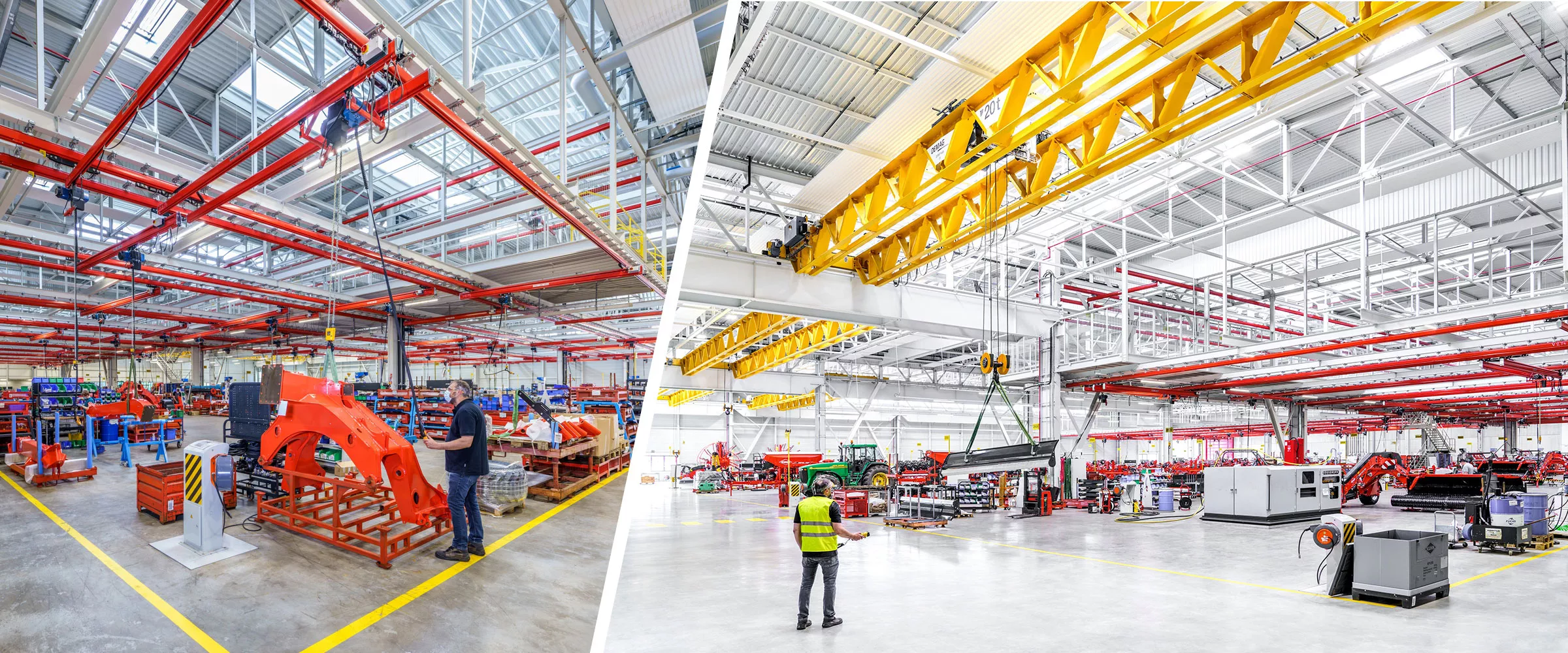
Maquinaria agrícola del norte de Francia
Flujo de material flexible y modular
Nueve grúas V-Type y 3,2 km de perfiles KBK con 120 polipastos de cadena DC para KUHN MGM SAS.
El grupo de empresas KUHN
En el noreste de Francia, cerca de Estrasburgo, se encuentra uno de los principales fabricantes de maquinaria agrícola del mundo. El Grupo KUHN promete a los agricultores capacidad innovadora y calidad a precios de mercado. Más de 5.000 empleados trabajan actualmente en numerosos centros de producción y distribución para mantener esta promesa en todo el mundo.
De Alsacia al mundo
La empresa comenzó con su fundador y homónimo Joseph Kuhn en 1828 como una herrería de pueblo. La herrería pronto se especializó en la fabricación de balanzas e instrumentos de medida. La empresa se trasladó a Saverne en 1864 y se especializó en la construcción de maquinaria agrícola. Desde entonces, sus actividades en la región de Saverne, incluido el municipio de Monswiller, se han centrado en el desarrollo, el perfeccionamiento y la mejora de segadoras, henificadoras, hileradoras, cortadoras de paja, equipos de labranza y sembradoras.
El proyecto
La producción de la planta principal de Saverne se ha ampliado varias veces en las últimas décadas y se ha adaptado a la cada vez mayor demanda de maquinaria agrícola. Sin embargo, el ancho de las naves, de un máximo de 15 metros, limitaba la producción, por lo que hace unos años se construyó una nueva planta de montaje en el municipio vecino de Monswiller. La abreviatura «MGM» significa «Montage Grande Machine» y explica que se necesitan anchos de nave de hasta 20 metros para montar las máquinas agrícolas de nueva generación. KUHN construyó una moderna nave de producción para la fabricación de grandes máquinas agrícolas.
En total, la planta de montaje fue ampliada en 20.461 m². En concreto, la ampliación consta de una nueva nave de montaje de 11.065 m², una ampliación de la nave de logística de 5.437 m² y 3.017 m² para una nave de expedición. Las zonas exteriores adicionales y la construcción de un nuevo comedor de empresa completan las instalaciones de la fábrica.
Distribución eficiente de la producción
La planta principal de Saverne produce maquinaria agrícola más pequeña y componentes para la MGM de Monswiller. Aquí se montan las máquinas más grandes que se utilizan para la henificación, el labrado y la siembra.
Estos componentes, así como las piezas compradas, se recogen en la zona de recepción de mercancías, el «Magasin», y se introducen en las líneas de montaje. Cada mes, en esta sección se manejan unas 100 toneladas de material. Las piezas compradas y otros componentes se recubren de polvo y se pintan en el propio taller de electrodeposición catódica (KTL) de la empresa. El montaje se realiza dentro de las líneas: La maquinaria agrícola se ensambla paso a paso en las estaciones de montaje individuales y, una vez realizado el montaje final y las pruebas de funcionamiento, se prepara para su envío.
Junto a la línea de montaje hay zonas de entrega para la intralogística. Los empleados necesitan una solución aérea para transportar la mercancía entregada desde el almacén y el taller de pintura hasta el lugar de montaje. Además, la manipulación del material en las diferentes estaciones de trabajo es crucial para enlazar con precisión los componentes y hacer que la manipulación sea lo más fluida posible para los empleados. Al ensamblar los subconjuntos al bastidor principal de la máquina agrícola, la precisión del polipasto en el posicionamiento y el control son de inmensa importancia para un trabajo eficaz. Por esta razón, las grúas ligeras son imprescindibles en cada paso de trabajo.
Al final de la línea de producción, las grúas universales ayudan en el montaje final. Según el tipo y el tamaño de la maquinaria agrícola, hay componentes voluminosos y pesados que deben montarse en el bastidor principal y, por lo tanto, también deben ser levantados y colocados. Por último, se lleva a cabo una prueba de funcionamiento y las máquinas agrícolas ya terminadas se transportan a la nave de expedición recién construida. Una vez allí, las grúas se encargan de cargar los camiones.
La solución
La ampliación de la producción conlleva la ampliación del concepto de flujo de material en KUHN MGM: a lo largo de las nuevas líneas de montaje y en la expedición se utilizan 9 grúas puente del tipo ZVKE con viga V-Type y una capacidad de carga respectiva de 20 toneladas, así como 120 polipastos de cadena del tipo DC-Pro. Con una ampliación de 3,2 kilómetros de perfiles KBK, la nueva línea de montaje también estará plenamente cubierta con el sistema de grúas ligeras.
KUHN MGM y Demag en Francia programaron las entregas para que las nuevas grúas pudieran ser montadas en secciones y a tiempo. El montaje de los sistemas de grúas ligeras fue realizado por el propio personal de mantenimiento de la empresa tras una exhaustiva formación.
Modular, seguro y eficiente: el sistema de grúa ligera KBK
En las líneas de montaje en Monswiller, una densa red de grúas ligeras KBK se extiende por el cielo de la nave de producción. Los empleados utilizan las grúas KBK de una y de dos vigas para trasladar de forma aérea los componentes de la maquinaria agrícola desde la línea logística hasta las estaciones de montaje de las líneas de producción, que tienen unos 100 metros de largo y 25 metros de ancho. A la hora de planificar la fábrica, se prestó atención a que el sistema KBK ocupara toda la superficie y, por tanto, estuviera disponible para respaldar todas las fases de trabajo.
Como polipastos se utilizan polipastos de cadena DC-Pro, que trabajan manualmente para capacidades de carga de hasta 1000 kg y eléctricamente para capacidades de carga de hasta 2000 kg. El transporte de los componentes es perfectamente fluido en el lugar de montaje con ambos tipos de accionamiento, por lo que las máquinas agrícolas pueden montarse de forma eficiente y ergonómica. Las conexiones articuladas entre la viga de la grúa y el mecanismo de traslación permiten una manipulación fluida de los conjuntos premontados desde la estación de montaje hasta el bastidor de la máquina. Las velocidades parcialmente sin escalonamiento y bajas de los polipastos de cadena DC-Pro permiten a los operadores de la grúa alinear los conjuntos con facilidad y precisión durante el montaje. De este modo, el montaje de un voluminoso rodillo para el labrado puede llevarse a cabo del mismo modo que el montaje de una unidad electrónica o hidráulica.
Confort y seguridad en la manipulación de cargas con el polipasto de cadena DC-Pro
La compatibilidad de los componentes Demag entre sí permite también a KUHN MGM utilizar polipastos de cadena de generaciones anteriores de su inventario, por ejemplo, del tipo DK o incluso PK. Sin embargo, el personal se ha acostumbrado a las ventajas de la última generación del tipo DC-Pro: el posicionamiento de los componentes con dos velocidades es absolutamente preciso, incluso a bajas velocidades. Con capacidades de carga de 500 a 2000 kg y un recorrido del gancho uniforme de 5 metros, los polipastos de cadena pueden utilizarse de forma flexible en todas las estaciones de trabajo. El cable de mando ajustable en altura de las botoneras de mando DSC utilizadas ofrece la máxima ergonomía. La forma ergonómica de la empuñadura y el hecho de usar el mismo modelo en todas las estaciones de trabajo aumentan la eficacia durante el montaje.
El polipasto de cadena DC-Pro está provisto con un reductor, un acoplamiento de fricción y frenos de alta calidad que no precisan mantenimiento durante 10 años. En combinación con la desconexión automática del acoplamiento de fricción y el frenado automático en caso de fallo del mando, los empleados de KUHN pueden confiar en la fiabilidad del DC-Pro en su lugar de trabajo. Las funciones relativas a la seguridad del tipo de polipasto de cadena cumplen, como mínimo, el nivel de rendimiento c y la categoría 2 según EN ISO 13849-1.
Fiabilidad operativa absoluta con una alta eficiencia
Las nueve grúas puente de dos vigas ZVKE con viga V-Type suministradas también ofrecen la máxima seguridad del servicio y eficiencia operativa. El diseño V-Type de las juntas de membrana de la viga de la grúa permite una gran permeabilidad lumínica en la nave. Debido a una menor necesidad de material, la innovadora viga de la grúa tiene un peso propio menor, lo cual repercute positivamente en la estática de la nave. Las luces de las grúas puente oscilan entre 10,4 y 28,3 metros.
«Vi la grúa por primera vez en otro cliente suyo y quedé inmediatamente impresionado. La viga puente casi no se ve, ya que deja pasar mucha luz a la nave. Esto también da la impresión de que la grúa es muy ligera». - Stéphane Schissele, KUHN SAS
Con una capacidad de elevación de 20 toneladas cada una, KUHN MGM podrá elevar en el futuro maquinaria agrícola más grande y pesada para su montaje final y transportarla para su envío. Cinco grúas apoyan los pasos finales de montaje al final de la línea de producción para unir los componentes premontados, que son ahora considerablemente más pesados. No sólo la potencia de elevación, también el posicionamiento preciso de los componentes gracias al sistema de mando sin escalonamiento representa una enorme agilización del trabajo.
Otros cuatro ZVKE están desplegados en la zona de expedición recién construida y cargan en camiones los paquetes de componentes ya embalados y la maquinaria agrícola. Los envíos de Monswiller se realizan a clientes de todo el mundo.
El polipasto de cable modular Demag DMR permite la integración de elementos mecánicos y eléctricos. El mando regulado por variador de frecuencia de las grúas desempeña un papel importante en la comodidad y permite a los operadores en la zona de expedición recoger y mover con precisión los palets con componentes de una maquinaria agrícola o máquinas agrícolas ya completas. La aproximación y la aceleración se realizan sin escalonamientos, de modo que el operador puede controlar con precisión el movimiento de la grúa, el carro y el polipasto y puede concentrarse mejor en la utilización del espacio de carga en el camión al cargar.
Seguridad en el servicio de la grúa
En las nueve grúas, el sistema de control de seguridad inteligente SafeControl supervisa y asegura el servicio en todo momento. Una desconexión en dos etapas evita que tanto la grúa como el carro choquen con los topes de extremo. Al alcanzar el primer final de carrera, la traslación de la grúa o del carro pasa a la velocidad de traslación de precisión. En cuanto se alcanza el segundo final de carrera, se desconectan los accionamientos de la grúa o del carro y se frena suavemente la marcha. La oscilación de la carga se evita mediante la combinación de un control sin escalonamiento e interruptores de final de carrera, de modo que la carga no sufra ningún percance y no pueda causar ningún daño en el camión o en el área circundante. El operador de la grúa se beneficia de la asistencia electrónica que le respalda y protege en situaciones imprevisibles.
Dos de los ZVKE se desplazan por una vía de rodadura en la nueva sección de producción. Para evitar colisiones, se utiliza un dispositivo anticolisión óptico: sensores láser dobles miden de forma redundante la distancia entre las respectivas grúas en la vía de la grúa y si se rebasa la distancia predefinida, la correspondiente grúa se desconecta en dos etapas y queda asegurada. En la primera etapa, la grúa sólo se puede desplazar a baja velocidad, en la segunda etapa la grúa se desconecta de forma segura. Este concepto de desconexión de seguridad independiente con hardware de dos canales corresponde a la categoría de seguridad 3 según la norma EN 13849-1.
Los estados de servicio siempre a simple vista
El operador siempre puede saber el peso de la carga en el gancho con el Demag StatusBoard en la viga de la grúa. Además, el StatusBoard muestra el estado de servicio actual de la grúa en tiempo real. Como la capacidad de carga, la carga total, la sobrecarga, la información de servicio o las funciones de asistencia y confort activadas del control de seguridad SafeControl: un funcionamiento transparente y, sobre todo, seguro de la grúa.
Particularidades
Las instalaciones modulares KBK permiten a KUHN MGM aplicar el sistema de grúas en el lugar de trabajo proyectado y podrá además ser ampliado en cualquier momento si es necesario. Pescantes giratorios de columna y murales transportan los componentes por toda la zona. Las versiones KBK en acero y aluminio se adaptan perfectamente a las distintas necesidades y también pueden combinarse posteriormente.
El suave funcionamiento de los componentes Demag permite una manipulación rápida y segura y, al mismo tiempo, un posicionamiento preciso y sin esfuerzo de las diferentes piezas para su montaje. El sistema de grúas ligeras garantiza así un flujo de trabajo eficaz y aumenta la productividad y la eficiencia.
La construcción del perfil con viga V-Type y con juntas de membrana permite ahorrar peso propio y, por tanto, tiene un efecto positivo en la estática de la nave. El control de seguridad inteligente SafeControl ofrece la mayor seguridad posible durante el servicio de la grúa. Los interruptores de final de carrera de la grúa y el sistema de detección visual de las grúas apoyan al operador electrónicamente y ayudan a evitar daños involuntarios en el entorno de trabajo de la grúa. En combinación con el control sin escalonamiento del desplazamiento de la grúa y del carro, así como de los movimientos de elevación, el manejo de la grúa resulta aún más cómodo.
Entrevista
Entrevistamos a Stéphane Schissele, Director de Construcción y Mantenimiento, en KUHN MGM SAS, en Monswiller (Francia).
Demag: Señor Schissele, ¿podría presentarnos brevemente la empresa KUHN MGM SAS y el emplazamiento de Monswiller?
Stéphane Schissele (KUHN MGM SAS): Monswiller se encuentra en el departamento del Bajo Rin que forma parte de Alsacia. Nuestra empresa está firmemente arraigada en esta región y ahora está representada por dos sedes, Saverne y Monswiller. La planta de producción y montaje de Saverne es la sede del Grupo KUHN. En Monswiller está ubicada la planta de montaje de MGM y la producción de piezas de recambio. Las siglas «MGM» provienen de «Montage Grande Machine». Aquí se montan las máquinas más grandes.
La planta de montaje se inauguró en 2008 con cuatro líneas de montaje y hasta el momento ha tenido una producción anual de 9.000 máquinas. Con la ampliación, se duplicó la capacidad del emplazamiento. Actualmente, 350 empleados se encargan de fabricar maquinaria agrícola para henificar, labrar y sembrar. Además, MGM está especializada en la producción de máquinas de temporada.Demag: ¿Por qué razones era necesaria la inversión en el lugar?
Sr. Schissele: En primer lugar, era importante para nosotros aumentar la capacidad de producción de cuatro a ocho líneas de montaje. A la par, hemos incorporado una zona propia para la logística y hemos completado el proceso de fabricación con una nueva nave de expedición en Monswiller. Además, nuestra pretensión es poder amoldarnos dinámicamente a las necesidades siempre cambiantes de nuestros clientes. Hace unos años, nos las arreglábamos en Saverne con anchos de nave de 14 o 15 metros. Sin embargo, con el paso de los años, han quedado demasiado estrechos para nuestras necesidades, por lo que ahora tenemos 20 metros de ancho para poder trabajar en las líneas de montaje en esta ubicación. Esto es de gran importancia para nosotros, ya que las máquinas son cada vez más grandes y anchas. Por tanto, la producción necesitaba más espacio.Por estas razones, la construcción de la nueva fábrica y la reciente ampliación eran esenciales para nosotros y proporcionan el entorno de producción adecuado para los próximos años.
Demag: ¿Puede darnos una idea de la magnitud de la expansión?
Sr. Schissele: Hemos llevado a cabo una ampliación de casi 20.000 m² para áreas productivas como el montaje, la logística y la expedición.
Demag: ¿Qué tareas realizan los productos Demag?
Sr. Schissele: Los productos Demag se encargan de la manipulación de materiales en las distintas estaciones de trabajo en la planta. El sistema de grúa ligera KBK requiere poco esfuerzo por parte de nuestros empleados para transportar los componentes a nuestro taller de pintura KTL y durante el premontaje. Los polipastos de cadena instalados en las instalaciones KBK suelen tener una capacidad de carga de entre 500 kg y 1.000 kg y se utilizan para manipular y posicionar componentes durante el montaje. Una vez premontados los conjuntos, necesitamos los polipastos para transportar estos conjuntos al bastidor principal de la máquina. La velocidad baja y parcialmente sin escalonamiento de los polipastos de cadena Demag DC-Pro ayuda a nuestros empleados a alinear los conjuntos de montaje con facilidad y precisión.
«Montaje preciso del conjunto gracias a las velocidades bajas y continuas de los polipastos de cadena Demag DC-Pro».
Al final de las líneas de montaje, el ensamblaje final de las máquinas se realiza con grúas V-Type con una capacidad de carga de 20 toneladas.
Demag: ¿Qué requisitos específicos exigió KUHN a los productos Demag?
Sr. Schissele: Para nosotros, la alta seguridad de funcionamiento de los componentes es enormemente importante para garantizar la máxima seguridad para el personal de servicio. Al ser socios de Demag desde hace ya varias décadas, somos conscientes de la durabilidad de los productos y así lo exigimos.
Demag:¿Por qué KUHN ha decidido optar por las soluciones de estaciones de trabajo de Demag?
Sr. Schissele: En Saverne, seguimos usando una gran flota de polipastos de la generación PK (nota del editor: los polipastos de cadena de la serie PK se fabricaron de 1961 a 1995). Por tanto, la larga vida útil de los productos es bien conocida por nosotros. A lo largo de las últimas décadas, polipastos de cadena de varias generaciones se han utilizado a diario y siguen siendo plenamente funcionales. Cuando nuestros empleados nos hacen saber que las velocidades de elevación variables serían útiles para su trabajo, actualizamos los polipastos con dispositivos de la nueva generación de DC. Hemos probado otros productos, pero la velocidad en los productos Demag es perfectamente adaptable para que el encaje de los componentes sea cien por cien preciso. La ganancia en precisión está plenamente comprobada con los polipastos Demag.
«La ganancia en precisión está plenamente comprobada con los polipastos Demag».
Otra razón es que los productos se pueden manejar fácilmente a mano. Los polipastos circulan casi exclusivamente por varios kilómetros de perfiles KBK. Como ya se ha mencionado, los polipastos de cadena tienen una capacidad de carga de hasta 1.000 kg, por lo que podría pensarse que transportarlos a mano podría ser difícil: ¡Pero la suavidad del KBK es realmente impresionante! En Saverne y Monswiller, cargas de hasta 1.000 kg y envergaduras de hasta 7 metros pueden moverse manualmente sin problemas. Cuando se trata de cargas de 2.000 kg o más, es necesario, por supuesto, un accionamiento eléctrico.
«(...) ¡la suavidad del KBK es realmente impresionante!»
Es igualmente indispensable para la planificación y la flexibilidad de la producción que podamos adaptar la disposición de los lugares de trabajo. Es posible en cualquier momento modificar o ampliar las instalaciones KBK, en algunos casos, las grúas de las distintas líneas de producción se desmontan y se vuelven a montar 30 o 40 veces al año, por ejemplo, para cambiar de sentido. El sistema KBK está aquí instalado en Monswiller de tal forma que pueda cubrir la mayor superficie posible. Nunca podemos asegurar con antelación si la cadena de montaje permanecerá igual durante ocho o diez días. Los requisitos pueden cambiar incluso a diario. Hace 20 años se ensamblaban 1.000 máquinas en una línea, ahora puede haber 80, 60, 50, a veces sólo 40 máquinas. Las series son cada vez más pequeñas, lo que significa que las líneas tienen que ser muy flexibles. Y, por tanto, también las vías para grúas.
La solución que utilizamos con KBK desde hace más de dos décadas es la mejor para nosotros. Nos acercamos a la línea con las piezas y los empleados pueden transportar fácilmente los componentes al lugar de trabajo para su montaje. Estas van de estación de trabajo en estación de trabajo y a lo largo de las líneas de producción de 100 metros de largo hasta que podemos probar la máquina agrícola terminada al final de cada línea y prepararla para su envío. Las grúas Demag V-Type sirven de apoyo para el montaje final y la manipulación de los productos acabados.
Demag: ¿Qué le parece el diseño V-Type de las vigas de la grúa?
Sr. Schissele: Esto es realmente una novedad. Conocemos los KBK desde hace años, pero el perfil en V de las grúas es realmente una innovación. Vi la grúa por primera vez en otro cliente suyo y quedé inmediatamente impresionado. La viga puente casi no se ve, ya que deja pasar mucha luz a la nave. Esto también da la impresión de que la grúa es muy ligera.
El reducido peso propio de la grúa tiene, lógicamente, un efecto positivo en la estructura metálica de la nave. Además, el diseño es realmente atractivo. Si además se consideran las especificaciones técnicas, la capacidad de carga disponible a pesar del bajo peso propio y la velocidad, se obtiene una solución que es realmente extraordinaria. Por supuesto, esto también repercute en el menor desgaste de las ruedas y de los carriles, lo que supone un efecto muy positivo en los costes para nosotros. También hicimos algunos cálculos con sistemas de la competencia, pero estos son más pesados y altos debido a los perfiles convencionales de las grúas, lo que habría hecho que la vía de rodadura de la grúa fuera mucho más alta. La diferencia era de hasta un metro en algunos casos. Esto simplemente no nos convenía y por eso nos decidimos por el diseño innovador.«La grúa V-Type es realmente un gran producto. Por ello, nos decantamos inmediatamente por el nuevo diseño y no nos ha decepcionado».
Las grúas también nos serán de gran utilidad de cara al futuro y, con una capacidad de carga de 20 toneladas, son actualmente de un tamaño mayor del que necesitamos. Sin embargo, como hemos constatado en los últimos tiempos, nuestras máquinas son cada vez más grandes y, por lo tanto, más pesadas, y un margen en la capacidad de carga de 5 toneladas no supuso una diferencia en términos de precio.
Demag: Demag: ¿Cómo se garantiza que el sistema esté disponible en todo momento?
Sr. Schissele: La gestión simplificada de las piezas de recambio es una gran ventaja. Pedimos un gran número de piezas de repuesto directamente a través del la Demag Shop. Un sistema rápido y eficaz en el que también se puede ver el número de suspensiones KBK y comprobar los planos. Realmente bueno. Y después de la simulación, se pueden pedir los productos directamente. Lo hacemos muy a menudo y el proceso, desde la recopilación de información hasta la selección y la entrega, es siempre extremadamente rápido. Ya solía utilizar el catálogo para encontrar los mejores productos de forma eficaz y rápida. El Demag Shop lo ha simplificado todo aún más.
Disponemos de un almacén con productos Demag en ambos centros de producción y, por tanto, un suministro centralizado de piezas de recambio. Aquí se almacenan productos de más de 25 años y casi todos son compatibles entre sí, lo que supone una gran ventaja para nosotros y ayuda a mantener la flexibilidad.
Demag: ¿Planificó también la ampliación de la producción a través de Demag Shop?
Sr. Schissele: La configuración de los proyectos más pequeños, de hasta unas tres grúas. Eso funciona muy bien. Pero cuando se trata de un proyecto integral, siempre es mejor tener un socio que nos apoye y con el que podamos planificar el proceso. El equipo de ventas de Demag fue muy, muy eficaz en este proyecto. Las piezas llegaron sector por sector. Las piezas estaban ya clasificadas, de modo que todos los componentes KBK y los polipastos necesarios se ensamblaron en el sector correspondiente. Previamente comentamos los plazos de entrega y en cada periodo de las diferentes semanas naturales, llegaron los paquetes. Esto significaba que no necesitábamos un gran almacén temporal in situ y que nuestros empleados podían montar el sistema directamente después de la entrega.
«Estamos completamente satisfechos con las soluciones de Demag».
Demag:¿Qué ventajas hablan a favor de las soluciones de Demag?
Sr. Schissele: Los productos Demag ofrecen una gran flexibilidad y permiten la fabricación de conjuntos complejos en un espacio reducido. La durabilidad de los productos es excelente. La capacidad de carga también es muy buena y los componentes pueden seguir siendo encargados después de 20 o 30 años sin ningún problema. Nuestros altos estándares de seguridad del servicio también se reflejan en los productos Demag. «Estamos plenamente satisfechos con las soluciones de Demag».
Demag: ¿Qué impresiones le han transmitido hasta ahora los empleados sobre el trabajo con los productos Demag?
Sr. Schissele: El personal está muy contento. Puede transportar los componentes con gran rapidez. Pero la mayor ventaja es que el posicionamiento para el montaje de subconjuntos es absolutamente preciso y eficaz. Tanto con el sistema de grúas ligeras en las estaciones de trabajo como con las grúas al final de las líneas de montaje y en la expedición.
Galeria de imagens
Galeria de imagens
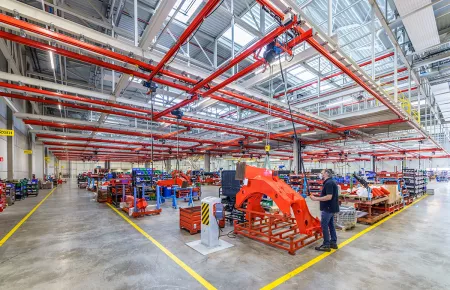
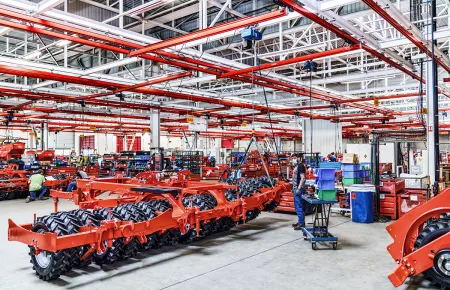
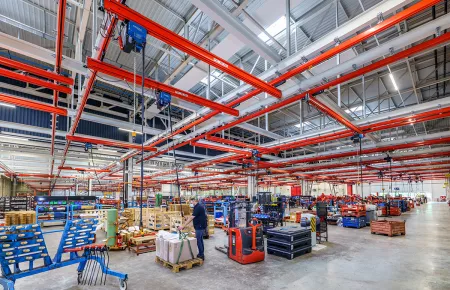
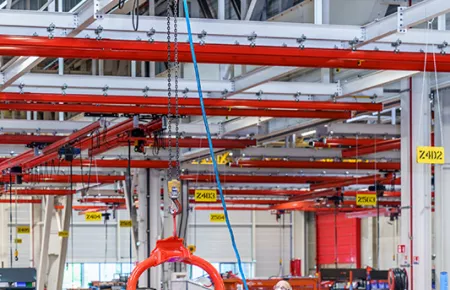