditta propone anche soluzioni software, per esempio per la gestione del parcomezzi o sistemi di magazzino completi con tanto di automatizzazione e servizi accessori.
Quando questo specialista di intralogistica pianifica e commissiona un nuovo centro logistico interno, si può star certi che verrà creata una soluzione di “best practice”. Del resto, questo tipo di attività fa parte delle competenze principali di Still.
Centro logistico con doppia funzione
Dunque, che cosa può imparare l'operatore logistico da Still? Innanzitutto: lo sviluppo (e la gestione) degli immobili si può tranquillamente affidare a un partner che operi specificamente nel settore. In questo caso, stiamo parlando della ECE di Amburgo, che ha investito circa 30 milioni di euro per creare due capannoni con una superficie totale di 27.000 m2. In questo contesto (ed ecco qual è la seconda cosa da imparare), la prossimità rispetto allo stabilimento di produzione costituiva un fattore importante per la posizione, proprio come l'aggregazione delle aree operative precedentemente decentralizzate, ovvero il deposito degli elementi ingombranti e la spedizione dei veicoli. Ne consegue che quasi tutti gli elementi acquistati per essere montati nei carrelli, passano due volte dal centro logistico: prima della produzione come componenti e dopo la produzione come carrello finito.
Sistema vocale Pick-by-Voice per la predisposizione ordine degli elementi voluminosi
Nell'area del nuovo centro logistico dedicata al prelievo degli ordini, vengono preparati gli elementi voluminosi di cui necessita lo stabilimento di Amburgo per la costruzione dei suoi carrelli di qualità, ovvero vengono riconfezionati con gli imballaggi propri di Still e prelevati “just in sequence”. Questi elementi possono essere per esempio i sedili, il radiatore o gli pneumatici. Nel caso dei pezzi del telaio e della carrozzeria, la predisposizione degli ordini è più complessa.
“Qui, i dipendenti ‘impacchettano insieme' tutti i componenti in acciaio e lamiera che servono per costruire il carrello elevatore”, afferma Timo Koppe, pianificatore logistico presso Still. Tutti i pezzi finiscono poi in un container speciale, per poi essere montati uno per uno in produzione.”
Il personale riceve le informazioni necessarie per la predisposizione dell’ordine mediante il sistema vocale “pick-by-voice”. Una navetta trasporta in seguito tutti i componenti necessari per la costruzione di un carrello elevatore allo stabilimento, che dista appena qualche centinaio di metri.
Requisito fondamentale: la flessibilità
Gli esperti di logistica di Still hanno esaminato da vicino il design ergonomico delle postazioni di prelievo degli ordini - e hanno optato per il sistema di gru leggere Demag KBK. Il sistema è stato presentato per la prima volta 55 anni fa e da allora è oggetto di sviluppo costante. Il principio di base è però sempre lo stesso: su un sistema di travi, si spostano carriponte leggeri che l'operatore può muovere esercitando una forza minima e quindi con un affaticamento fisico ridotto.
Oggi, proponiamo una linea di KBK veramente ricca, adattabile a pressoché tutte le attività di montaggio, predisposizione ordini e spedizione. Per prima cosa, si sceglie se realizzare le rotaie e i ponti in acciaio o con canaline in alluminio, tenendo presente che anche domande semplici come questa possono avere molteplici possibilità di risposta, proprio come dimostra l'esempio del centro logistico di Still. Qui, i due sistemi sono stati combinati. Le vie di corsa del carroponte e parte dei ponti sono in alluminio, mentre i ponti con portate maggiori (da 250 kg a 2 t) sono realizzati in acciaio.
In tutti gli impianti KBK, Still impiega profili con conduttori interni, che si possono utilizzare anche nei ponti più lunghi, in modo da coprire aree di lavoro ampie. In questo progetto, cinque carriponte si spostano su una stessa via di corsa. Questi sistemi di movimentazione si possono realizzare senza sospensioni e non solo è possibile integrare le svariate opzioni previste dal sistema costruttivo modulare, ma si possono anche prendere in considerazione le richieste speciali.
Il sistema KBK è utilizzato in tutto il mondo per le più disparate operazioni di predisposizione ordini, maneggiamento e montaggio. In oltre 50 anni, Demag ha installato impianti per oltre 10.000 chilometri di profili KBK in tutto il mondo e nei settori più diversi. Per Still, questo sistema è perfetto, perché consente la massima flessibilità.
Timo Koppe: “Non dobbiamo solo gestire una grande varietà di pezzi, ma dobbiamo anche prelevare i componenti più disparati: lamiere di formato ingombrante, ma anche componenti più piccoli sebbene pesanti e, tutto questo, in una sola postazione di lavoro. Il sistema di movimentazione deve perciò essere flessibile, soprattutto perché vengono costantemente aggiunti nuovi componenti.”
Tecnologia di movimentazione ispirata alla modularità
Inoltre, sebbene la logistica sia simile a quella della produzione automobilistica, le quantità prodotte sono inferiori e la varietà è estremamente elevata. ogni singolo tipo di carrello elevatore è disponibile in tante versioni e le possibilità di scelta non riguardano solo la dotazione, ma anche l'altezza, la lunghezza e la larghezza dell'intero dispositivo.
All’ingresso del capannone, dove si svolge anche la predisposizione ordini, sono stati installati sei impianti KBK con due o quattro postazioni di lavoro per carroponte su ogni via di corsa. Tutti sono dotati di alimentazione e segnali tramite conduttori interni. In tutte le postazioni di lavoro, non importa che si maneggino “fast mover” (montati in quasi tutti i carrelli elevatori in lavorazione) o “slow mover”: il sistema di carroponte leggero dà i suoi risultati, anche perché Still sfrutta intensivamente tutte le possibilità del sistema modulare KBK Demag.
Spedizione dei veicoli: si chiude con il KBK e la gru a portale
Nel reparto spedizioni del centro logistico, i carrelli appena finiti vengono completati in vista della consegna. Qui, si eseguono i controlli finali, si monta la batteria e si aggiungono le forche ordinate dal cliente. In questo reparto, Still si destreggia con un sistema KBK, che viene utilizzato in cinque postazioni di lavoro, fra l'altro per il montaggio delle forche e le griglie di protezione del carico. In totale, nelle due superfici di logistica, sono presenti sette impianti KBK, con 192 metri di vie di corsa e 18 postazioni di lavoro per carriponte.
Nel secondo capannone, dove si collocano tra l'altro i depositi a blocchi per i componenti voluminosi, è presente inoltre una gru a bandiera a colonna con uno sbraccio nientemeno di sette metri. Quest'ultim permette di disimballare, riconfezionare e maneggiare carichi pesanti, come per esempio gli alberi di trasmissione, raggiungendo durante questa operazione un raggio d'azione considerevole.
Montaggio della batteria con una gru a portale da 3,2 t
Per il montaggio della batteria, i progettisti hanno realizzato una soluzione speciale, sulla base del principio modulare Demag. Visto che le batterie sono molto pesanti e devono essere posizionate con precisione, Still ha scelto una gru da 3,2 tonnellate, che si aggancia a un carroponte sospeso nel contesto di un portale, per coprire l'area di lavoro compatta adibita al montaggio delle batterie. Questo espediente si può realizzare qui senza problemi, perché in questa postazione di lavoro non si svolgono altre attività e non è necessario uno sbraccio particolarmente grande.
Maneggiamento sicuro di carichi pesanti... con il Manulift
Nelle postazioni di lavoro adibite alla movimentazione di carichi pesanti o poco maneggevoli, gli operatori lavorano con il Manulift di Demag. Quest'ultimo consente l'utilizzo del paranco a catena con una sola mano, cosicché l'operatore può utilizzare l'altra mano per guidare il carico.
Timo Koppe: “Quando per esempio si devono sollevare e portare in posizione le lamiere per la costruzione del telaio oppure si devono maneggiare strutture saldate ingombranti, si tratta di un aiuto importante per l'operatore”.
Dato che il principio del Manulift si è rivelato così fruttuoso, Still ha deciso di adottarlo anche in altre postazioni di lavoro KBK già esistenti. A tal fine, Demag ha realizzato una struttura speciale con una portata maggiorata di 500 kg.
Importante partecipazione alla progettazione in prima persona
I tecnici della logistica di Still hanno lavorato principalmente in autonomia alla progettazione, tuttavia sono stati supportati dagli esperti di Demag operativi presso gli uffici di rappresentanza di Amburgo. I gestori sono assolutamente contenti del risultato ottenuto nel nuovo centro logistico. Anche il concept complessivo convince su tutta la linea: per questo progetto, la ditta specializzata in progettazioni ECE ha ricevuto il riconoscimento “Logix Award 2017”, che viene assegnato ogni due anni agli sviluppi logisticoimmobiliari più interessanti.
Esempi di applicazione
Esempi di applicazione
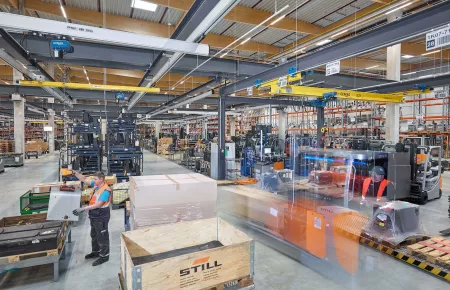
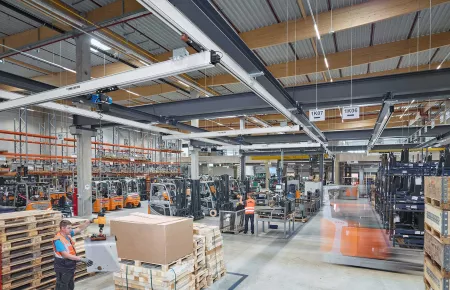
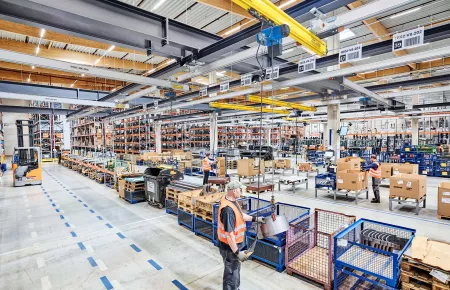
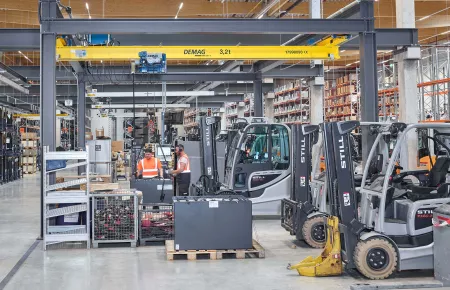