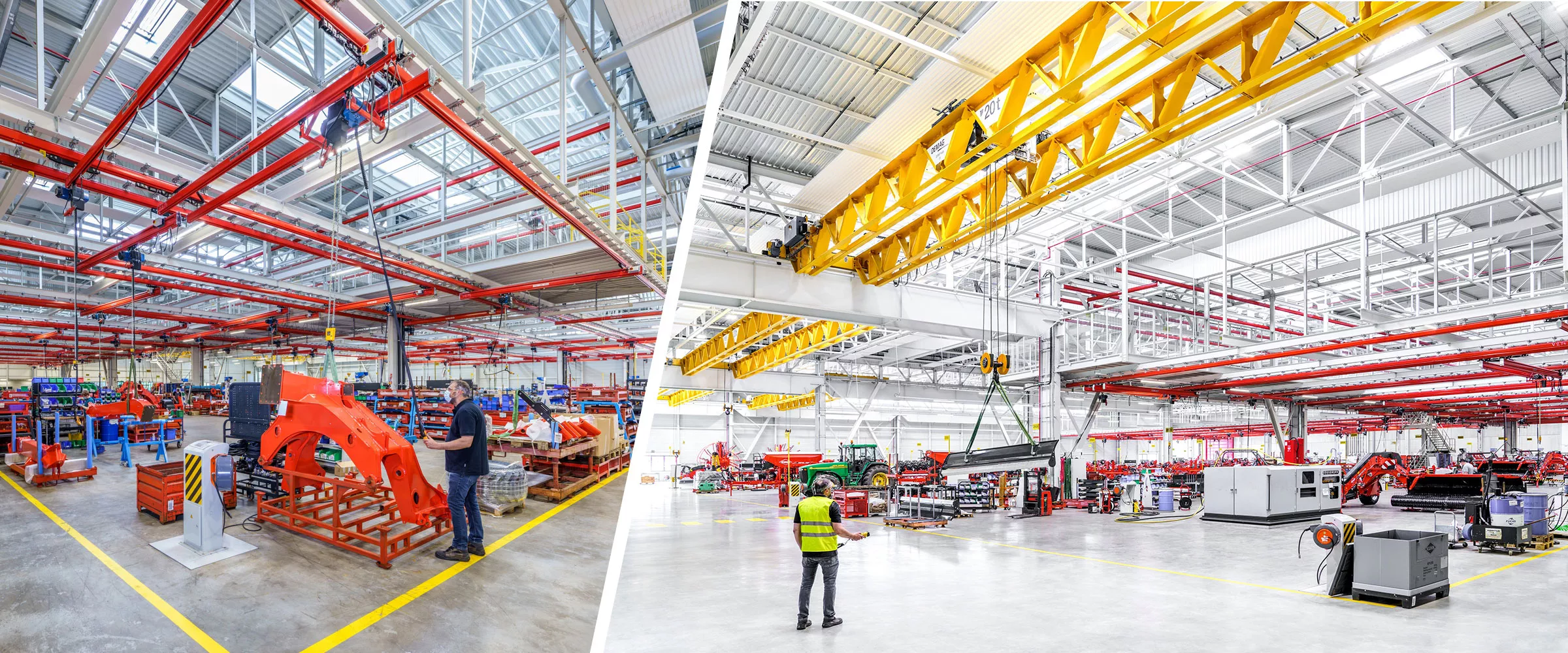
Matériels agricoles de l’Est de la France
Solution de manutention flexible et modulaire
Neuf ponts type V et 3,2 km de profilés KBK avec 120 palans à chaîne à courant alternatif pour KUHN MGM SAS
Le groupe KUHN
Dans le nord-est de la France, près de Strasbourg, se trouve l’un des principaux fabricants mondiaux de machines agricoles. Le groupe de sociétés KUHN promet aux agriculteurs une force d’innovation et une grande qualité à des prix adaptés au marché. Plus de 5 000 employés dans le monde entier travaillent actuellement à la réalisation de cette promesse sur de nombreux sites de production et de vente.
Depuis l’Alsace vers le monde entier
L'entreprise a d'abord été une forge créée en 1828 par Joseph Kuhn. La forge s’est rapidement spécialisée dans la fabrication de balances et d’instruments de mesure. L’entreprise s’installe à Saverne en 1864 et se spécialise alors dans la construction de matériel agricole. Depuis lors, c’est autour de Saverne et dans la commune limitrophe de Monswiller que l’on poursuit le développement de faucheuses, faneuses, andaineuses, hacheuses ainsi que d'outils de travail du sol et de semoirs.
La mission
La production dans l’usine principale de Saverne a été étendue à plusieurs reprises au cours des dernières décennies et adaptée à la demande toujours croissante de machines agricoles de plus en plus grandes. Cependant, la production était limitée par la largeur des baies maximale de 15 mètres, si bien qu’une nouvelle usine de montage a été construite dans la commune voisine de Monswiller il y a quelques années. L’abréviation « MGM » signifie « Montage Grande Machine » et indique que des largeurs de couloir allant jusqu’à 20 mètres sont nécessaires pour assembler les machines agricoles de dernière génération. KUHN a construit un hall de production moderne pour la production en flux de grandes machines agricoles.
Au total, l’usine d’assemblage a été agrandie de 20 461 m². Dans le détail, l’extension est divisée en 11 065 m² pour un nouveau hall de montage, 5 437 m² pour une extension du hall logistique et 3 017 m² pour un hall d’expédition. Des espaces extérieurs supplémentaires et la construction d’une nouvelle cantine complètent les locaux de l’usine.
Un schéma de production efficace
L’usine principale de Saverne produit de petites machines agricoles et des composants pour le MGM de Monswiller. C’est là que sont assemblées les grandes machines utilisées pour la fenaison, le travail du sol et les semailles. Ces composants, ainsi que les pièces achetées, sont prélevés dans la zone de réception des marchandises, le « magasin », et acheminés vers les lignes d’assemblage. Chaque mois, ce secteur traite environ 100 tonnes de matériaux. Les pièces achetées et les autres composants sont revêtus de poudre et laqués dans l’atelier de peinture interne de KTL. Le montage se fait à l’intérieur des lignes : Dans les différentes stations de montage, les machines agricoles sont assemblées étape par étape et préparées pour l’expédition après le montage final et un test de fonctionnement.
Sur le côté de la ligne d’assemblage se trouvent des zones de livraison pour l’intralogistique. Les employés ont besoin d’une solution de manutention aérienne pour transporter les marchandises livrées de l’entrepôt et de l’atelier de peinture au site de montage. En outre, la manutention du matériel aux postes de travail individuels est cruciale pour relier précisément les composants et rendre la manipulation aussi aisée que possible pour les employés. Lors du montage des modules au châssis principal de la machine agricole, la précision de l’appareil de levage en matière de positionnement et de contrôle est d’une importance capitale pour un travail efficace. Les ponts légers sont donc indispensables pour chaque étape de travail.
Au bout de la chaîne de production, des ponts roulants aident au montage final. Selon le type et la taille de la machine agricole, des composants volumineux et lourds sont montés sur le châssis principal et doivent donc également être soulevés et positionnés. Enfin, un test de fonctionnement est effectué et les machines agricoles finies sont transportées vers le nouveau hall d’expédition. Des ponts sont alors utilisés pour le chargement des camions.
La solution
L’expansion de la production va de pair avec l’investissement de moyens de manutentions complémentaires chez KUHN MGM : 9 ponts roulants de type ZVKE à profil type V et une capacité de charge respective de 20 tonnes ainsi que 120 palans à chaîne de type DC-Pro soutiennent les nouvelles lignes de montage et l’expédition. Avec une extension de 3,2 kilomètres de profilés KBK, la nouvelle ligne de montage sera également entièrement couverte par l’ensemble modulaire KBK.
KUHN MGM et Demag en France ont planifié les livraisons de manière à ce que les nouveaux ponts puissent être assemblés par sections et dans les délais. Le montage des ensembles modulaires KBK a été effectué par le personnel de maintenance de l’entreprise après une formation approfondie.
Le système modulaire KBK, un produit sûr et efficace
Le long des lignes de montage de Monswiller, un réseau dense de système modulaire KBK couvre le plafond du hall de production. Les employés utilisent des ponts monopoutre et bipoutre KBK pour déplacer les différents composants des machines agricoles de la ligne logistique vers les postes de montage des lignes de production, qui mesurent environ 100 mètres de long et 25 mètres de large. Lors de la planification de l’usine, une attention particulière a été prêtée à ce que le KBK soit installé sur toute la surface et soit donc disponible pour apporter une aide précieuse à chaque étape des travaux.
Les palans à chaîne DC-Pro d’une capacité de 1000kg sont déplaçables manuellement et les 2000kg sont motorisés pour une meilleure ergonomie. Avec les deux types d’entraînement, le transport des composants sur le site de montage se fait sans problème, ce qui permet de monter les machines agricoles de manière efficace et ergonomique. Les liaisons articulées entre la poutre de pont et le chariot permettent une manutention sans heurts des modules pré-assemblés depuis la station d’assemblage jusqu’au châssis de la machine. Les vitesses partiellement réglables en continu et réduites des palans à chaîne DC-Pro aident les opérateurs du pont à aligner les modules facilement et avec précision pendant le montage. Le montage d’une pièce telqu’un tambour peut ainsi être réalisé de la même manière que le montage d’une unité électronique ou hydraulique.
Confort et sécurité lors de la manutention de charges avec le palan à chaîne DC-Pro
La compatibilité des composants Demag entre eux permet même à KUHN MGM d’utiliser des palans à chaîne d’ancienne génération de son stock, par exemple de type DK ou même PK. Cependant, le personnel s’est habitué aux avantages de la dernière génération du type DC-Pro : Le positionnement des composants est absolument précis avec deux vitesses, même à faible vitesse. Avec des capacités de charge de 500 à 2 000 kg et une course du crochet uniforme de 5 mètres, les palans à chaîne peuvent être utilisés de manière flexible sur tous les postes de travail. Le câble de commande réglable en hauteur de la boîte à boutons de commande DSC offre une ergonomie optimale. La forme ergonomique de la poignée et sa maniabilité permet d‘augmenter l’efficacité lors du montage.
Le palan à chaîne DC-Pro est doté d’un réducteur, d’un accouplement à friction et d’un frein avec des composants de haute qualité qui ne nécessitent aucun entretien pendant 10 ans. Grâce au débrayage automatique de l’accouplement à friction et au freinage automatique en cas de défaillance de la commande, les employés de KUHN peuvent compter sur la fiabilité du DC-Pro sur leur poste de travail. Les fonctions de sécurité du type de palan à chaîne répondent au moins au niveau de performance c et à la catégorie 2 selon la norme EN ISO 13849-1.
Fiabilité absolue avec une efficacité élevée
Les neuf ponts roulants bipoutre ZVKE à profil type V fournis offrent également une fiabilité et une efficacité maximales. La structure innovante avec des membranes de liaison effilées permettent de réaliser un design de type V qui laisse passer la lumière. Grâce à la réduction des besoins en matériaux, la poutre de pont a un poids mort plus faible, ce qui a un effet positif sur la statique du hall. Les portées des ponts roulants vont de 10,4 mètres à 28,3 mètres.
« J’ai vu le pont pour la première fois chez un autre de vos clients et j’ai été immédiatement impressionné. On ne voit presque pas la poutre de pont, et elle laisse passer beaucoup de lumière dans le hall. Cela donne également l’impression que le pont est très léger. » – Stéphane Schissele, KUHN SAS
Avec une capacité de charge de 20 tonnes pour chaque pont, KUHN MGM sera à l’avenir en mesure de soulever des machines agricoles plus grandes et plus lourdes pour le montage final et de les transporter jusqu’à l’expédition. Cinq ponts soutiennent les étapes de montage final à la fin de la chaîne de production pour monter les composants pré-assemblés et désormais plus lourds. La puissance de levage et surtout le positionnement précis des composants grâce au système de commande en continu représentent une énorme simplification du travail.
Quatre autres ZVKE sont utilisés dans la nouvelle zone d’expédition pour charger sur des camions des ensembles de composants et les machines agricoles déjà emballés. Les expéditions de Monswiller sont effectuées vers des clients du monde entier.
Le palan à câble modulaire DMR Demag permet l’intégration d’aides mécaniques et électriques. La commande à régulation de fréquence des ponts joue un rôle important dans le confort et permet aux opérateurs de la zone d’expédition de prendre et de déplacer avec précision les palettes contenant des composants de machines agricoles ou des machines agricoles complètes. Le démarrage et l’accélération des mouvements sont progressifs, de sorte que l’opérateur peut contrôler précisément le mouvement du pont, du chariot ou de levage et se concentrer sur La dépose délicate de l‘ensemble dans le camion dans le camion.
Fonctionnement du pont en toute sécurité
Sur les neuf ponts, le système SafeControl surveille et sécurise en continu le fonctionnement. Un fin de course à deux cranes empêche que le pont ou le chariot ne heurte les butées d’extrémité. Lorsque le premier fin de course est atteint, la translation du pont ou la direction du chariot enclenche la commutation grande vitesse/petite vitesse pour le mouvement de translation. Dès que le deuxième fin de course est enclenché, les entraînements du pont ou de la direction du chariot sont arrêtés et la translation est freinée en douceur. Le balancement de la charge est empêché par la combinaison d’une commande continue et d’interrupteurs de fin de course, de sorte que la charge ne subit aucun dommage et ne cause aucun dommage au camion ou à la zone environnante. L’opérateur du pont bénéficie de l’assistance électronique et est soutenu et protégé par le pont dans les situations imprévisibles.
Deux des ZVKE circulent sur la voie de roulement dans la nouvelle section de production. Pour éviter les collisions, un contrôle optique de la distance entre les ponts est utilisé : Des capteurs laser doubles mesurent de manière redondante la distance entre les différents ponts sur la voie de roulement et si les distances prédéfinies sont dépassées, le pont concerné est arrêté en deux étapes et sécurisée. Dans la première phase, le pont ne peut plus être déplacé qu’à faible vitesse, dans la deuxième phase, le pont s’arrête en toute sécurité. Ce concept d’arrêt de sécurité indépendant avec un matériel à deux canaux correspond à la catégorie de sécurité 3 selon la norme EN 13849-1.
La lecture instantanée des états du pont roulant
L’opérateur peut lire le poids de la charge au crochet sur un écran déporté de type StatusBoard monté sur la poutre du pont. En outre, le StatusBoard permet de visualiser en temps réel les états de fonctionnement actuels du pont. Il s’agit, par exemple, de la capacité de charge, de la charge totale, d’un état de surcharge, des informations de service ou des fonctions d’assistance activées de la commande de sécurité SafeControl - un fonctionnement transparent et surtout sûr du pont.
Les particularités
L’ensemble modulaire KBK permet à KUHN MGM de bénéficier d’un système modulaire de manutention pour les poste de travail, qui peut être étendu à tout moment si nécessaire. Les voies de roulement ainsi que des potences pivotantes murales et sur piliers transportent les composants sur toute la surface. Les variantes KBK en acier et en aluminium conviennent également aux diverses exigences et peuvent également être combinées ultérieurement.
La facilité de mouvement des composants Demag permet une manipulation rapide et sûre et en même temps un positionnement précis et sans effort des différentes pièces détachées pour l’assemblage. L’ensemble modulaire KBK assure ainsi des flux de travail efficaces et augmente la productivité et l’efficacité.
La construction à profil type V avec des joints de membrane permet d’économiser du poids mort et a donc un effet positif sur la statique du hall. La commande de sécurité intelligente SafeControl offre la plus grande sécurité possible pendant l’utilisation du pont. Les fins de course pont et la détection de distance des ponts assistent l’opérateur électroniquement et contribuent à prévenir les dommages involontaires dans l’environnement de travail du pont. En combinaison avec la commande en continu de la translation du pont et de la direction du chariot du pont, ainsi que des mouvements de levage, l’utilisation du pont devient plus confortable.
Entretien
Nous avons réalisé un entretien avec Stéphane Schissele, responsable des bâtiments et de la maintenance, chez KUHN MGM SAS à Monswiller, France.
Demag : M. Schissele, pouvez-vous présenter brièvement la société KUHN MGM SAS et le site de Monswiller ?
Stéphane Schissele (KUHN MGM SAS) : Monswiller est situé dans le département du Bas-Rhin, et donc en Alsace. Notre entreprise est solidement ancrée dans cette région et est désormais représentée par deux sites, à Saverne et Monswiller. L’usine de production et de montage de Saverne est le siège du groupe KUHN. Monswiller abrite l’usine de montage MGM et la production de pièces de rechange. L’abréviation « MGM » signifie « Montage Grande Machine ». C’est là que sont assemblées les grandes machines agricoles. L’usine de montage a été ouverte en 2008 avec quatre lignes de montage et avait jusqu’alors une production annuelle de 9 000 machines. Avec l’extension, la capacité du site a été doublée. Actuellement, ce sont 350 employés qui fabriquent des machines agricoles pour la fenaison, le travail du sol et les semoirs. En outre, MGM est spécialisé dans la production de machines saisonnières.
Demag : Pour quelles raisons l'investissement réalisé sur le site s'est-il avéré nécessaire ?
M. Schissele : Tout d’abord, il était important pour nous d’augmenter la capacité de production de quatre à huit lignes de montage. Parallèlement, nous avons pu ajouter notre propre zone de logistique et compléter le processus de fabrication avec un nouveau hall d’expédition à Monswiller. Nous avons l’ambition d’être en mesure de nous adapter de manière dynamique aux exigences changeantes de nos clients. Il y a quelques années, nous nous contentions de Saverne avec des largeurs de baies de 14 ou 15 mètres. Mais au fil des ans, celles-ci étaient devenues trop étroites, de sorte que nous disposons aujourd’hui d’une largeur de travail de 20 mètres sur les chaînes de montage de ce site. C’est extrêmement important pour nous, car les machines sont de plus en plus grandes et larges. Il a donc fallu plus d’espace pour la production. Pour ces raisons, la construction de la nouvelle usine et la récente extension étaient essentielles pour nous et offrent le bon environnement de production pour les années à venir.
Demag : Pouvez-vous nous donner une idée de l’ampleur de l’extension ?
M. Schissele : Nous avons réalisé une extension de près de 20 000 m² pour les zones productives telles que l’assemblage, la logistique et l’expédition.
Demag : Quelles tâches les produits Demag assurent-ils ?
M. Schissele : Les produits Demag permettent la manutention des matériaux sur les différents postes de travail de l’usine. L’ensemble modulaire KBK demande peu d’efforts à nos employés lors du transport des composants dans notre atelier de peinture KTL et lors du pré-montage. Les palans à chaîne installés dans les installations KBK ont généralement une capacité de charge de 500 kg à 1000 kg et sont utilisés pour la manutention et le positionnement des composants lors du montage. Une fois les modules pré-assemblés, nous avons besoin d’appareils de levage pour transporter les modules vers le châssis principal de la machine. La vitesse lente et partiellement réglable en continu des palans à chaîne DC-Pro Demag permet à nos employés d’aligner les éléments d’assemblage de manière simple et précise.
« Montage précis du module grâce à la vitesse lente et réglable en continu des palans à chaîne DC-Pro Demag »
Au bout des lignes de montage, l’assemblage final des machines a lieu à l’aide de ponts type V d’une capacité de charge de 20 tonnes.
Demag : Quelles exigences concrètes la société KUHN a-t-elle posées vis à vis des produits Demag ?
M. Schissele : Pour nous, la fiabilité élevée des composants est extrêmement importante pour garantir une sécurité optimale aux opérateurs. Comme nous sommes partenaires de Demag depuis plusieurs décennies, nous sommes conscients de la durabilité des produits et nous l’exigeons.
Demag : Pourquoi la société KUHN a-t-elle préféré les solutions de postes de travail Demag ?
M. Schissele : À Saverne, nous exploitons encore un très grand parc d’appareils de levage de la génération PK (ndlr : les palans à chaîne de la série PK ont été fabriqués de 1961 à 1995). Nous sommes donc parfaitement conscients de la longévité des produits. Au cours des dernières décennies, des palans à chaîne de différentes générations ont été utilisés quotidiennement et continuent à être pleinement fonctionnels. Si les employés demandent des vitesses de levage réglables en continu sur leur poste de travail, nous modernisons les appareils de levage avec des équipements de la nouvelle génération DC. Nous avons testé d’autres produits, mais la vitesse des produits Demag est parfaitement réglable, de sorte que le montage des composants est correct à cent pour cent. Le gain en précision est exceptionnel avec les appareils de levage Demag.
« Le gain en précision est exceptionnel avec les appareils de levage Demag. »
Une autre raison est que les produits peuvent être facilement déplacés à la main. Les appareils de levage fonctionnent presque exclusivement sur plusieurs kilomètres de rails KBK. Comme nous l’avons déjà mentionné, les palans à chaîne ont une capacité de charge allant jusqu’à 1000 kg, vous pourriez donc penser que leur transport à la main pourrait être difficile : mais la grande facilité d’utilisation du KBK est simplement énorme ! À Saverne et à Monswiller, des charges allant jusqu’à 1000 kg et des portées allant jusqu’à 7 mètres peuvent ainsi être déplacées manuellement sans aucun problème. Lorsque nous devons manipuler des charges de 2000 kg ou plus, un mécanisme électrique est bien sûr nécessaire.
« (...) mais la facilité d’utilisation du KBK est simplement énorme ! »
Il est également indispensable pour la planification et la flexibilité de la production que nous puissions adapter la disposition des postes de travail. La modification ou l’extension des installations KBK est possible à tout moment et, dans certains cas, les ponts des lignes de production individuelles sont démontées et remontées 30 ou 40 fois par an, par exemple pour changer de direction. Le système KBK est installé ici à Monswiller de manière à couvrir la plus grande surface possible. Nous ne pouvons jamais dire à l’avance si la chaîne de montage restera la même pendant huit ou dix jours. Les exigences peuvent même changer tous les jours. Il y a 20 ans, 1000 machines étaient assemblées sur une même ligne, aujourd’hui il y en a peut-être 80, 60, 50, parfois seulement 40. Les séries sont de plus en plus petites, ce qui signifie que les lignes doivent rester flexibles. De même que les voies de roulement, bien entendu.
La solution que nous utilisons avec KBK depuis plus de deux décennies est la meilleure pour nous. Nous pouvons rapprocher les pièces au plus près de la ligne et les employés peuvent facilement transporter les composants sur le poste de travail pour les assembler. Cela est possible d’un poste de travail à l’autre et le long des lignes de production de 100 mètres de long jusqu’à ce que nous puissions tester la machine agricole finie à la fin de chaque ligne et la préparer pour l’expédition. Les pont Demag type V ont pour mission l’assemblage final et la manutention des produits finis.
Demag : Que pensez-vous de la conception du profil en V des poutres de pont ?
M. Schissele : C’est vraiment une nouveauté. Nous connaissons le KBK depuis des années, mais le profil type V des ponts est vraiment une innovation. J’ai vu le pont pour la première fois chez un autre de vos clients et j’ai été immédiatement impressionné. On ne voit presque pas la poutre de pont, et elle laisse passer beaucoup de lumière dans le hall. Cela donne également l’impression que le pont est très léger.
Le faible poids mort a naturellement un effet positif sur la charpente métallique du hall. Et en plus, le design est absolument esthétique. Si l’on regarde aussi les spécifications techniques et que l’on se rend compte de la capacité de charge et des vitesse possibles, malgré le faible poids mort, je dois dire que c’est assez impressionnant. Cela se traduit bien sûr par une usure réduite des galets et des voies de roulement, ce qui constitue donc un effet positif sur nos coûts. Nous avons également consulté la concurrence avec des ponts caissons traditionnels qui offrent un profil plus lourd et encombrant, nous obligeant à remonter les voies de roulement. La différence pouvait atteindre un mètre dans certains cas. Cela ne nous convenait pas, tout simplement, et nous avons choisi le pont roulant Demag type V.« Le pont type V est un très bon produit. Nous avons donc immédiatement opté pour le nouveau design et nous n’avons pas été déçus. »
Les ponts nous serviront également dans une perspective d’avenir et, avec une capacité de charge de 20 tonnes, elles sont actuellement de taille un peu plus importante que ce dont nous avons besoin. Cependant, comme nous l’avons appris récemment, nos machines sont de plus en plus grandes et donc de plus en plus lourdes et une marge de 5 tonnes de capacité de charge en plus n’a pas fait de différence en termes de prix.
Demag : Comment vous assurez-vous que les installations sont disponibles à tout moment ?
M. Schissele : La gestion simplifiée des pièces de rechange est un grand avantage. Nous commandons un grand nombre de pièces de rechange directement dans le Demag Shop. Un système rapide et efficace dans lequel vous pouvez également voir le nombre de suspensions KBK et consulter les dessins. C’est vraiment très bien fait. Et après la simulation, je peux commander les produits directement. Nous le faisons très souvent et le processus, de la collecte d’informations à la sélection et à la livraison, est toujours extrêmement rapide. J’avais l’habitude d’utiliser le catalogue pour trouver les meilleurs produits de manière efficace et rapide. Le Shop a encore simplifié ce processus.
Nous disposons d’un entrepôt avec des produits Demag sur les deux sites de production et donc d’un approvisionnement central en pièces de rechange. Nous y stockons des produits datant parfois de plus de 25 ans, et presque tous sont compatibles entre eux, ce qui constitue un énorme avantage pour nous et nous permet de conserver une certaine flexibilité.
Demag : Avez-vous également planifié d’extension via le Demag Shop ?
M. Schissele : Pour la configuration de projets de petite taille, jusqu’à trois ponts environ. Ça fonctionne plutôt bien ! Lorsque j’ai un projet complet, il est toujours préférable d’avoir un partenaire qui peut nous soutenir et avec qui nous pouvons planifier le processus. L’équipe commerciale de Demag a été très, très efficace sur ce projet. Les pièces sont arrivées chez nous secteur par secteur. Les pièces ont été pré-triées de manière à ce que tous les composants KBK et les appareils de levage requis soient assemblés pour le secteur concerné. Nous avons discuté des délais de livraison à l’avance et les différents colis sont arrivés sur notre chantier semaine après semaine. Cela nous a permis d’éviter d’avoir un grand stock sur place et nos employés pouvaient ainsi assembler le système directement après la livraison.
« Nous sommes entièrement satisfaits des solutions proposées par Demag. »
Demag : Quels avantages parlent en faveur des solutions Demag utilisées ?
M. Schissele : Les produits Demag offrent une grande flexibilité et permettent la fabrication de modules complexes sur une surface réduite. La durabilité des produits est excellente. La capacité de charge est également très bonne et les différents composants peuvent encore être commandés sans problème après 20 ou 30 ans. Nos normes élevées de fiabilité se reflètent également dans les produits Demag. Nous sommes entièrement satisfaits de nos solutions.
Demag : Quelles sont jusqu'ici les impressions dont les employés vous ont fait part au sujet de leur travail avec les produits Demag ?
M. Schissele : Les employés sont très heureux ! Ils peuvent transporter les composants à grande vitesse. Mais le plus grand avantage réside dans la précision et l'efficacité absolues du positionnement dans le cadre de l'assemblage des modules. Tant avec les ensembles modulaires KBK sur les postes de travail qu’avec les ponts à la fin des chaînes de montage et dans la zone d’expédition.
Galerie d'images
Galerie d'images
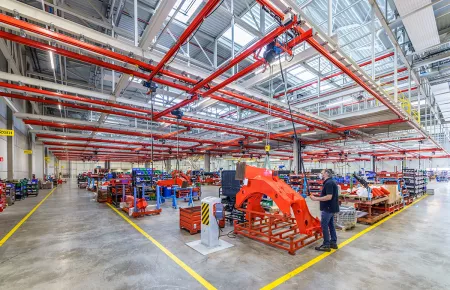
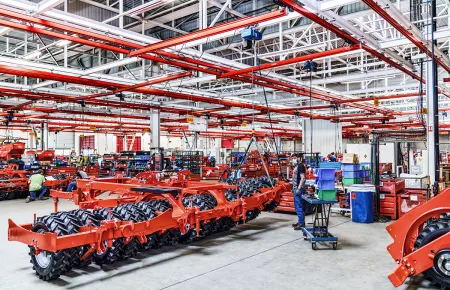
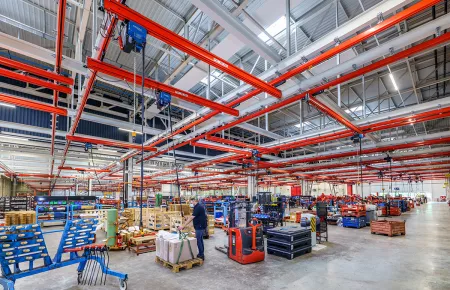
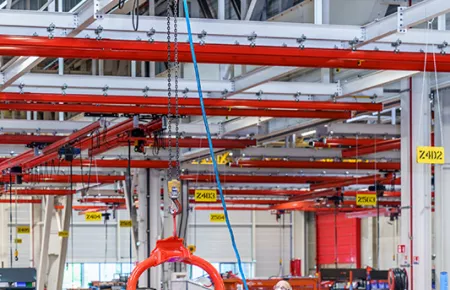