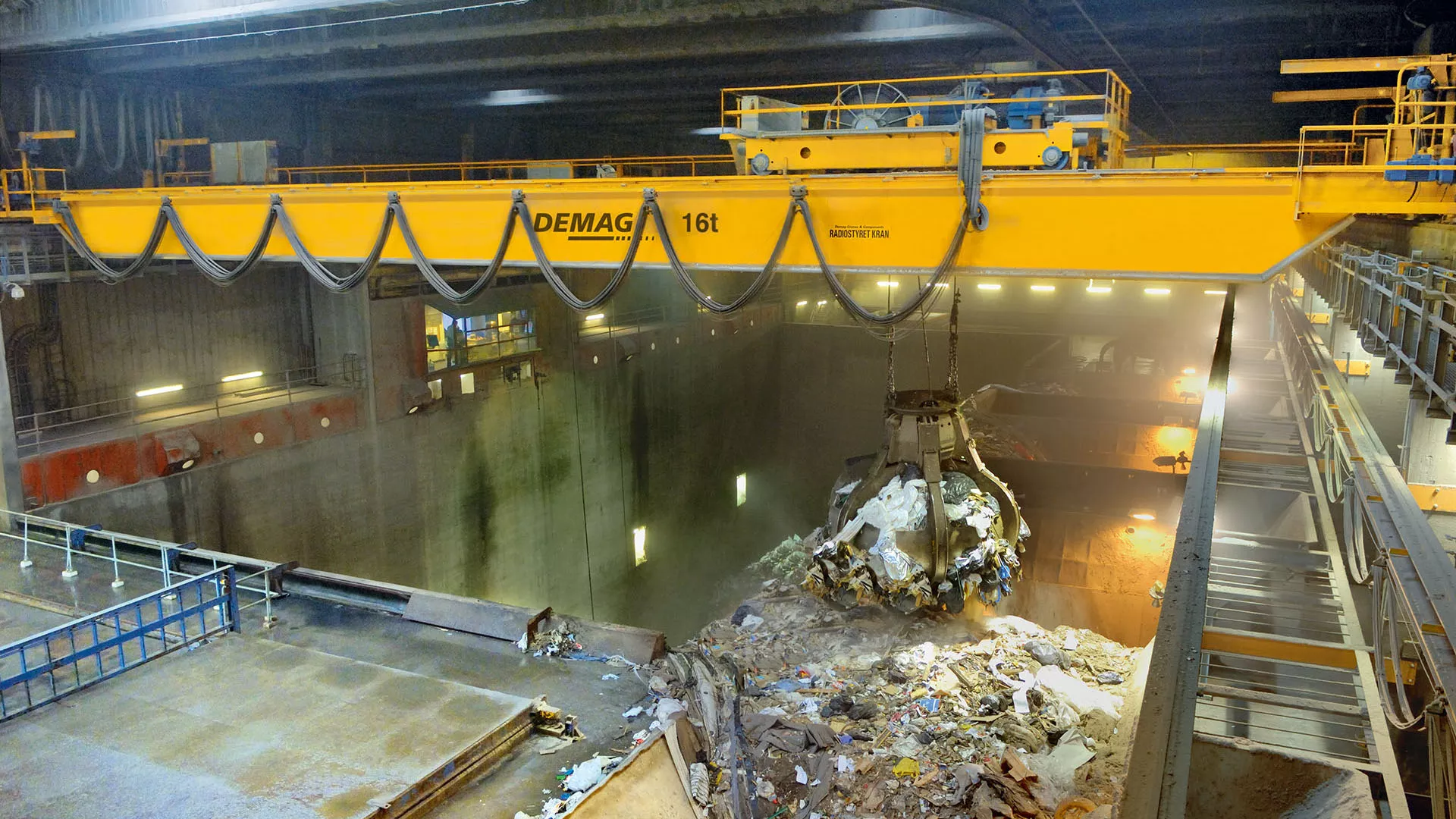
Maximum efficiency for high handling rates
Amagerforbraending
Requirements in automated refuse incineration facilities
High material handling rates in automatic operation 24/7 without a crane operator.
The Danish Amagerforbraending company processes refuse to generate electricity and supply district heating. Some 500,000 people live in its catchment area in the south of the capital Copenhagen. Besides recycling stations, Amagerforbraending operates a refuse incineration facility. The crane systems used in the facility, which was built in 1970, were fully automated in 2007.
- Some 430,000 t of refuse are incinerated every year
- Output: more than 1 million MWh of energy and district heating output to supply 140,000 households every year
- Four furnace lines each incinerate 17 t of refuse per hour
Maximum efficiency for high handling rates
Maximum efficiency was required in the material handling operation to process the constantly increasing amount of refuse and to ensure that the incineration lines are fed continuously. After the crane installations were fully automated, the former crane personnel was to be to utilised at qualified positions in the company.
Increased handling rates
- Both crane installations operate in independent working areas
- High handling rates are required in order to clear the tipping areas and to provide adequate blending of the material
- The crane installations have to achieve high operating speeds in all three motion axes without any sway of the grab
24/7 automatic operation
- Fully automatic control of the crane installations around-the-clock – without a crane operator
Maximum availability
- All furnace lines can be served by only one crane in an emergency
- Extended maintenance intervals
- Minimised damage to the grabs that may occur in manual operation
Continuous feed to the furnaces
- Maximum blending of the refuse before it is fed to the furnaces to ensure that a constant incineration rate is achieved for the furnace lines
- Furnaces are fed with refuse for incineration to Schedule
The crane installations were initially equipped for automatic operation, which was only used at certain periods of time, however. In a further step, the Process Cranes were converted to fully automatic operation without any crane operators:
24 hours per day, 7 days per week.
- Double-girder crane design
- Powered multiple shell hydraulic grab of low-maintenance design
- Load capacity: 16 t
- Span: 29.5 metres
- Frequency inverter-controlled long and cross-travel motions
- Load-dependent hoist speeds
- Active load sway damping system
- Spiral winding cable drum to supply power to the grab
A computer with a visualization system was additionally installed as an operator interface. This system
ensures that the personnel are continuously provided with information on the current position and status of
the cranes. The owner can program operation of the installation himself by means of configurable storage
and filling strategies and, in this way, optimise management of the bunkers. Capacity was increased by 30% after these modifications had been carried out.
Feeding operation and strategies
Continuous feed to the furnaces
Delivery of the refuse is controlled by a traffic light and gate system. During the truck unloading operation, this arrangement ensures that the area next to the corresponding gate remains blocked for the cranes so that the grabs are not buried beneath falling refuse. The refuse is delivered by some 450 vehicles every day.
Blending program
The installation features blending programs and storage strategies to achieve uniform incineration and, as a result, the most constant calorific value possible. For example, the cranes create conical heaps of bulk material when the tipping positions have been cleared, which ensures optimum blending of the refuse.
Start-up strategy
After maintenance work has been carried out, the cranecontrol system supports start-up of the incineration linewith a strategy that gradually increases the amount of material which is handled.
Serving the bunker chutes
The feed process is controlled by a program and adapted to the various bunker chutes. Since the individual lines are fed independently, bridges of refuse are not created and blockages do not form in the bunker chutes, which optimises the material flow.
Technical data
Demag crane
- Double-girder open-winch cranes
- Type ZKKW (16 t x 29.5 m)
- MPW open winch crab
- Hoist speed: 0 – 80 m/min. (with load) / 0 – 95 m/min. (w/o load)
- Cross-travel speed: 0 – 90 m/min.
- Long-travel speed: 0 – 90 m/min.
- Lifting height: 34 m
Handling rates
- 4 furnaces fed by 2 cranes (without any blending operations): 68 t / hour
- Clearing, blending and storage by 2 cranes: 240 t / hour
- Combined handling rate of 2 cranes: 308 t / hour
Grab
- Type: Powered multiple shell grab
- Capacity: 8 m³
- Dimensions: 5.00 m open; 3.12 m closed
- Opening time: 8 seconds
- Closing time: 15 seconds